When to Use Root Cause Analysis
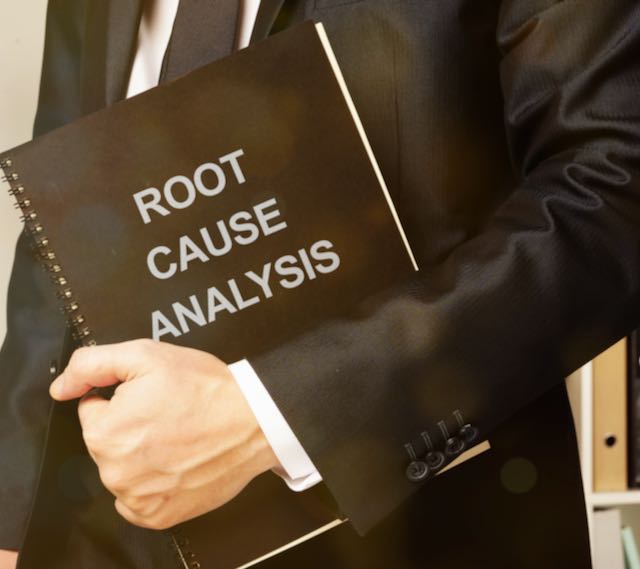
Bad Advice
I heard a safety guru say that EVERY loss deserves an investigation and corrective action.
Is that possible?
Is that desirable?
I would say NO.
Not every loss needs an investigation and certainly not every loss deserves a root cause analysis. So, when should you use root cause analysis?
When Should You Use Root Cause Analysis?
Because every investigation should have at least a chance of a positive return on the investigation investment. Many losses are too small to get much benefit from an investigation. (This is true even if you take into account the potential for even bigger problems down the road.) Let’s face it, sometimes there just isn’t much to learn from a paper cut!
Why should we avoid wasting our improvement energy on unimportant minor problems?
Because every organization has resource limitations and we should spend our resources wisely. We need to put our effort where it will do the most good.
Therefore, we must target our resources where they will get the most improvement bang for the buck.

The targeting of improvement resources should match management’s goals. This targeting of resources should guide the improvement effort by assigning resources for safety, quality, reliability, productivity, and product improvement. Of course, the division of resources is guided by the company’s risk assessment and market analysis.
Let’s Look at an Interesting Hypothetical Example.
At a large chemical company, a budget and level of emphasis has been assigned for safety improvement. How should the company spend this budget? Where should the safety team direct their resources?
The first place to look would be the company’s real accident data. Of course, if the company has poor root cause analysis, the data will not be meaningful. If that is true, the first place to apply resources is to achieving outstanding root cause analysis of significant accidents.
What if this company has been applying advanced root cause analysis for several years and has fairly good accident data. Then, they can use that data to determine where their biggest risks are and what type of root causes contribute the most to that risk. That knowledge can help them target their resources.
If a company’s safety improvement programs are fairly ineffective (measured by the fatality count), the majority of the emphasis should be put on the investigation of significant incidents and precursors to significant incidents. These are incidents that cause fatalities and serious injuries and incidents that could have caused a fatality or serious injury if one or two more Safeguards had failed.
The remaining improvement effort (say 33%) would be applied to proactive improvement. This includes local safety audits, peer observations, management field observations, and outside audits.
As the company improves, their safety performance and the time between significant incidents will improve significantly (Do you trend this?). As this happens, effort is shifted from reactive investigations (because there are less of them) to targeted proactive improvement. This tends to cause an excelleration in the improvement progress.
What Happens If Your Company Doesn’t Have Good Root Cause Analysis?
If a company does NOT do a good job investigating and fixing their serious incidents, the proactive improvement efforts tend to be miss-directed. The lessons learned from significant injuries and potential significant injuries are inaccurate. The data produced misdirects the proactive improvement efforts. The significant injuries continue even though the minor incidents targeted by the misdirected proactive improvement efforts tend to improve.
This misdirection of proactive improvement efforts has been written about extensively. Proactive behavior based safety improvement efforts produced good trends in lost time injury data with little improvement in fatality and significant injury data as shown from a 2015 article in Professional Safety titled Preventing Serious Injuries & Fatalities…

