Where Does Advanced RCA Training Fit in an Executive’s Career?
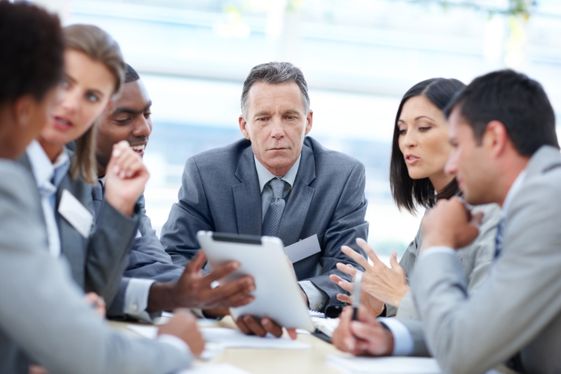
Why Should Executives Be Trained in Root Cause Analysis?
Executive root cause analysis was not my original idea. It came from the Chief Operating Officer of a large oil company and one of his senior staff.
It seems that the large oil company had several fatalities at its major construction projects at sites around the world. It wasn’t more than the industry average, but the company had made a commitment to have ZERO fatalities. What could they do?
The senior staff member had been trained in TapRooT® Root Cause Analysis and could see the value of having the senior executives of the construction projects know about the causes of accidents and how they could be prevented with advanced root cause analysis. He knew the leadership development program didn’t include this training as a standard part of the executive development progression. He mentioned this to the COO and the COO said:
“Let’s get them trained.”
So, a requirement was added to the executives’ bonus program. The executives had six months to arrange to attend the 5-Day TapRooT® Advanced Root Cause Analysis Team Leader Training to receive the “safety” portion of their executive bonus. (This was a considerable portion of their annual bonus program.)
Needless to say, the executives scheduled their week of training even though they had demanding schedules managing major projects.
We at System Improvements didn’t know about the COO’s requirement. We just saw senior executives start showing up for 5-Day Courses (the requirement for their bonus).
One of the executives at one course didn’t seem happy about being there. I talked to him during the break and asked him why he didn’t seem to want to be there. He explained that it was a requirement, and he didn’t see why he had to be there. After all, he didn’t have any fatalities on his project and was very busy. He didn’t see how taking five days for this training would be worthwhile.
I asked him to give the training a chance and then tell me his thoughts.
On Thursday of the course, he took me aside to apologize. He appreciated what he had learned and thought it would be valuable in his current position. But beyond that, he wished he knew what he had learned much earlier in his career.
This senior executive had made the case for TapRooT® Root Cause Analysis Training as part of their executive development program.
Part of Employee/ Executive Development
How would making advanced root cause analysis part of an employee/executive development program work?
Some executives think that Lean or Six Sigma training is sufficient as part of the executive development program. However, Lean and Six Sigma don’t include advanced root cause analysis training. They use Fishbone Diagrams or 5-Whys for root cause analysis, which isn’t advanced root cause analysis and doesn’t include the knowledge the senior executive thought was valuable.
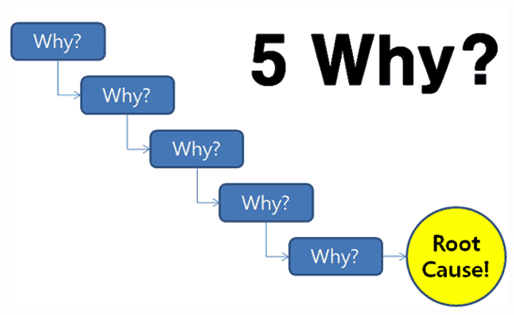
Would you like to know more about the differences between advanced root cause analysis and 5-Whys or Fishbone Diagrams? Then read these two articles:
Comparing 5-Whys with Advanced Root Cause Analysis
Fishbone Diagram Root Cause Analysis – Pros & Cons
Thus, most employee/executive development programs don’t include the knowledge of human factors and equipment reliability built into the TapRooT® Root Cause Analysis System, which the senior executive found valuable.
In fact, no other system has the knowledge and system design built into the TapRooT® RCA System. That’s why we protect our copyrights, patents, and trademarks.
