Six Ways Maintenance Professionals Can Use Root Cause Analysis to Improve Equipment Performance
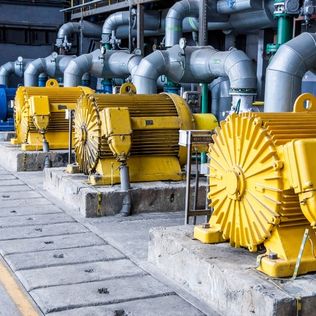
What Are the Six Ways to Improve Equipment Performance?
The following article explains six ways maintenance professionals can use root cause analysis to improve performance. There are more than six ways to improve performance, but we will only cover six ways.
Also, you can only get all six ways if you use advanced root cause analysis—TapRooT® RCA. Why? TapRooT® RCA includes the advanced Equifactor® Troubleshooting Tools, based on Heinz Bloch’s techniques, which have been proven in the process industries.
So read on to find out more about how maintenance professionals can use advanced root cause analysis to:
- Stop equipment repeat failures.
- Improve uptime statistics.
- Improve equipment troubleshooting efficiency.
- Analyze the causes of maintenance-related safety incidents.
- Develop maintenance and operations practices for new equipment.
- Help operations with process troubleshooting.
Stop Equipment Repeat Failures
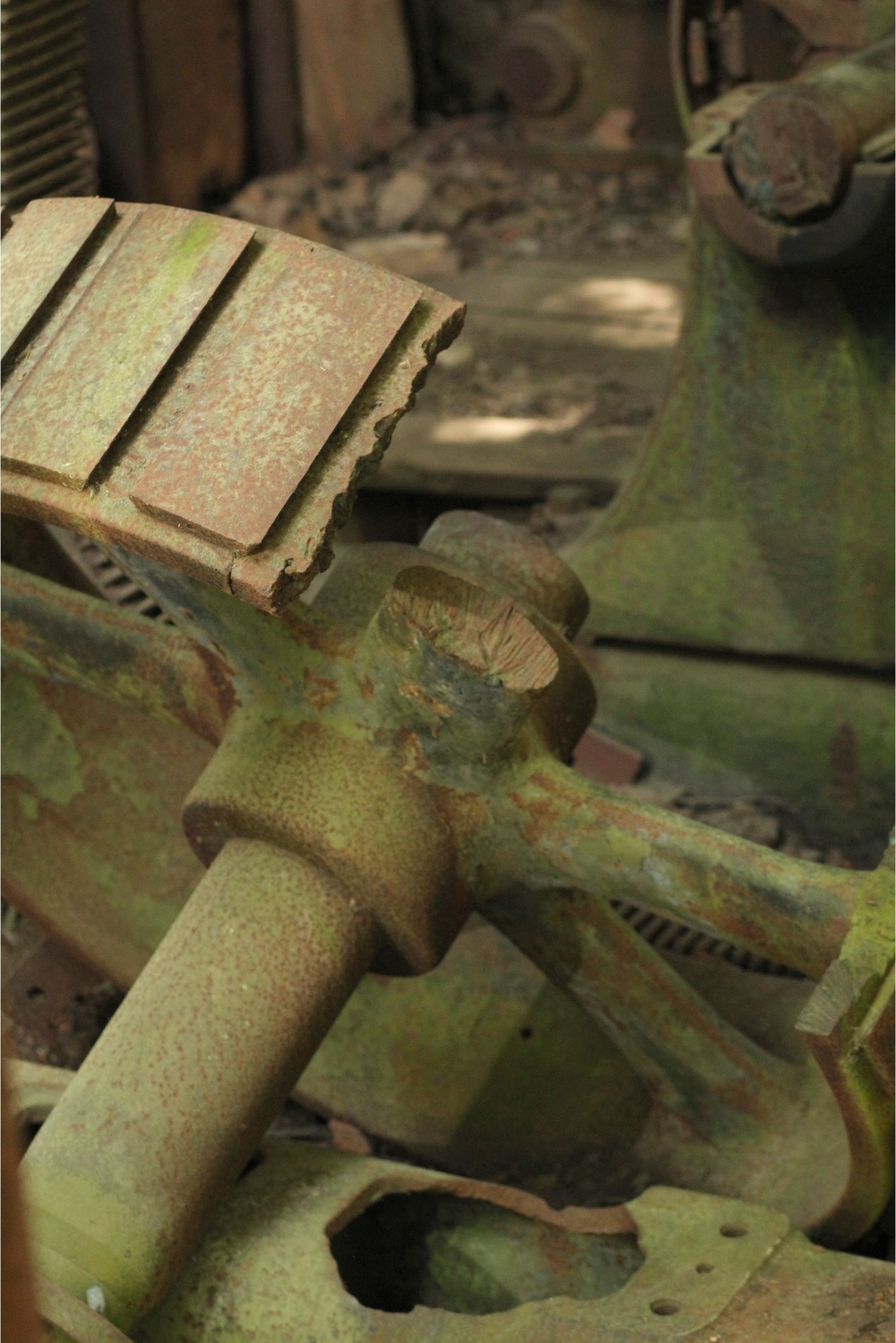
We have already written extensively about this topic. So, I will refer you to two previous articles and a video…
