Get Real, Get Better
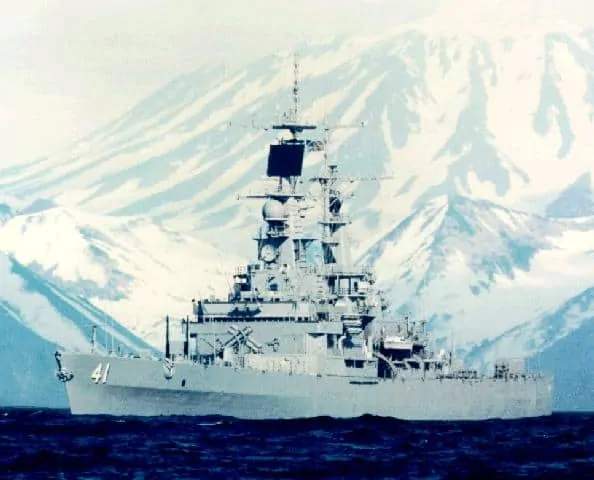
US Navy Improvement Program
In 2022, the US Navy started the “Get Real, Get Better” Program to improve fleet performance after a series of collisions and groundings in the 7th Fleet. The program is outlined below…
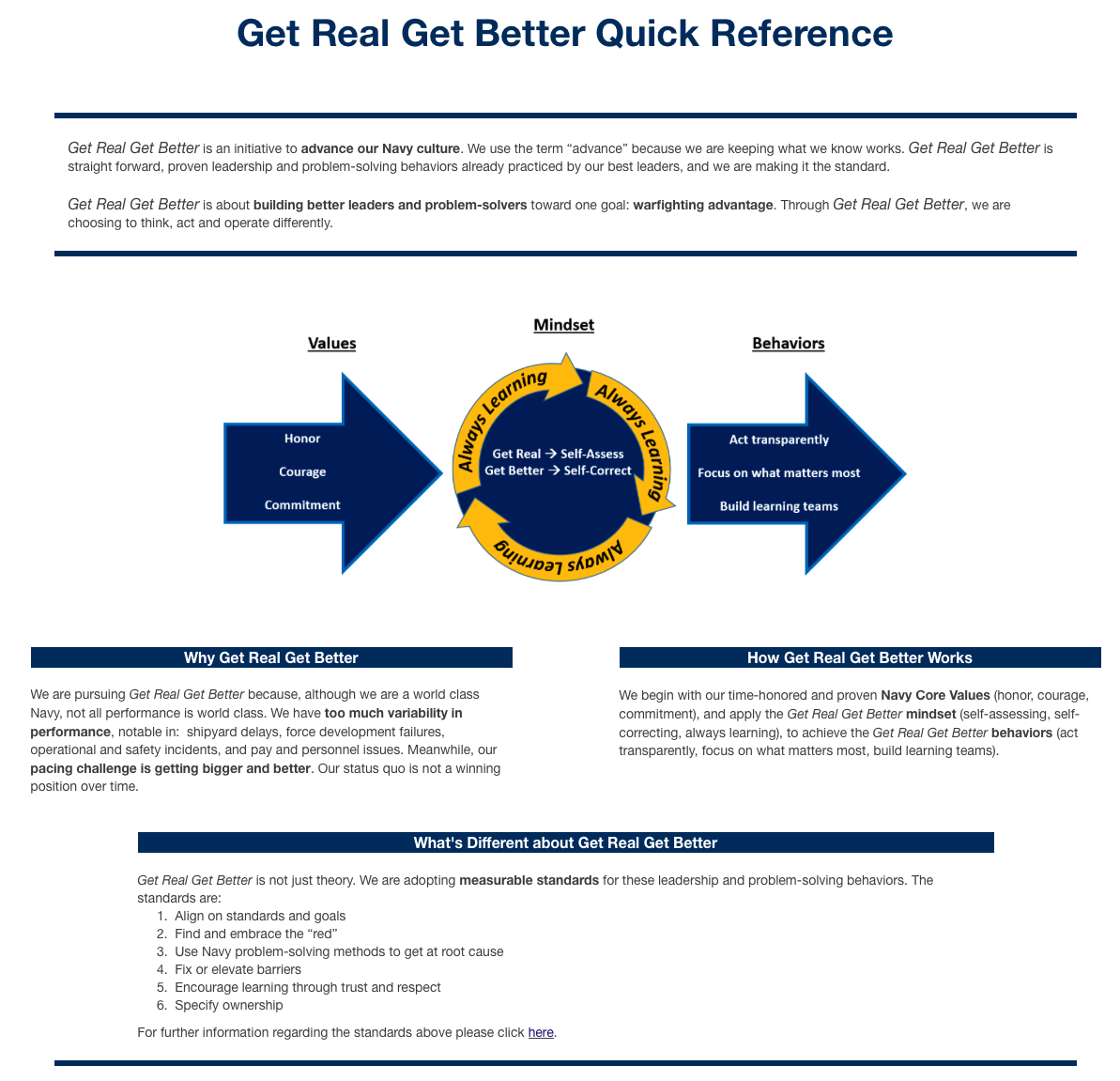
The top brass says…
The Navy says the “Get Real, Get Better” Program has two elements:
Get Real
“Get Real is about having the courage to self-assess, to build teams that embrace honest, hard, transparent looks at our performance, and to understand our actual strengths and shortcomings. We must be our own toughest critics.”