If you want the valuable knowledge built into the TapRooT® System, you must schedule TapRooT® RCA Training and implement the patented TapRooT® RCA Software.
Why TapRooT® RCA?
Would you like to learn more about the knowledge and development that makes TaoRooT® Root Cause Analysis unique? What makes TapRooT® RCA superior? Read these articles:
How is TapRooT® Root Cause Analysis Different? (Best)
Where Did the Human Factors Knowledge
Embedded in the TapRooT® System Come From?
Root Cause Analysis Software History
For an example of using TapRooT® Root Cause Analysis to analyze an incident, see this white paper:
Using TapRooT® Root Cause Analysis
to Investigate Precursor Incidents
and Major Accidents
Build TapRooT® Into Your Company’s Culture
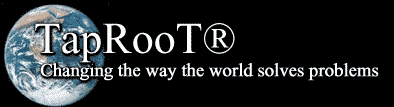
How should you integrate TapRooT® RCA into your company’s culture and make it part of employee/executive development? Below, I will outline how to get the process started and develop TapRooT® Root Cause Analysis into the fabric of your management and improvement processes.
First, you will want to test the system. Send some of your safety, environment, and quality people to one of our public TapRooT® Courses. I suggest the 5-Day TapRooT® Advanced Root Cause Analysis Team Leader Training Courses (the same course the senior executive attended).
Have them return to work and use what they learned. When you are pleasantly surprized with the root causes they discover and the corrective actions they develop, you are ready to take the next step.
The next step is to adopt TapRooT® RCA as the corporate standard for all root cause analysis. This includes root cause analysis of:
- Safety accidents and incidents (precursor incidents)
- Environmental incidents
- Quality issues/escapes
- Human Performance Incidents (HOP/Learning Teams)
- Maintenance problems and reliability issues
- Human resource incidents
This step includes licensing the TapRooT® Software and hosting it on your cloud or having us host it for you.
Now you are ready for initial training. This includes training for:
- Executives
- Team Leaders
- Junior Investigators
- General Employees
Let’s start with senior executive training.
Senior Executive Training
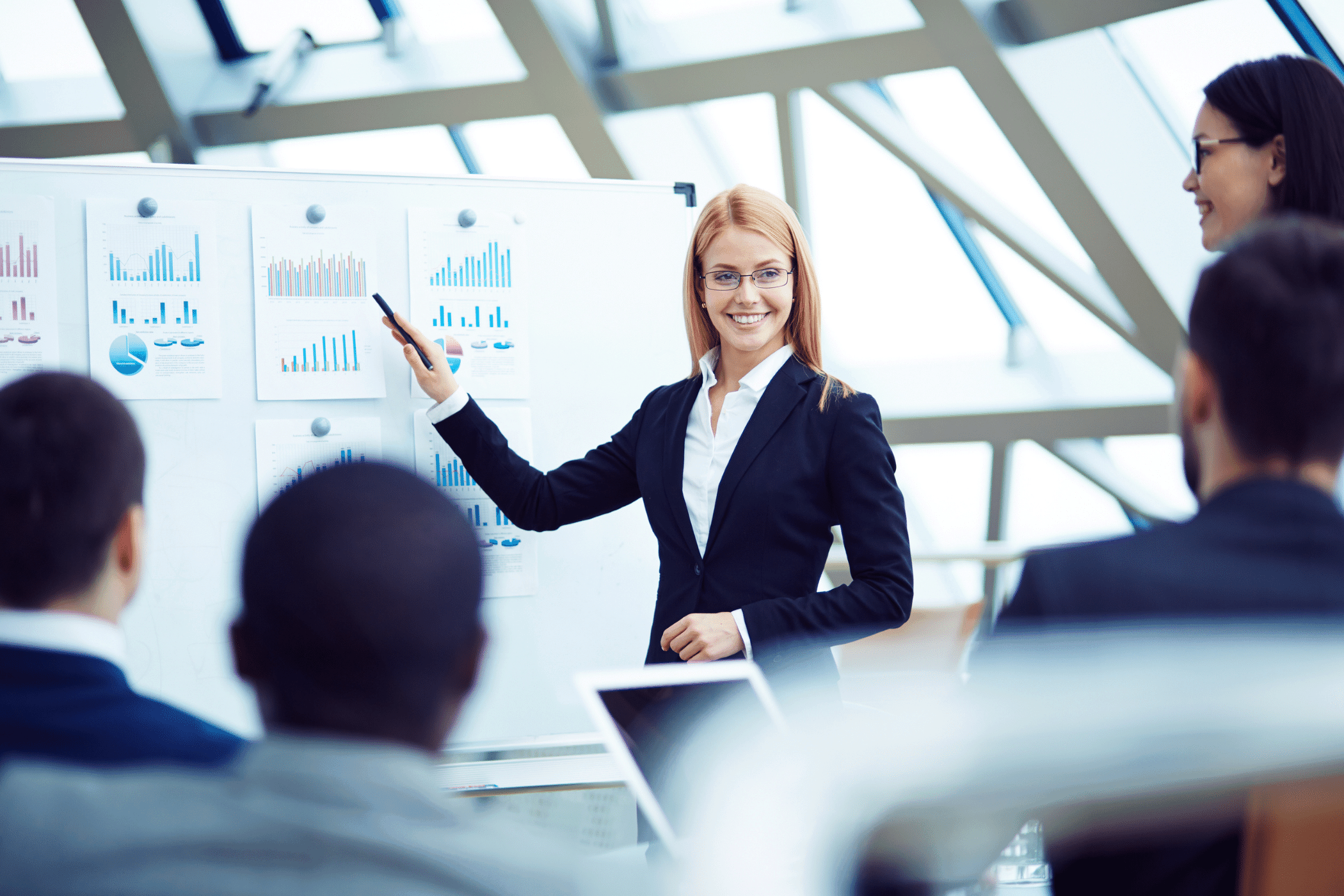
It would be great if senior executives had time for a 5-Day TapTooT® Advanced Root Cause Analysis Team Leader Course. However, most companies don’t have the COO making TapRooT® Training part of the senior executives’ bonuses.
So, how should you get things started? With the TapRooT® Executive Leaderships Role in Root Cause Analysis Course. This course can be customized to include as much information as the time allows. It won’t be the same as the 5-Day TapRooT® Course, but it is valuable for senior executives to understand how the TapRooT® RCA System works and what their role is in making TapRooT® Root Cause Analysis a success.
Team Leader Training
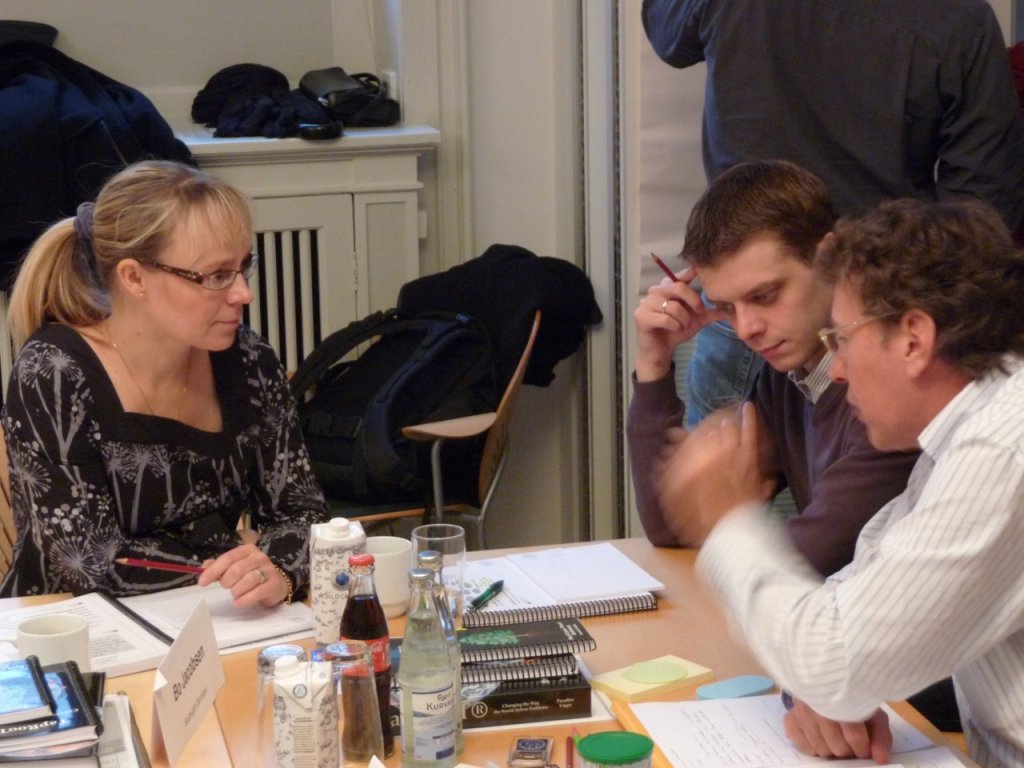
Team Leaders facilitate major investigations, coach Junior Investigators, and evaluate investigations completed by Junior Investigators. They are also in charge of safety, quality, environmental, HOP/Learning Teams, or equipment reliability programs and the director of Human Relations.