That should show you how to use Equifactor® Troubleshooting Techniques and TapRooT® Root Cause Analysis to analyze and stop repeat equipment failures by fixing their root causes. It should also convince you that the proprietary Equifactor®/TapRooT® Tools make this analysis and corrective action process so successful.
Improve Uptime Statistics
Improving your uptime statistics (or reducing downtime) is a fairly simple process once you start using Equifactor® Troubleshooting and TapRooT® RCA to analyze and fix your equipment issues. You simply look for your biggest causes of downtime and analyze the failures using Equifactor® Troubleshooting and TapRooT® Root Cause Failure Analysis.
You can even proactively address critical equipment failures by using the Equifactor® Troubleshooting Tables to identify what could cause equipment failures and proactively improve processes, maintenance practices, operating practices, and equipment procurement.
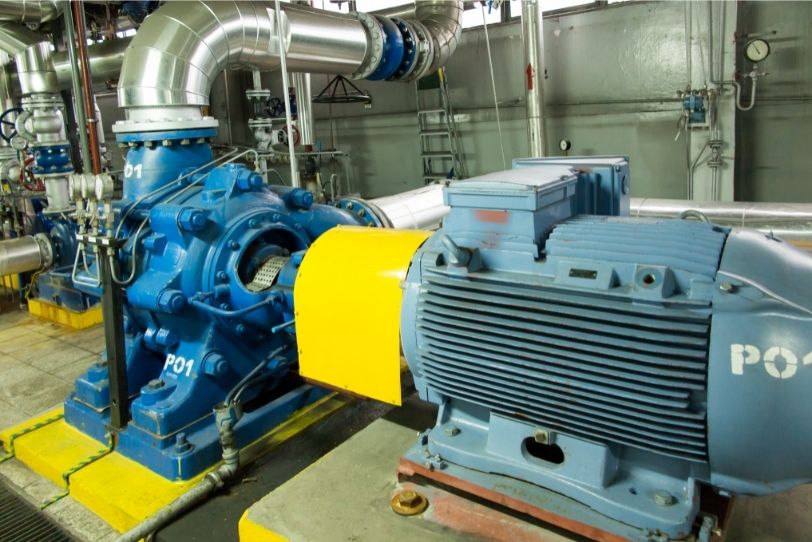
Improve Equipment Troubleshooting Efficiency
One of the first surprises we discovered when working with Heinz Bloch to develop the Equifactor® Troubleshooting Tables was that, in general, people were failing to find the root causes of equipment failures because they weren’t doing a good job troubleshooting equipment failures.
