You Don’t Need a Root Cause Test
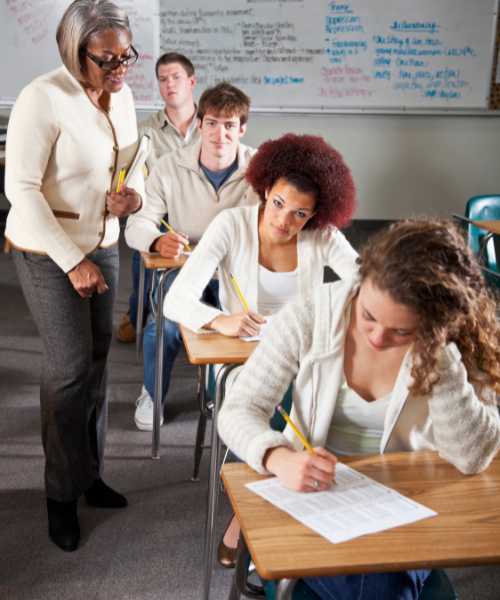
Is a Test Required to Use TapRooT® RCA?
A potential TapRooT® Root Cause Analysis client asked me:
“What test do you use to ensure you find a true root cause?”
The potential client was using a “Why-Why” Analysis and they thought that any root cause technique needed a test to see it had reached a “root cause.”
Unfortunately, using one of the “why” methods (“Why-Why,” 5-Why’s, etc.) leads many investigators to question their method. After using it a few times, it becomes obvious that “Why?” methods depend on the investigator’s experience and biases.
For example, if you’re a training person, you seem to find training problems. If you are familiar with writing good procedures, you find procedure problems. Everyone finds “human errors” and can tell people to be more careful.
These “why” methods don’t provide expert guidance to get beyond the investigator’s current level of knowledge. For example, if you don’t know anything about “human engineering,” you will never look for human engineering problems. You will only find problems you already understand. You have to understand the cause-and-effect relationship to find a true root cause. This is why, when using a “why” method, you will only implement corrective actions that you have tried in the past.
This lack of understanding of a wide variety of cause-and-effect relationships is the need for a root cause “test” to see if you have found a root cause. However, only a highly-trained human performance expert can answer, “How far beyond a human error is the root cause?”
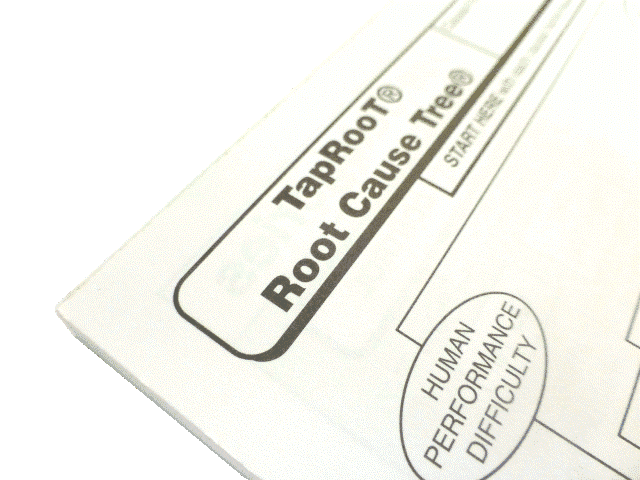
So, what did I tell the potential client? You don’t need a test because TapRooT® Root Cause Analysis has built-in human performance knowledge in the Root Cause Tree® Diagram and the Root Cause Tree® Dictionary. TapRooT® Root Cause Analysis has expert systems to guide the investigator to the root causes of an incident. These are built into the Root Cause Tree® Module of the TapRooT® Software.
Good News
It’s good news that TapRooT® RCA is designed to give you the expert guidance needed to find root causes when using the system without relying on a test.
TapRooT® RCA was designed by human performance experts to guide investigators to true root causes of human errors. How? By using a series of simple “yes/no” questions that guide the investigation. The answers to those questions quickly narrow down the investigation to the true root causes of human performance or equipment failures. Once you have these root causes, you can use the Corrective Action Helper® Guide (or the Corrective Action Helper® Module of the TapRooT® Software) to develop effective corrective actions.

Instead of ending up with corrective actions like “Counseled the operator to be more careful,” you can find the root cause of the error and develop an effective corrective action to prevent, (or at least reduce the likelihood of) making the same type of error in the future. You can make the work easy to do right and hard to do wrong.
So, in conclusion, there is no reliable test that checks to see if you have reached true root causes using one of the “why” methods IF you don’t already understand the cause of the problem. A test can’t make you find a cause in the cause-and-effect chain if you don’t know that the cause produces that effect. Guessing at causes can’t be tested.
Learn to Find the True Root Causes
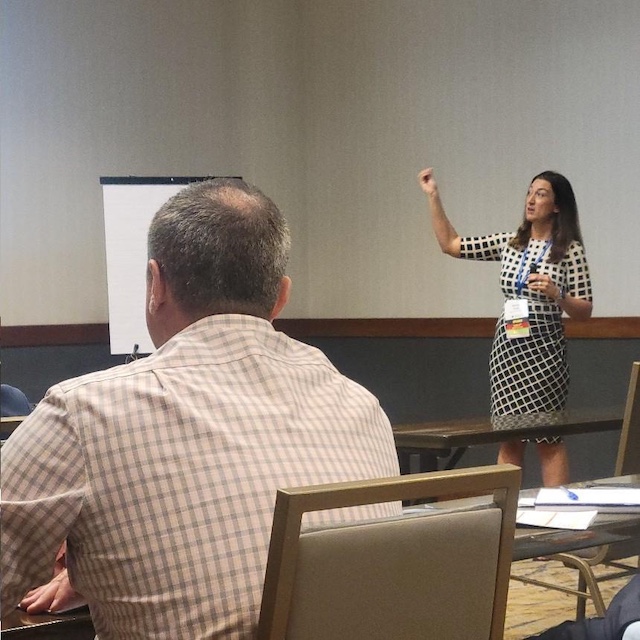
You can learn to use the TapRooT® System in one of our public
courses. Learn more about the training HERE.
To see the dates and locations of our public training, CLICK HERE.
And to contact us to schedule a course at your facility, CLICK HERE.
Don’t wait! You don’t want to fail a test and have poor root cause analysis allow an accident that should have been prevented. Learn TapRooT® RCA as soon as possible and get started creating more effective corrective actions.