Get Better
“Get Better is about a commitment to improve, to be self-correcting. It’s about taking pride in high standards and fixing problems together when they are small, before they grow large and complex. It’s about applying proven methods to get after the things that matter most, in a focused and disciplined way, and not by just adding activity.”
Problems
In a 2024 San Diego Naval Base assessment of Get Real, Get Better, just 1 in 4 sailors have bought into the Get Real, Get Better Program. The other 75% either hadn’t heard of the program or said something to the effect that:
“…I’ve heard of it, but I’m not a believer…”
Why would that be? Here are some ideas…
Bad Tools
What are they using for root cause analysis? 5-Whys.
Here is what one officer had to say…
Of course, the 5-Why Technique is utterly inadequate for almost all problems. For ideas on why the 5-Whys are inadequate, see these articles:
- Problems Using 5-Whys? Read “Under Scrutiny” from Quality Progress to Understand Why!
- 5-Whys Example – Is this Root Cause Analysis? (Updated)
- Comparing 5-Whys with Advanced Root Cause Analysis
The Navy also applies DMAIC (similar to Causal Learning) and Fishbone Diagrams.
However, the root cause tools are only part of the problem.
Not Fixing the Real Generic (Fleet-Wide) Problems
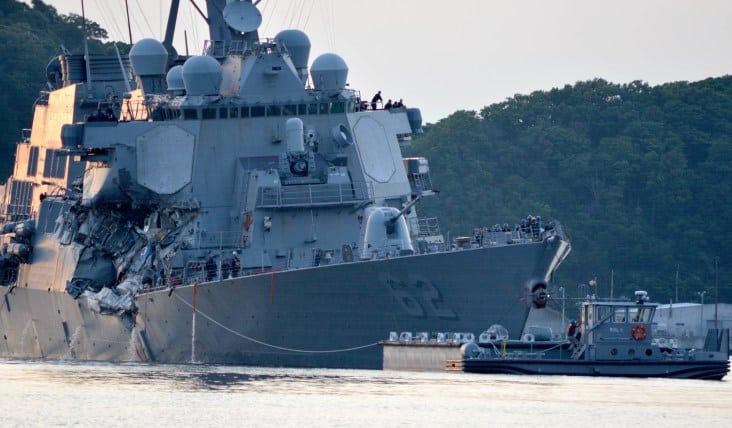
Looking back at the two collisions in the 7th Fleet, several issues were identified that would not be easy for sailors to analyze or correct. For example:
- The human factors of the steering systems (see this LINK).
- The staffing of ships (see this LINK).
- The training program for junior officers (see this LINK).
- The operations tempo in the 7th Fleet (too few ships and too many missions – see this LINK).
- Fatigue (see this LINK).
- A culture of “Blame and Shame” (see this LINK and this LINK).
Then, there is THIS ARTICLE about the conditions aboard the USS Fitzgerald.
I recently watched a video where an Admiral said the Navy needed 70 operational ships to support its mission. He then said we may not have 70 fully operational ships right now. SEVENTY! That seems completely inadequate to support operations in the Atlantic, Pacific, Mediterranean, and Persian Gulf/Arabian Sea/Indian Ocean.
The chance that sailors could suggest effective solutions for the problems listed above using 5-Whys is laughable. The most likely corrective actions would be band-aids and training.
Could they pass the “barriers” they couldn’t fix to higher levels to find root causes and fix the problems? That’s doubtful since the higher levels created the problems or have lived with them so long that they see them as normal.
What Should the Navy Be Doing?