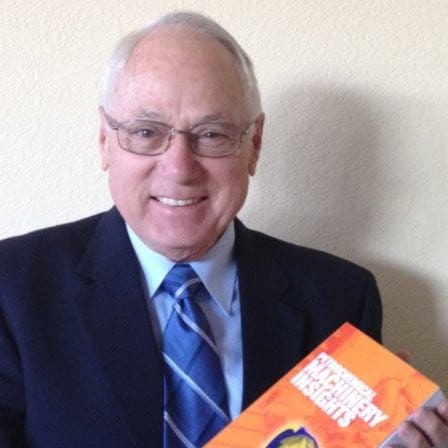
Since they didn’t know what caused the issue, they couldn’t identify the failure’s root causes, and therefore, their corrective actions were largely ineffective.
That troubleshooting failure made the efforts very inefficient. Perhaps people would guess the right answer, but a large portion of the time, the fixes didn’t work, and problems happened over and over again.
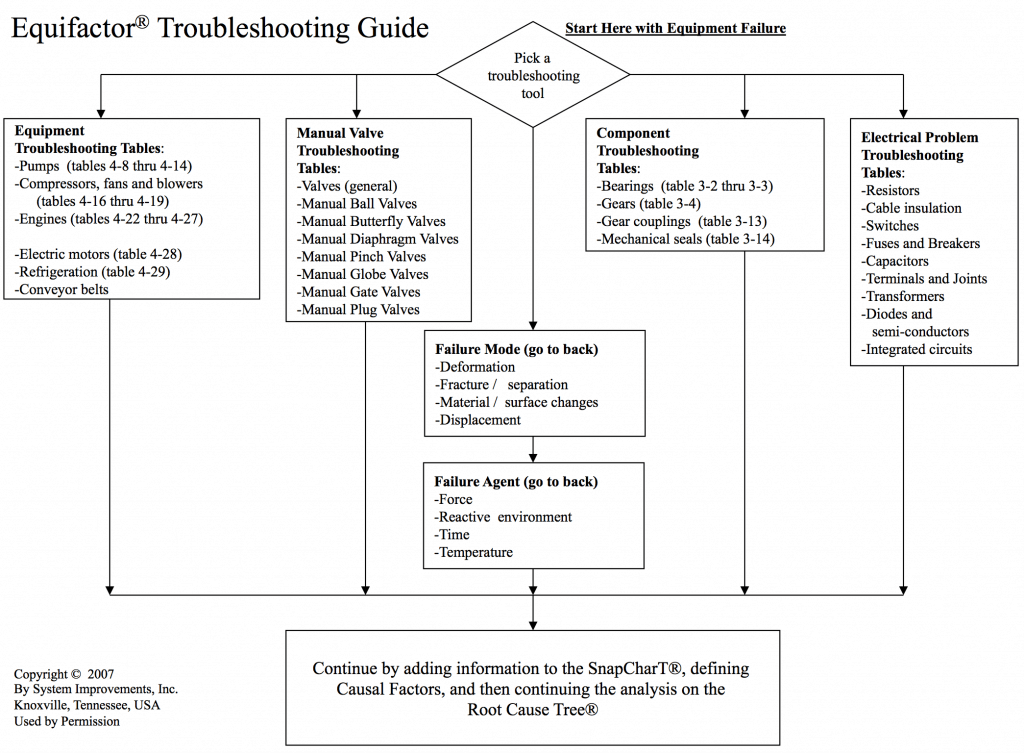
The answer is to teach your field personnel to use an effective troubleshooting tool (Equifactor®). We can do this training in a day at your site in our Equifactor® Troubleshooting Course.
This article explains who needs troubleshooting training and who also needs root cause analysis training…
The results can show a fantastic improvement in the efficiency and effectiveness of your troubleshooting efforts. Combined with TapRooT® Root Cause Analysis for your more significant equipment problems, you have a one-two punch to improve equipment performance.
