Fight Fear with Root Cause Analysis
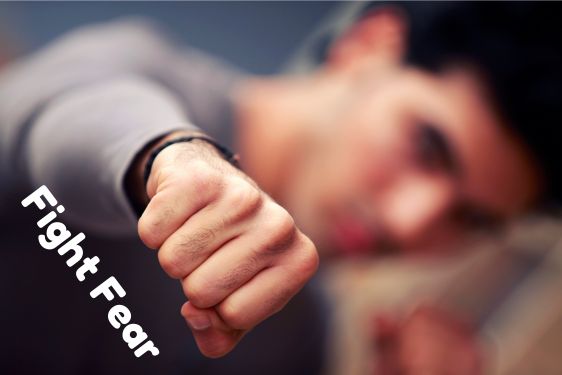
#1 Investigation Problem – Fear!
In the late 1990s, the Center for Chemical Process Safety polled its members about their problems investigating incidents. What was the #1 problem? Fear! People were afraid after an incident, inhibiting the free flow of information about what had happened.
Henry Ford also saw fear as a problem. He said:
“One who fears limits his activities.
Failure is only the opportunity to more intelligently begin again.”
So, have things changed since 1928 or even 1999? Is fear still a problem in 2025 for your incident investigators? If so, read on to learn the causes of fear and ways to fight fear by applying well-known root cause analysis tools.
What Causes Fear?
To stop fear, you must understand its causes. What causes fear after an accident when the investigation starts?
- Fear of punishment (especially being fired).
- Fear of being wrong and looking stupid.
- Fear of the stigma of being “at fault.”
- Fear of being seen as a problem employee and getting bad evaluations.
- Fear of being blamed for injuries or fatalities.
- Fear of the investigators (especially if they are senior management or law enforcement).
These six are just the start of the blame and fear negative cycle.
The “Blame” Vision
Fear is often caused by managers and prosecutors trapped in the Blame Vision.
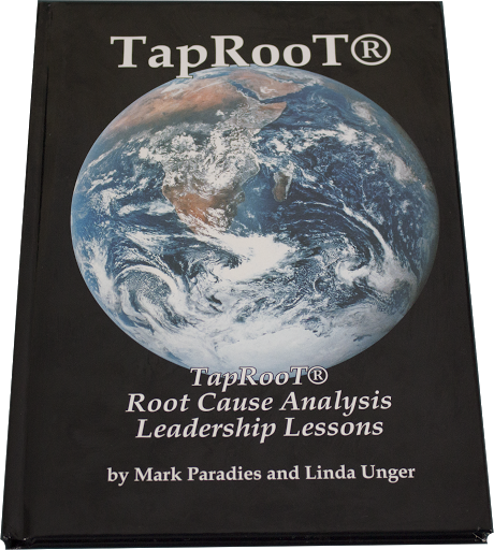
In Book 1: TapRooT® Root Cause Analysis Leadership Lessons, section 1.2 discusses the “Blame Vision.” Here is a quote from that section:
We’ve seen managers caught up in the Blame Vision. They believe: “If we could just get people to be careful and try harder, these problems would go away.” These managers think they can weed out the bad, lazy, or careless employees or discipline them to get them to work harder and smarter. These managers see problems as obviously the fault of the person doing the work. If the worker was more careful, then he/she would have opened the correct valve. If the surgery team had been more careful, they would have amputated the correct leg.
The only problem for people with the “Blame Vision” is finding the right person to blame. Once that person is identified, he or she can be disciplined (fired?), and then we can return to business as usual.
What? You don’t think the Blame Vision exists in our modern age? I’ve seen it too many times to doubt its existence. Especially when major accidents occur. For example:
- BP Texas City explosion and fire and the Bonse Report,
- USS Fitzgerald collision at sea and Blame Game Serious Bussiness,
- Statistics show that 90% of our accidents are caused by 5% of the workforce,
- USS Hartford/USS New Orleans collision,
- Fire at Arkema plant,
- US Army friendly fire incident,
- Vanderbilt patient fatality,
- USS John S. McCain collision at sea,
- Scaffold collapse in Toronto,
- USS Ford initial operational problems,
- Fatality at UK hospital and wrongful criminal prosecution,
- Transocean’s role in the Deepwater Horizon blowout, explosion, and fire,
- Miami bridge collapse,
- Marine Corps mortar accident, and
- Moscow subway accident.
And that’s just a partial list. Here is Marcus Miller talking about blame, discipline, and criminalization of accidents at the 2020 Global TapRooT® Summit (apologies for the poor audio at the start of the video; it gets better as the video progresses)…
Perhaps people trapped in the Blame Vision need to use this root cause analysis tool…

That kind of blame-oriented philosophy leads to fear and non-cooperative employees when an incident occurs.
