How to Make a Better Improvement Plan for 2025
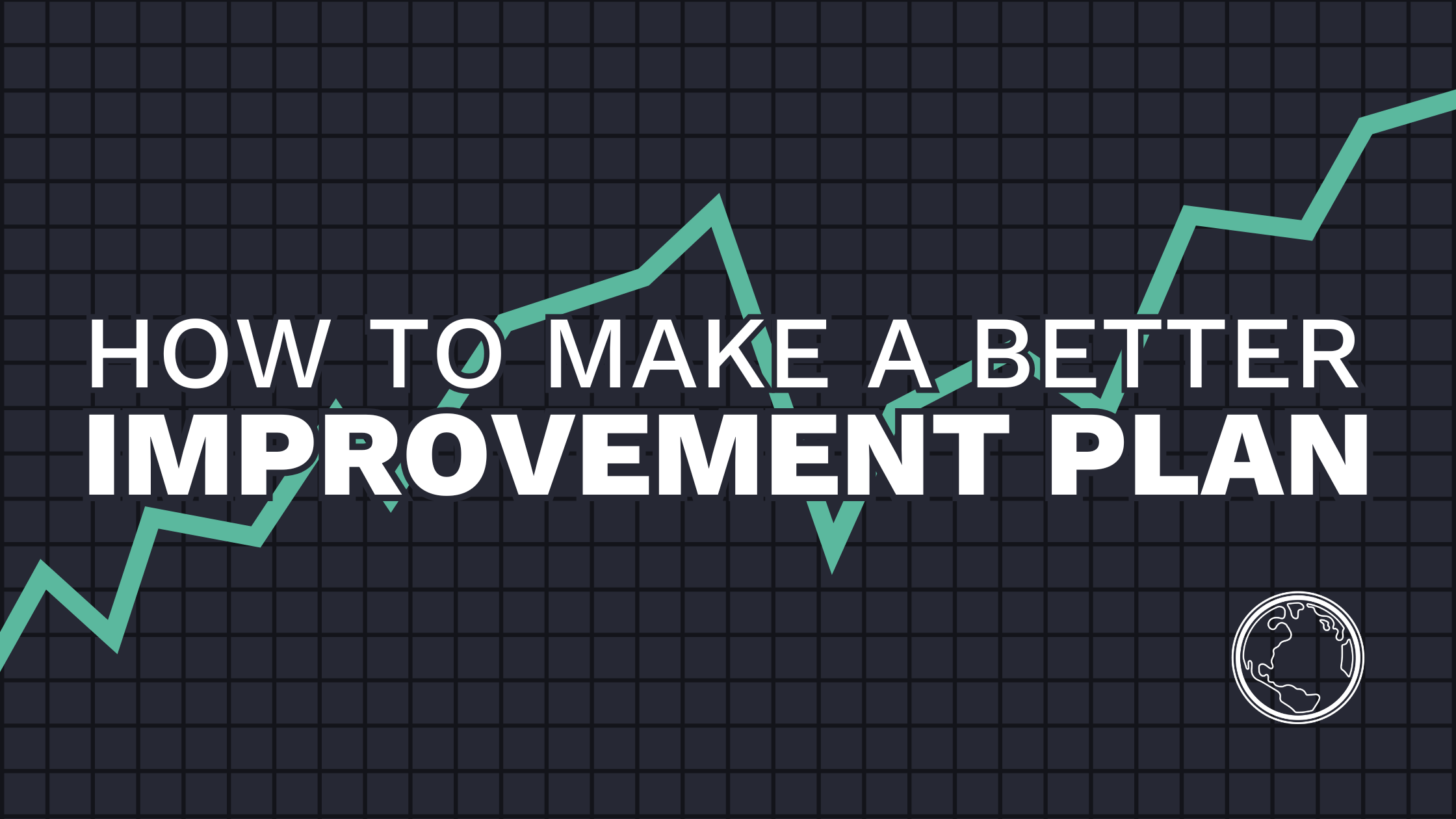
Get Ahead on your Improvement Plan
With a new year comes a new set of aspirations to complete. An improvement plan can help businesses establish goals, delegate responsibilities, implement fixes, or just strategize proactively in a competitive market.
Start on yours sooner than later so that you can start the new year with a solid foundation.
Steps for a Strong Improvement Plan
Understand the Situation

While most online guides recommend to begin an improvement plan by establishing milestones, this isn’t the best practice in reality. Setting improvement goals before you understand the situation means that you’ll be addressing symptoms of a problem, rather than the root causes.
You need to understand what’s happening before you can deduce why it’s happening. Start your plan with an investigation that collects as much information as needed. Answer questions along the lines of:
- Which operations are going well? Which ones are not? What’s different among these?
- Which departments are having issues? Which ones are going smoothly? Do any patterns pop up?