This should not be a surprise. It is the reason that many companies hit a plateau of improvement for major accidents while having world-class lost time injury rates.
I believe an excellent example of this misdirection of improvement efforts could be seen in the BP Texas City Refinery explosion. Management thought their improvement efforts were working because of a decrease in the LTI rate but the fatality rate (that included contractors) was unchanged (or maybe slightly worse).
Where Is Your Company/Site in Their Improvement Efforts?
Is your company/site trending the time between serious injuries and fatalities?
Is that time increasing significantly?
Do you know how to tell if the time between incidents increases significantly?
We can help you learn how to mathematically prove that improvement is occurring (or that things have taken a turn for the worse).
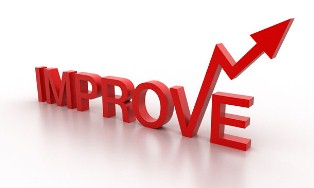
Is your company’s LTI rate improving without making much impact on your significant injury rate? This is a sign of a misdirected improvement effort and a need to improve your root cause analysis.
We can review your program, point out potential improvements, and teach your folks how to apply the best root cause analysis techniques reactively and proactively to make improvement happen.
We can also help your management understand their impact on improvement. How they directly influence the quality of the root cause analysis. (You can’t have excellent root cause analysis without management understanding and involvement.) Even the best root cause analysis systems can’t succeed unless management asks for the appropriate investigations and provides the resources needed to implement effective performance improvement fixes.
Once this is on track, we can help you see how to effectively apply your resources to get the most bang for your improvement buck. This includes targeting improvement efforts and deciding when a root cause analysis is needed and when the effort should be applied elsewhere.
Call us at 865-539-2139 (or CLICK HERE to contact us) to discuss your improvement efforts and see how we could help focus your program to get the best return on your improvement investment.
Courses That Can Help

Learn techniques that will help you improve performance in these courses…
5-Day TapRooT® Advanced Root Cause Analysis Team Leader Training
This is the course we recommend for people who facilitate investigations – especially investigations of serious injuries, fatalities, and precursor incidents.
Find out more about the course and see the complete course outline HERE.
See the upcoming public course dates and locations HERE.
2-Day Auditing & Proactive Improvement Using TapRooT® RCA Course
Learn to use TapRooT® Root Cause Analysis as part of an effective proactive improvement program. See the course details HERE.
See the public course dates and locations HERE.
2-Day Measurement, Trending, and Proactive Analytics: How the Best Use Data Every Day to Improve Work
Kevin McManus will teach you advanced trending techniques to help you measure and improve performance. See the course details HERE.
See the public course dates and locations HERE.
The 2024 Global TapRooT® Summit
A great way to network, benchmark, and learn the latest improvement program best practices is to attend the 2024 Global TapRooT® Summit.
The Better Improvement Programs and CAPA Track includes a session on using trending to manage improvement. Plus the pre-Summit courses include the Measurement, Trending, & Predictive Analysis Course being taught by Kevin McManus. The course and session can help you improve your use of root cause data and management of your improvement programs.
But there’s more…
Pre-Summit Courses
The Summit starts with 11 advanced courses on April 29-20. These courses include:
- 2-Day TapRooT® Root Cause Analysis Training
- Effective Communication Certification
- Stopping Human Error
- TapRooT® Advanced Case Study Workshop
- Developing an Incident Command System – A New Value Proposition Using TapRooT® Tools
- Measurement, Trending, & Predictive Analysis
- Equifactor® Equipment Troubleshooting & TapRooT® Root Cause Analysis Training
- Effective Interviewing & Evidence Collection
- Risk Assessment and Risk Management Best Practices
- Auditing & Proactive Improvement Using TapRooT® Root Cause Analysis
- TapRooT® Software
Best Practice Tracks
Next comes the three-day Summit. The Summit includes Best Practice Tracks organized by these Track Leaders…
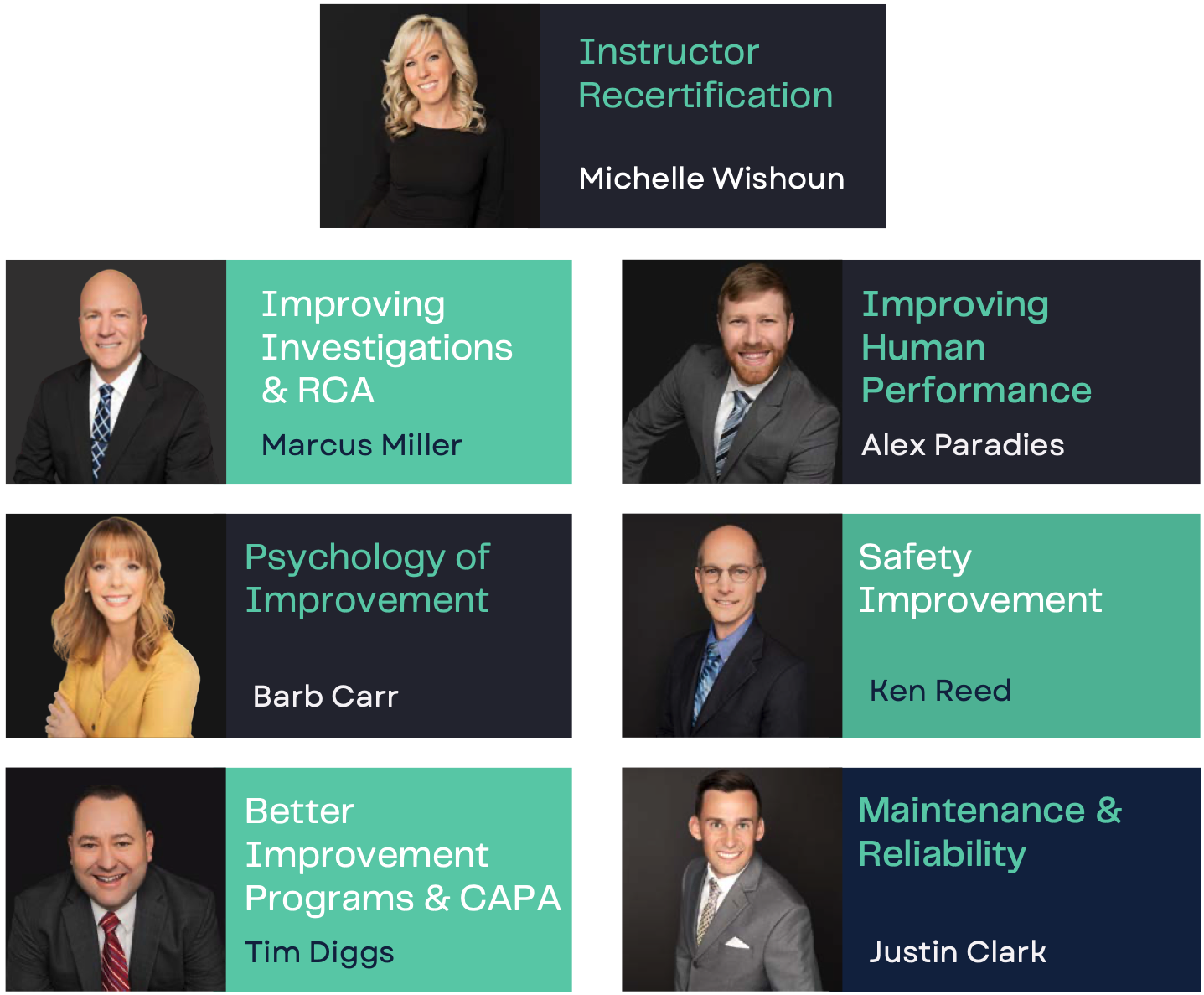
Click on the track titles below for details about each track:
- Improving Investigations & RCA
- Improving Human Performance
- Psychology of Improvement
- Safety Improvement
- Better Improvement Programs and CAPA
- Maintenance and Reliability
- Instructor Recertification
Keynote Speakers
Also, the Summit includes five interesting, inspiring, informative Keynote Talks…
Erika Armstrong (Wednesday AM)