At this point, a quote from Albert Einstein might apply…
“Condemnation without investigation is the height of ignorance.”
Investigators Need Cooperation
To investigate an incident, investigators need the cooperation of those involved. They need to find out:
- What people involved did and what they observed.
- What those nearby saw, felt, heard, tasted, and smelled.
- Any mistakes that people made or observed.
In other words, investigators need to find out what happened.
What do many employees do when faced with blame, being fired, and even criminal prosecution? They may tell a good story to CTA (cover their a**). I’ve even seen team members collaborate to make up a story that deflects blame. And I’ve seen investigators blame equipment failures to save people from discipline.
False stories create needless work for investigators to try to find out what really happened and ineffective corrective actions for fake root causes.
I’m always amazed when people cooperate despite the Blame Vision at their plant. It encourages me about what we can accomplish if we stop blame, needless punishment, and fear.
So, what should we do to help stop fear? Read on for three ideas.
Idea 1: Stop Punishment
Henry Wadsworth Longfellow said…
“Look upon errors of others in sorrow, not anger.”
Stopping the knee-jerk reaction of punishing people immediately after an accident may sound like heresy, but I believe it is the first step in learning and preventing future accidents.
Senior management must declare that there will be no punishment for accidents. The only punishment will be for willful criminal acts.
Is that statement too bold a move? Well, what about no punishment unless a person intentionally violates a well-understood, consistently applied rule that is consistently and positively enforced and followed by an overwhelming majority of the other employees?
One of the steps mentioned above is absolutely imperative if you want employees to overcome fear and honestly cooperate with an investigation.
Idea 2: Use a SnapCharT® Diagram