- What equipment has been reliable? What has been unreliable? Any differences between these?
- Et cetera for whichever topics you wish to improve.
Collect and lay out as much information that you need to look into. Once patterns linking the symptoms of the problem start to arise, you can start to investigate the root causes.
TapRooT® RCA uses the SnapCharT® Diagram to display the facts in an organized, objective manner. It can link files and evidence directly into the timeline for ease of use.
Find the Root Causes
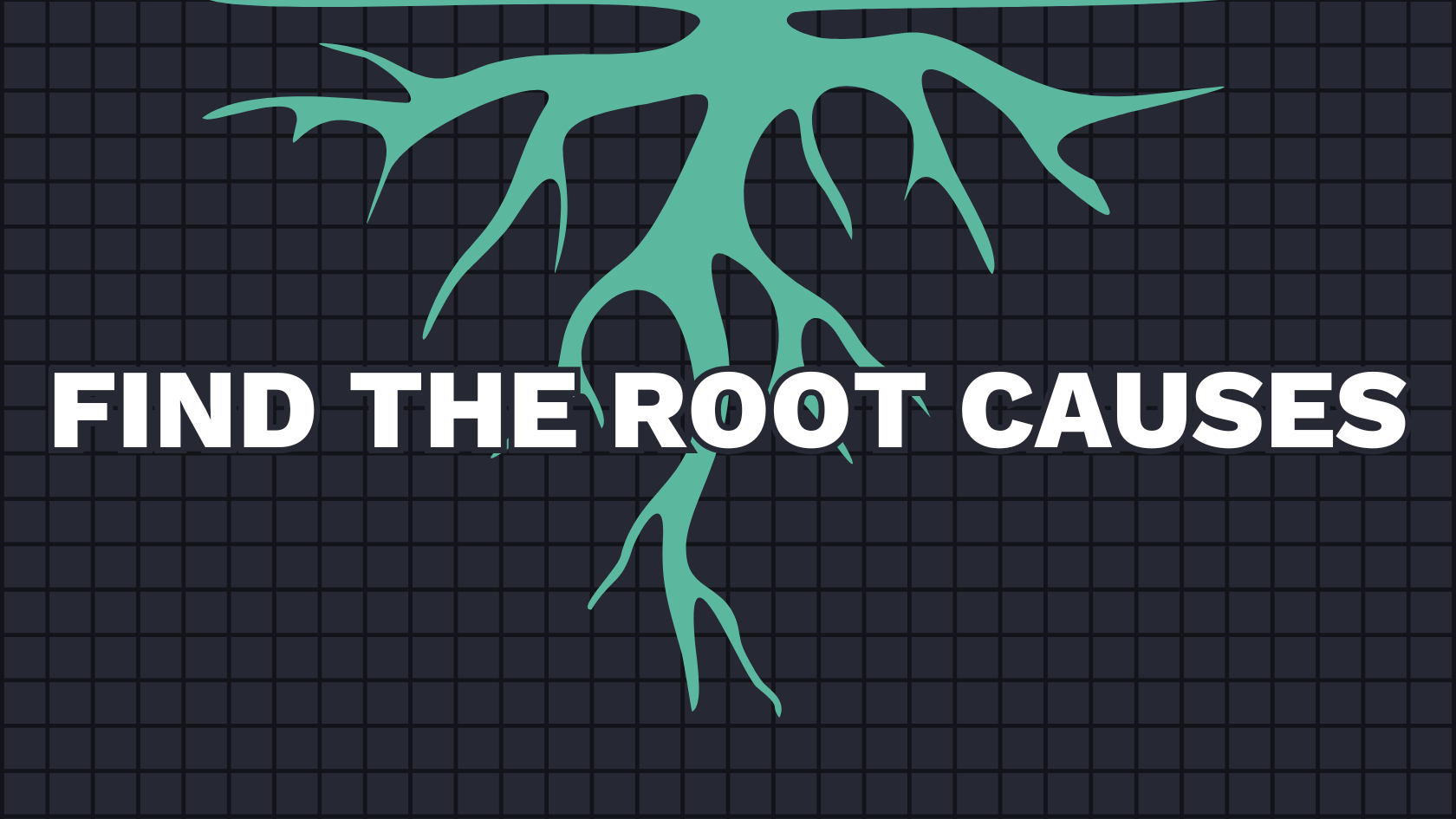
A problem that needs improvement is often the result of multiple failed (or absent) safeguards, which means there are multiple root causes to address.
Defining root causes can be tricky for some teams. If you want to stop the problem reoccurring across the whole organization, think systematically. Look past the mistakes and dig deeply into how these mistakes are allowed to happen in the first place.
Human error, for example, is not a root cause. Humans are bound to make mistakes, so it’s up to the company to put safeguards in place to alleviate them.