Team Leaders will attend the 5-Day TapRooT® Advanced Root Cause Analysis Training and should plan on attending advanced pre-Summit training and the Global TapRooT® Summit every 18 months as part of their professional development while they are one of the improvement program leader roles. The 5-Day Course will also become a part of the development path for the senior executive ranks.
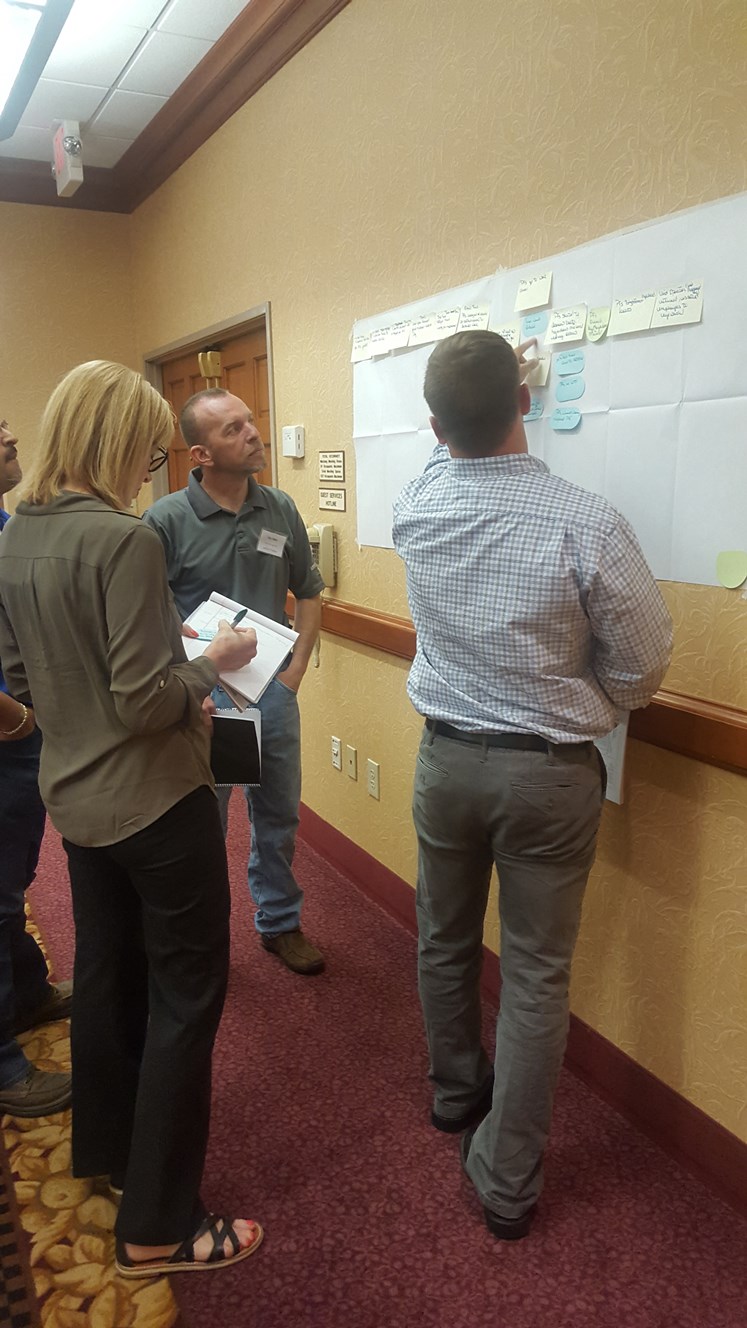
Junior Investigator Training
Junior investigators are usually assigned to investigate low-to-medium risk incidents (precursor incidents) and assist Team Leaders with more serious incidents.