Analyze the Causes of Maintenance-Related Safety Incidents
Studies and experience show that the more unscheduled, unplanned corrective maintenance (as opposed to scheduled/planned preventative maintenance) a company performs, the higher the rate of injuries to maintenance personnel. Thus, the first way to reduce maintenance safety-related incidents is to reduce unscheduled, unplanned maintenance by improving equipment reliability (discussed above).
However, you can use the tools (TapRooT® Root Cause Analysis) you used to investigate the root causes of equipment failures to analyze the root causes of human errors that cause safety-related incidents (lost-time injuries or fatalities).
Using the same tool for equipment failures and safety incidents is a great way to get more for your training dollar because TapRooT® RCA is so effective for both types of investigations.
Develop Maintenance and Operations Practices for New Equipment
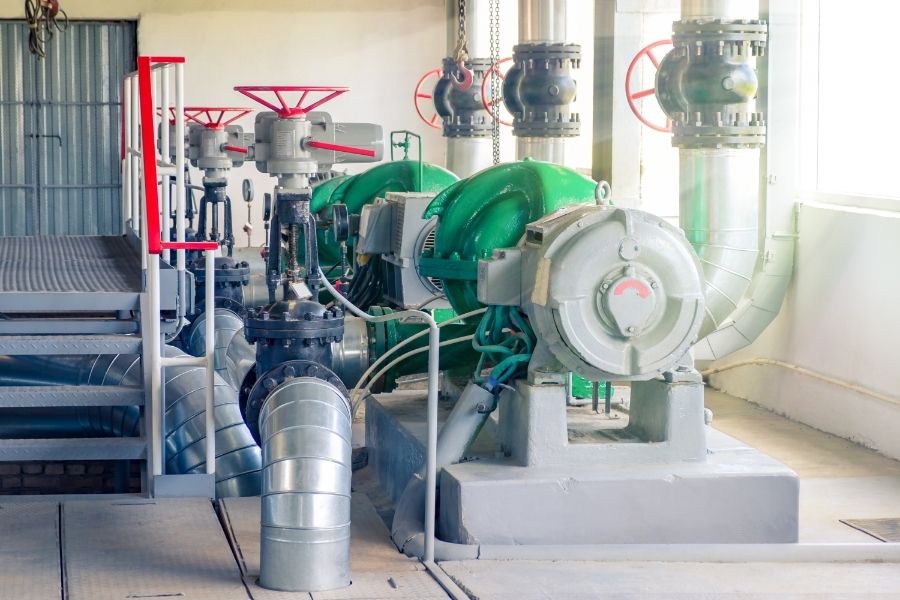
We mentioned this in the section on improving uptime statistics above. You can simply use the Equifactor® Troubleshooting Tables to develop practices for improving equipment performance.
For example, many equipment failures are caused by improper operation. Thus, developing effective procedures and effective operator training can significantly improve equipment reliability.