Even if the same few employees are slipping up, don’t be so quick to label them as the underlying issue. Here are some other potential causes, just to name a few:
- The training was inadequate for this team.
- These employees are having accessibility issues for any controls.
- There is a lack of supervision for these employees.
- The communication system fails to harbor effective 2-way communication.
- And so on.
If more information is needed to find a systematic failure, there is nothing wrong with jumping back into the previous step and reinvestigating. Never make an assumption about the root cause, or else your improvement plan is the result of guesswork.
The Root Cause Tree® Diagram is a questionnaire to facilitate this process. It asks closed-ended questions about the investigation to efficiently define the root causes.
Develop Corrective Actions
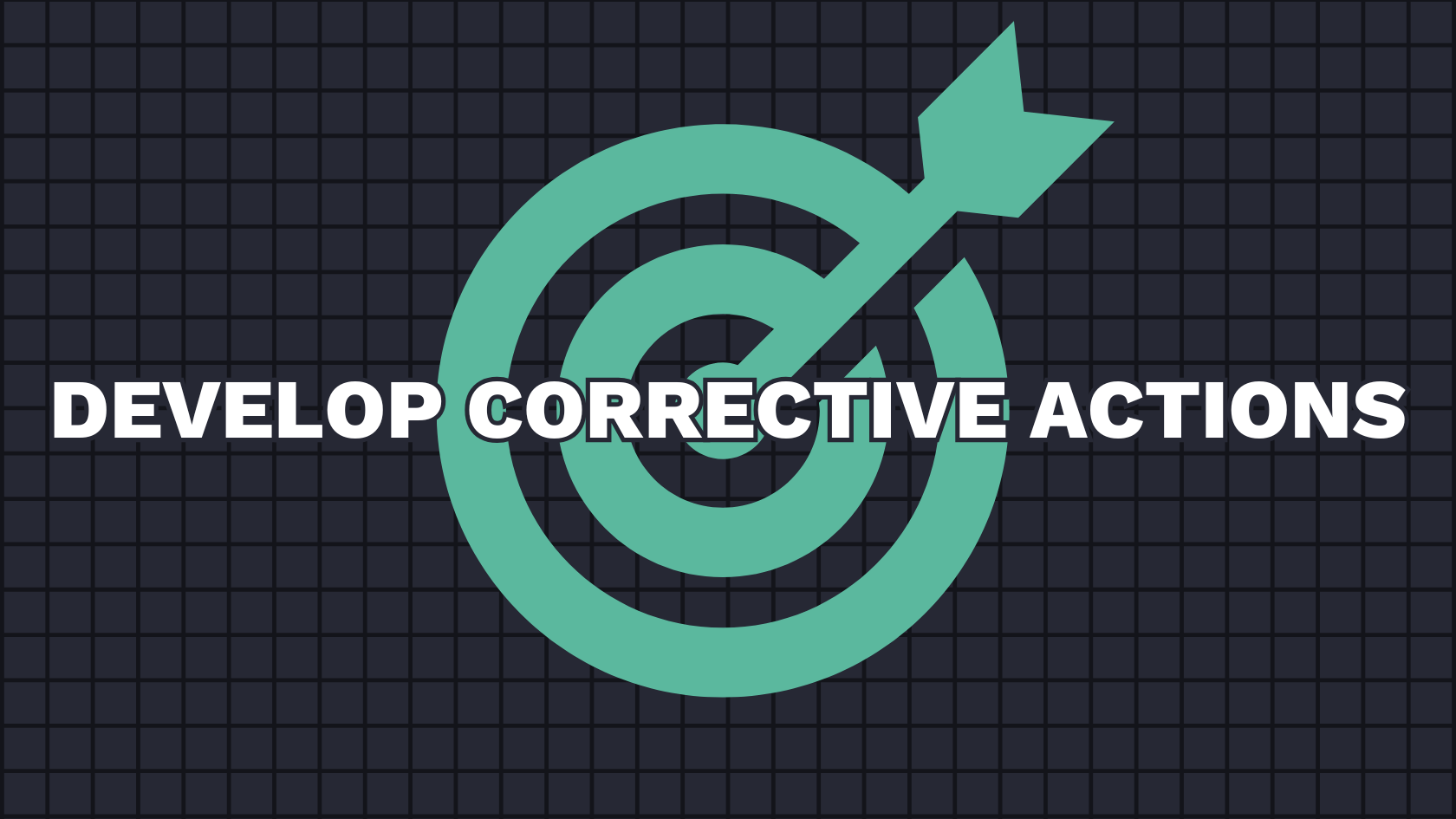
Once you fully understand the situation, you can effectively develop milestones and actions to address the underlying issues. Checklist that your goals are SMARTER:
Specific
Measurable
Accountable
Reasonable
Timely
Effective
Reviewed
You can then assign what should be done, who should be involved, and when should these tasks be completed. This is easier said than done, of course. A small team would be more effective making these decisions than an individual.