Once the fear of punishment is removed, the next step is to relieve the employee’s fear of looking stupid and fear of the investigative team.
Good news! This step is pretty easy.
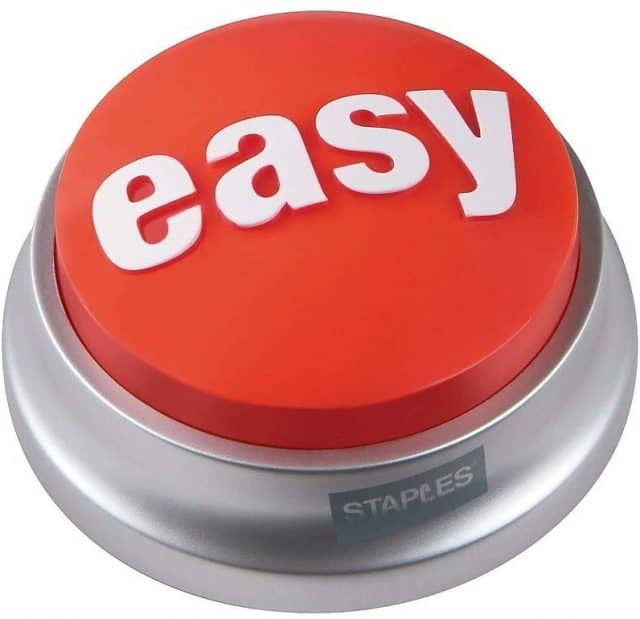
How do you do it? Adopt the SnapCharT® Diagram as a standard part of your investigation.
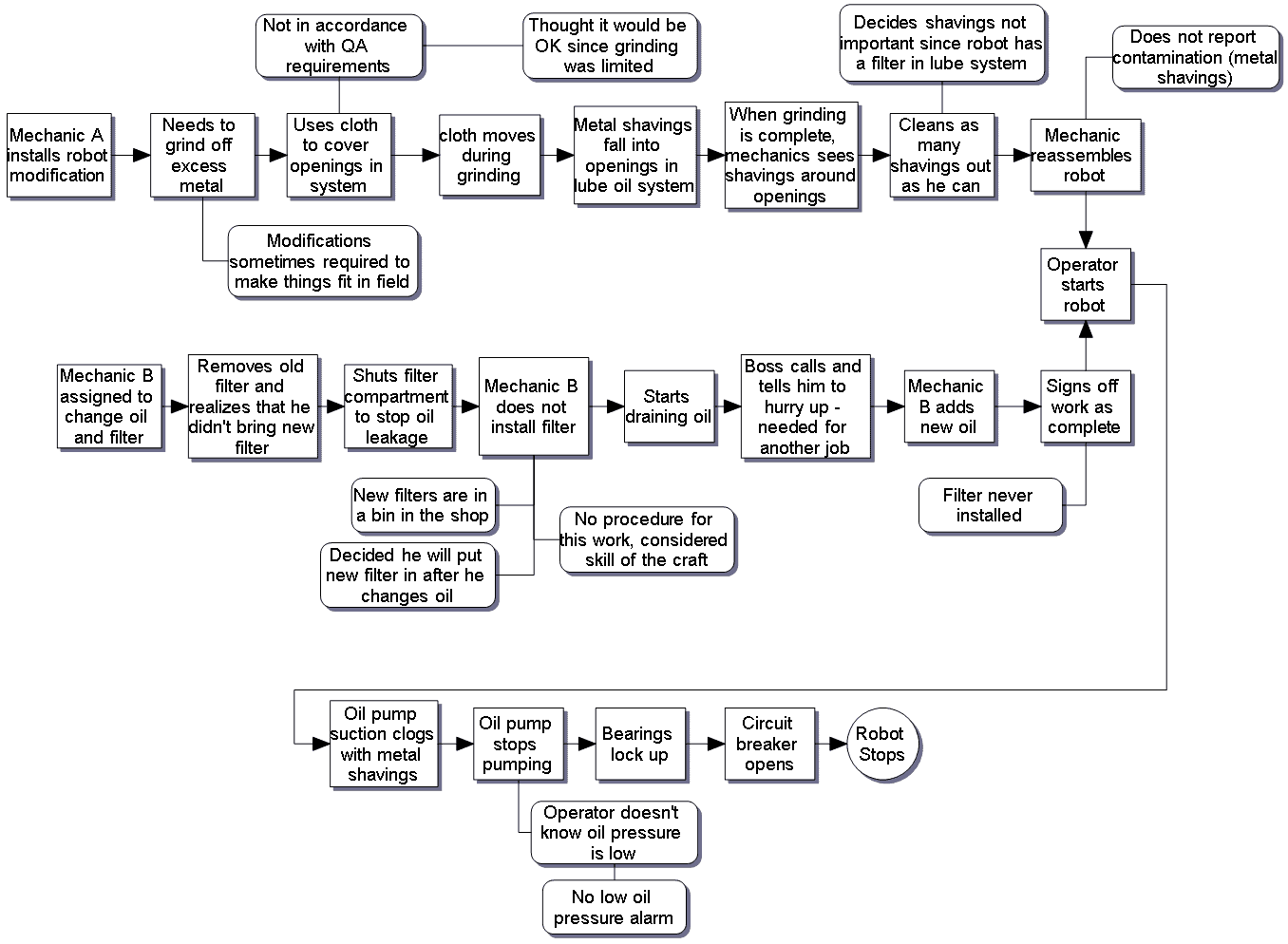
In this case, there are at least two human errors that investigators would not have known about in detail without the mechanics’ cooperation. Also, note that no names are used on the SnapCharT® Diagram. When people clearly see what happened on a SnapCharT® Diagram, they see that the problems could have happened to anyone. Thus, blame (even self-blame) is inappropriate. Instead, changes need to be made to the system.
Idea 3: Celebrate
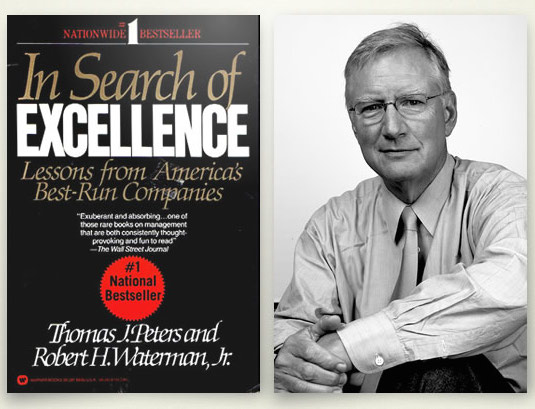
Tom Peters was a famous 1980s/1990s management guru. I was, and am still, a huge fan of this writing. One thing he wrote was that we should “celebrate mistakes” to achieve excellence.
What? You can’t go that far? You just can’t celebrate a mistake. Well, could you at least celebrate successful investigations that discover and fix system problems?
But how do you discover and fix system problems? Once again, that’s easy. You simply apply the Root Cause Tree® Diagram and the Corrective Action Helper Module of the TapRooT® Software. Find out more by downloading this White Paper.
How does celebrating mistakes or successful investigations help? Imagine the difference in morale when there is a celebration instead of punishment after an accident.
Success
I’ve seen rapid turnarounds when fear is eliminated. I’ve seen the downward spiral of blame when the Blame Vision is dominant.
I’ve NEVER seen an honest turnaround when fear is the primary tool. However, I have seen people stop reporting incidents and injuries so that management thinks performance has improved.
What does success look like? See THESE Success Stories.

Don’t wait. Get started today. CLICK HERE to see our upcoming TapRooT® RCA Courses and HERE to learn more about the 2025 Global TapRooT® Summit that focuses on performance improvement.