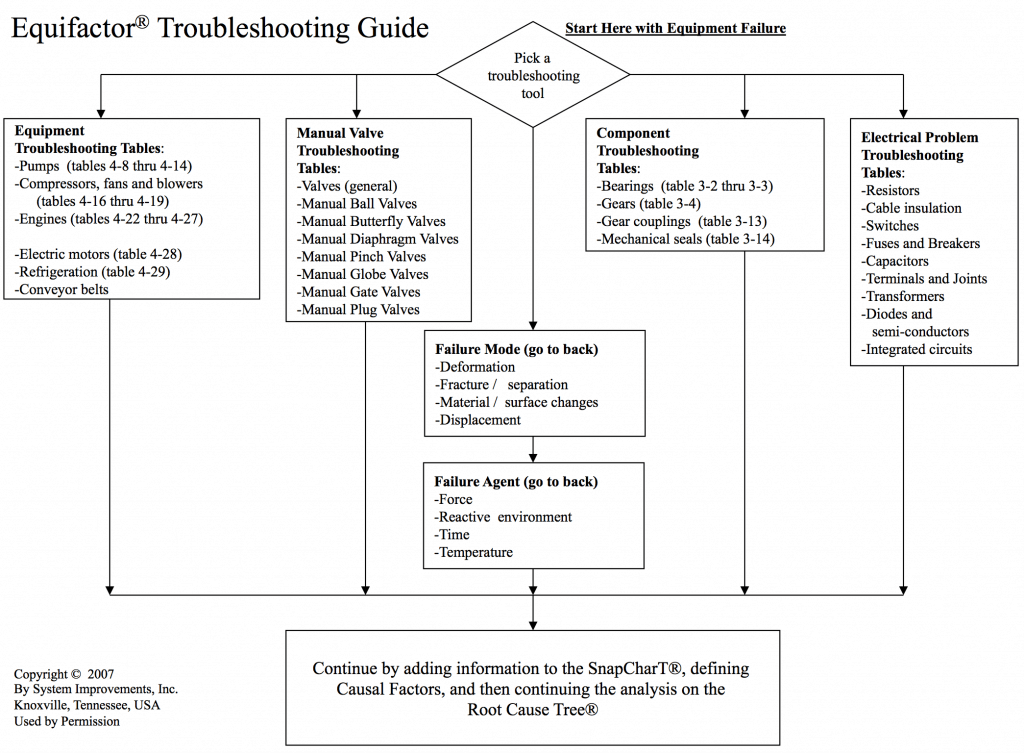
You can use the Equifactor® Troubleshooting Tables to discover operating practices that could lead to failures. This analysis can suggest ideas for improvement, including equipment installation practices, operating procedures, and operator training.
Help Operations with Process Troubleshooting
As mentioned above, many maintenance issues are caused by operating issues. Thus, equipment troubleshooting problems can become process troubleshooting problems.
You can customize the computerized Equifactor® Troubleshooting Tables by adding specific tables for your unique equipment and processes. This customization can improve your troubleshooting effectiveness (as mentioned above) and make the best troubleshooting techniques available to all your personnel.
Below is a video of one of our Equifactor® Users, Don Brooks, explaining how this helped them improve the reliability of one of their processes with unique equipment that wasn’t included in the Equifactor® Troubleshooting Tables.
Learn to Use These Best Practices
Learn to use Equifactor® Troubleshooting and the TapRooT® Root Cause Analysis System in our 2-Day Equifactor® Troubleshooting and TapRooT® Root Cause Analysis Course. What’s in the course? Here’s the course outline:
Course Outline
DAY ONE
- Introductions
- Understanding What Happened – SnapCharT® Basics
- SnapCharT® Exercise
- Collecting Information
- Failure Modes and Failure Agents
- Equifactor® Troubleshooting Tables
- Human Errors
- Process Troubleshooting
- Example: Troubleshooting a Seawater Pump
DAY TWO
- TapRooT®/Equifactor® Software Introduction
- Identifying Causal Factors
- Introduction to the Root Cause Tree®
- Exercise: Walking Through the Root Cause Tree®
- Exercise: Teams Find Root Causes Using the Root Cause Tree®
- Change Analysis
- Change Analysis Exercise
- Final Exercise: Solving a Major Equipment Issue
The course materials include the book Using Equifactor® Troubleshooting Tools and TapRooT® Root Cause Analysis to Improve Equipment Reliability, a TapRooT® Root Cause Tree®, the Root Cause Tree® Dictionary, and the Corrective Action Helper® Guide. Those books are a $129 value. The book includes a complete set of Heinz Bloch’s troubleshooting tables.
Upon completion of the course, attendees will receive a certificate of completion and a 90-day subscription to TapRooT® VI Software, our dynamic cloud-based software that computerizes the Equifactor® and TapRooT® Techniques.
We also have a 2-Day Virtual Equifactor®/TapRooT® Course that teaches the same material.
See the dates and locations of our upcoming public courses by CLICKING HERE.
Or CONTACT US to get a quote for a course at your site (or virtually).