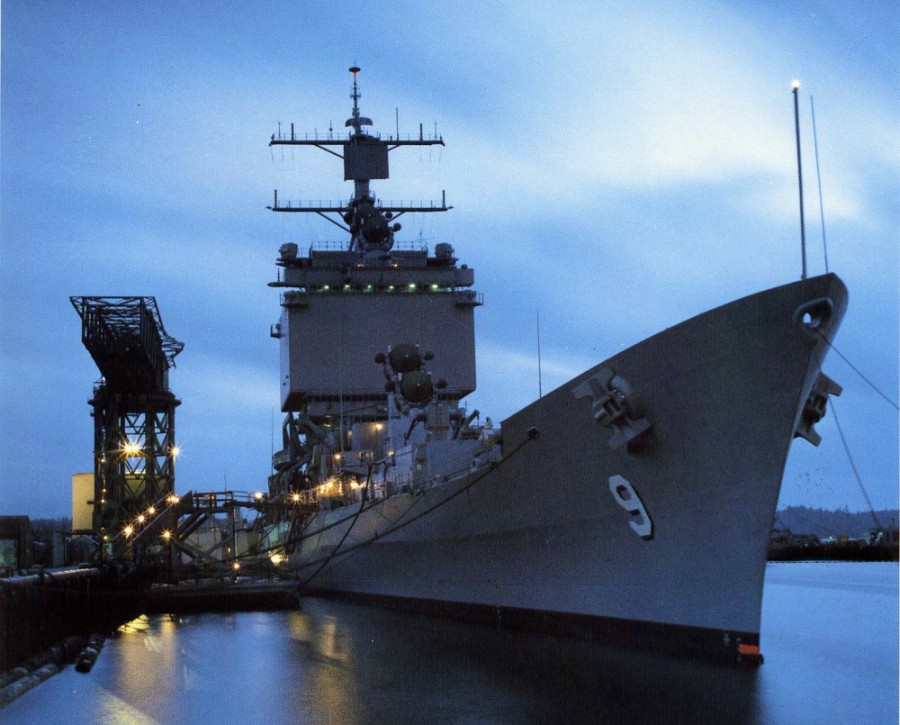
It’s been a long time since I served in the Navy. During the Cold War, I was an officer aboard the USS Arkansas (CGN-41) and the USS Long Beach (CGN-9).
Let’s “Get Real.” During the Cold War, the Navy faced the same challenges as the current Navy. The pace of change was dramatic. Budgets were tight. The USSR was a near-peer competitor. We had a difficult operating tempo. Pay for sailors was far below civilian salaries. After the Vietnam War, with the start of the all-volunteer fleet, morale was probably lower, and recruiting was more difficult than it is today.
There were a couple of other differences. Today’s Navy isn’t trying to grow to a 500-ship fleet; the new Navy is much smaller. The new Navy also decided to save money by reducing the manpower on each ship. Technology and shore support would replace manpower, but this led to much less self-sustaining ships.
Today, I hear lots of talk about:
- Self-Assessment
- Learning
- Embrace the Red
- Transparency
- World-Class Performance Techniques Molded into Navy Requirements
- Root Cause Analysis
- Single Accountable Leader
- Best Practices
- Drive and Measure Outcomes
- High Standards at the Deckplates
However, the “Navy-Proven” problem-solving critiqued above and applied in the “Get Real, Get Better” Program won’t solve the Navy’s problems. Continued accidents prove that point. Headlines from the Military Times document the facts.
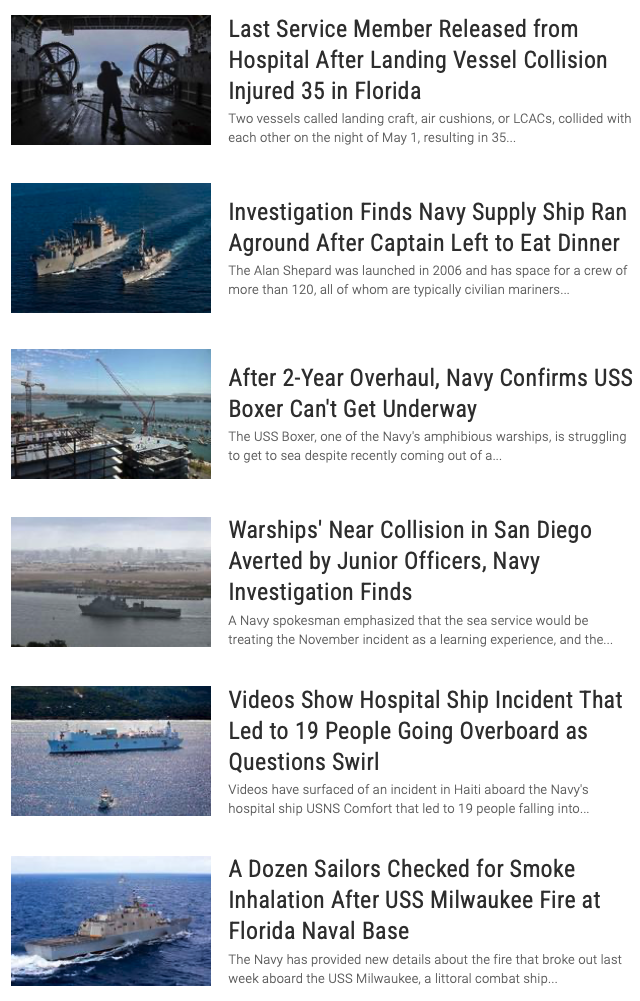
I’ve spent 30+ years observing world-class performance at industry-leading companies worldwide. We have helped these leaders improve (see success stories HERE) using world-class root cause analysis tools.
