Fatal WV Explosion Investigation Report, CSB
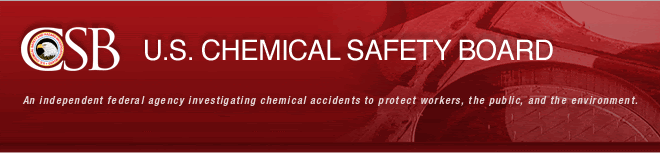
CSB (the Chemical Safety and Hazard Investigation Board) has released the investigation report covering the 2020 Optima Belle explosion and fatality that occurred in Belle, West Virginia.
The U.S. Chemical Safety and Hazard Investigation Board (CSB) released its final report into the December 8, 2020, fatal incident at Optima Belle LLC (Optima Bell) in Belle, WV. The incident occurred during Optima Belle’s production of a sanitizing compound for Clearon Corporation (Clearon). A dryer at the Optima Belle facility that was removing water from the compound exploded, resulting in the death of an employee and leading to significant property damage and a shelter-in-place order for the neighboring community.
The CSB’s final report makes fifteen recommendations to Optima Belle and Clearon, as well the U.S. Occupational Safety and Health Administration (OSHA), the U.S. Environmental Protection Agency (EPA), and other entities.
CSB calls on OSHA and EPA to close a glaring gap
In addition to recommending that the companies involved in this tragic incident correct deficiencies in their programs and operations, the CSB is once again calling on OSHA and EPA to close a glaring gap in their chemical regulations and provide much-needed additional coverage of reactive chemicals.
CSB Chairperson Steve Owens said, “Our report identifies a number of factors that led to this needless tragedy. In addition to issues with the production process, OSHA’s and EPA’s regulations do not adequately protect against hazards presented by reactive chemicals. Stronger regulations addressing reactive hazards will help keep similar incidents from occurring in the future, prevent deaths, and help protect workers at these facilities and the families who live nearby.”
Optima Belle offers toll manufacturing services – meaning that the company provides manufacturing equipment and services to other companies that provide raw materials or unfinished products. At the time of the incident, Optima Belle was working on behalf of Clearon through a contractual agreement with tolling broker Richman Chemical Inc. (RCI).
As part of the agreement, Optima Belle was dehydrating CDB-56® (sodium dichloroisocyanurate (NaDCC) dihydrate, an isocyanurate compound) to make anhydrous NaDCC. While dehydrating CBD-56® inside a pressure-rated rotary double cone dryer, the isocyanurate compound underwent a decomposition reaction, releasing gases that increased the dryer’s internal pressure to above its design pressure. At approximately 10:00 pm on December 8, 2020, the dryer exploded, releasing toxic chlorine gas.
Metal debris and dryer fragments propelled off-site and within the facility, striking a methanol pipe that then caught fire, leading to an estimated $33.1 million in property damage.
The CSB’s final report identifies the cause of the incident as being the over-pressurization of the facility’s dryer due to what is referred to as a runaway chemical reaction. The CSB identified that the facility did not adequately understand the potential for, analyze the hazards of, or detect and mitigate the self-accelerating reaction. Also contributing to the incident was the fact that the company for whom Optima Belle was producing the chemical – Clearon– did not transmit sufficient process safety information to Optima Belle, as well as both companies’ ineffective process safety management systems.
The CSB’s report identifies several key safety issues:
- Process Knowledge Management: Clearon lacked effective process knowledge management systems, and as a result, it did not deliver Optima Belle critical safety information as part of the tolling arrangement – Optima Belle was therefore unaware of the circumstances and temperatures that could lead to the hazardous decomposition of the compound they were working with.
- Thermal Hazards Assessment: None of the parties involved in the operation effectively assessed the hazards of the chemical being worked with and the circumstances that could possibly lead to a runaway chemical reaction.
- Equipment Selection and Design: Optima Belle did the work using equipment that was not designed or sized for the CDB-56® dehydration operation involved in the tolling agreement. It did not verify the adequacy of the dryer’s cooling or pressure relief systems during a decomposition reaction. Laboratory or pilot scale studies were also not conducted for the tolling operation.
- Tolling of Hazardous Materials: Companies often augment in-house production by outsourcing chemical processes and other operations. These agreements are called tolling contracts. Clearon established a tolling contract with RCI, who in turn contracted with Optima Belle. The Center for Chemical Process Safety (CCPS) provides industry guidance for safe and effective tolling arrangements. The dryer explosion might have been prevented had Clearon and Optima Belle applied the suggested industry guidance.
- Regulatory Coverage of Reactive Hazards: The facility was working with an isocyanurate compound that can undergo self-accelerating decomposition when heated. The reaction may lead to an explosion, fire, and toxic emission with severe impacts to people, property, and the environment. Yet, many such reactive chemicals are not regulated under OSHA’s Process Safety Management (PSM) standard or the EPA’s Risk Management Program (RMP) rule. Had NaDCC dihydrate been covered under the PSM standard or RMP rule, Optima Belle would have been required to implement risk mitigation and management systems that could have prevented this incident.
As a result of its findings, the CSB is issuing safety recommendations to OSHA, EPA, the companies involved in the incident, and safety organizations to prevent future chemical incidents and protect communities, workers, and the environment.
Investigator-in-Charge Vincent Vonzella said, “Our investigation found considerable safety management gaps at Optima Belle and Clearon. These gaps are not unique to this specific site. Across industry there needs to be a better understanding of the safety management system elements that must be in place to prevent incidents from reactive hazards.”
The CSB has a long history of investigating reactive chemical incidents, including producing a 2002 study in which the CSB called on OSHA and the EPA to expand their standards to address reactive chemicals and hazards. To date, however, neither agency has acted on the recommendations. The agency’s investigations involving serious reactive incidents include a 2020 incident in Westlake, LA; a 2019 incident in Waukegan, IL; the 2013 West Fertilizer incident in West, TX; a 2007 explosion and fire at T2 Laboratories in Jacksonville, Florida; and a 2004 toxic release at MFG Chemical in Dalton, Georgia, among other incidents.
The CSB is an independent federal agency charged with investigating incidents and hazards that result, or may result, in the catastrophic release of extremely hazardous substances. The agency’s core mission activities include conducting incident investigations; formulating preventive or mitigative recommendations based on investigation findings and advocating for their implementation; issuing reports containing the findings, conclusions, and recommendations arising from incident investigations; and conducting studies on chemical hazards.
The agency’s board members are appointed by the president subject to Senate confirmation. The Board does not issue citations or fines but makes safety recommendations to companies, industry organizations, labor groups, and regulatory agencies such as OSHA and EPA.
For more information about CSB, visit the website, www.csb.gov.
Circumstances can crop up anywhere at any time if proper and safe sequence and procedures are not planned and followed. We encourage you to learn and use the TapRooT® System to find and fix problems.
TapRooT® has a team of investigators and instructors with years of extensive training ready to offer assistance worldwide. We also offer ongoing support to our clients through free newsletters and root cause tip videos, the root cause analysis blog, and our annual Global TapRooT® Summit.
Register for one of our TapRooT® courses. We offer a basic 2-day course and an advanced 5-day course.
Contact us to discuss training your employees on-site. You may also call us at 865.539.2139 to speak to an instructor, schedule an executive briefing, or book on-site training for your team. We’re here to find solutions for you.