They would be trained in either the 2-Day TapRooT® Root Cause Analysis Course where they would learn the essential TapRooT® Techniques or the 2-Day Equifactor® Equipment Troubleshooting and TapRooT® RCA Course that is designed for people investigating equipment problems.
They may move from this junior investigator role into a more senior position where they would then take the 5-Day TapRooT® Training.
General Employee Training
This is the most basic training that all employees who do not receive the training outlined above will receive. It is a 4-hour TapRooT® Course that outlines the TapRooT® Process and demonstrates that the TapRooT® System is not blame-oriented.
Start the Process – The Clock is Ticking
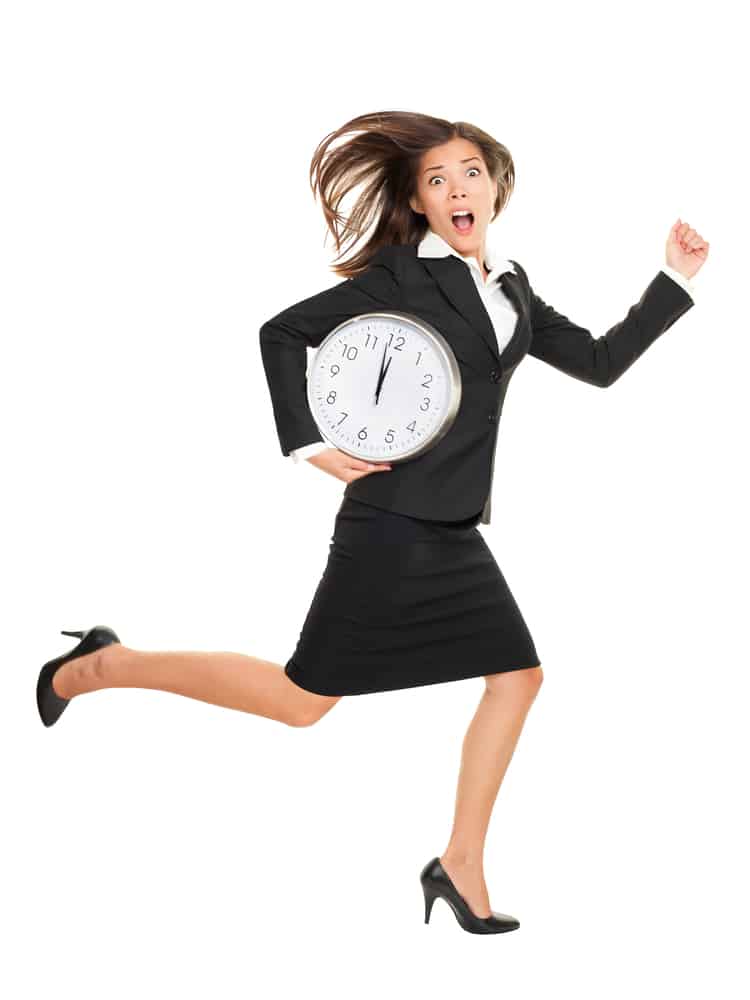
The clock is ticking. You don’t want a major accident, environmental release, quality issue, or unplanned equipment downtime.
Is it time to start bringing this valuable technology to your company? Technology that can help your company:
- Save lives
- Reduce risk
- Change behavior
- Stop human errors
- Improve production
- Prevent serious injuries
- Eliminate sentinel events
- Improve regulatory compliance
- Become a high-reliability company
- Improve environmental performance
- Improve Lean, Six Sigma, or CAPA Programs
- Enhance equipment/asset reliability and achieve excellence
CLICK HERE to see our upcoming public TapRooT® Training. To arrange on-site training, call us at 865-539-2139 or CLICK HERE to contact us via email.