However, the Navy’s root cause analysis and performance improvement tools are not world-class. High standards don’t start at the deck plates (see how Admiral Rickover achieved excellence in THIS SERIES OF ARTICLES and by reading the book below).
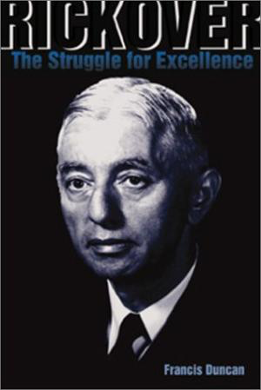
Where can the Navy learn something better? Suppose the Navy is interested in world-class performance and sharing best practices with leading organizations. In that case, it should send someone to the Global TapRooT® Summit to learn practical, world-class ways to achieve excellence. Since that Summit is a year away, the Navy might consider having key personnel attend a five-day course to understand the fundamentals of root cause analysis.
I’m not suggesting this because we sponsor the courses and the Summit. I’m saying this because I’ve seen the same problems and the same type of solutions applied by the Navy since the 1990s without significant improvement. And what is the definition of insanity?
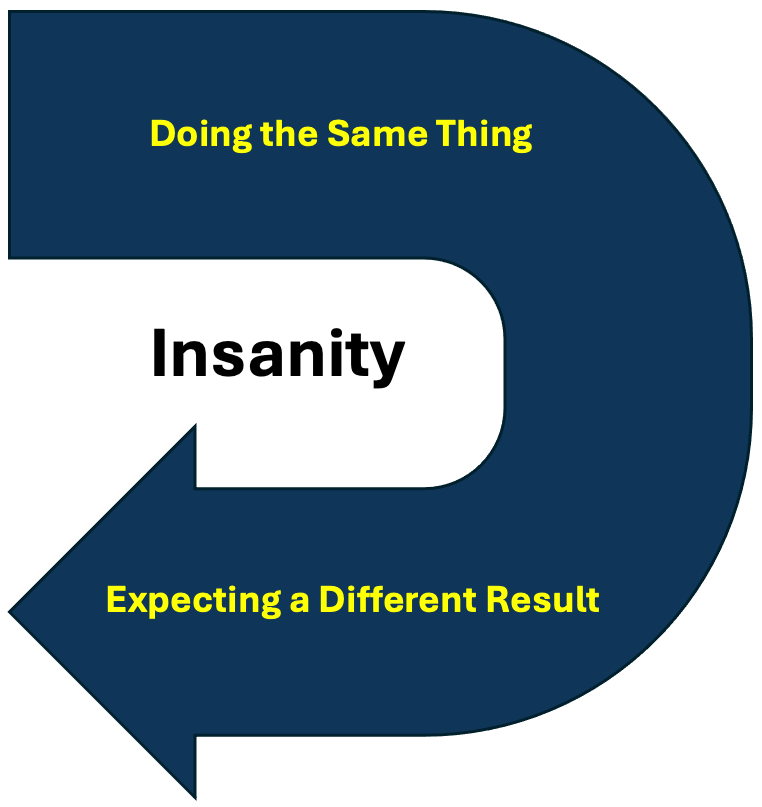
Unfortunately, until the Navy adopts world-class root cause analysis, it won’t be able to accelerate learning to improve its warfighting advantage at sea. Instead, the Navy will continue developing new programs with new names and wonder why expected improvements never materialize in the long term.