Betsy Allen-Manning (Wednesday PM)

Mark Paradies, Amy Souders, & Alex Paradies (Thursday AM)

Dan Verlinde (Thursday PM)

Karl Mecklenburg (Friday AM)

Summit Guarantee
We know that TapRooT® Users will enjoy the Summit and learn valuable new skills and ideas that they will take back to work and apply. That’s why we can offer this exceptional GUARANTEE:
Attend the Global TapRooT® Summit. Go back to work and implement your roadmap to success. If you don’t save 10 times the cost of the Summit fee, let us know and return your Summit materials, and we will refund 100% of the Summit registration fee.
This guarantee shows how certain we are that you will learn valuable best practices to take your team’s and your organization’s performance to the next level.
Plus, this guarantee also applies to people who have not implemented TapRooT® RCA yet. So, if you are a TapRooT® User or just someone interested in improving performance, you should REGISTER for the 2024 Global TapRooT® Summit NOW!
What Past Participants Have to Say
Here are some samples of what people said about past Summits to help you judge whether your investment will be worthwhile…
Pat, Suncor: “Fantastic speakers and sessions. I’m taking a lot of tools back to improve performance.”
Rich, PPL Electric Utilities: “Well organized. This was my first Summit, and from the start to the end was a great experience and great networking.”
Teresa, Irving Oil: “The Summit was fun! There were wonderful speakers. I have a lot of good information to take back to my workplace.”
Jeff, Halliburton: “It’s like a family reunion, except you meet root cause experts from around the world.”
Dave, Marathon: “Very Valuable. Well-organized multiple breakout sessions with good practices and even some things not to do.”
Jeff, First Energy: “This is my second Summit in a row, and each time I come, I learn new, valuable things to take back to work and apply,”
And that’s just a sample of the very positive feedback we get about past Summits. And here’s another thing to consider … We make the Summit better every year.
Bring a Team

And if you want to get the most from that Global TapRooT® Summit, bring a team of managers, investigators, and people interested in performance improvement to turbocharge your improvement program. See the savings possible with the discounts for bringing a team shown below.

Don’t miss this opportunity to learn ways to improve performance at your company.
Summit Dates and Location
When and where is the 2024 Global TapRooT® Summit being held?
The Summit is scheduled for April 29 – May 3.
Where is the Summit being held?
At the Horseshoe Bay Resort near Austin, Texas.
To download the Summit Brochure, CLICK HERE.
CLICK HERE to register.
Summit Location Information
The Horseshoe Bay Resort is a great place to hold the Summit. See more information about the location in this video…