Remember that these actions should aim to fix a systematic problem rather than its symptoms. If the action seems to target a small number of employees, reconsider if the improvement plan is really benefitting the team.
The Corrective Action Helper® Guide provides recommended changes based on the root causes. It also includes a template for delegating these responsibilities.
Monitor Progress
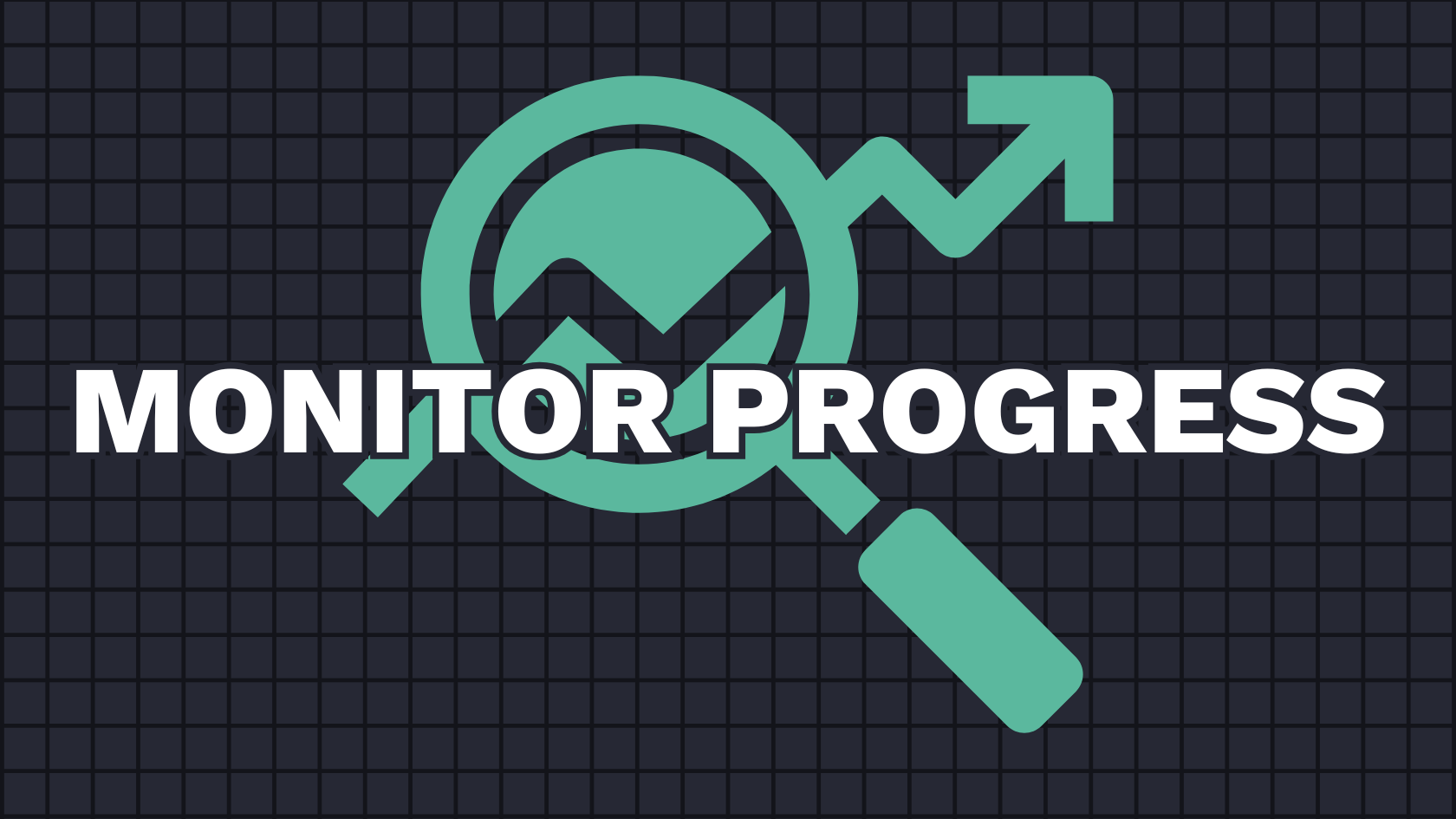
An strong improvement plan doesn’t stop after the corrective actions are established. You need to continuously collect and analyze the effectiveness of your plan with regular audits.
Your evaluation shouldn’t be limited to quantitive data — don’t just look at the numbers. Your improvement plan should open up feedback for the whole team. Qualitative data can help provide specific insights behind and create a more collaborative and hands-on work culture.
TapRooT® RCA includes a grading system to check and coach your team to develop accurate data, logical root causes, effective corrective actions, and so on.
More Resources for Your Improvement Plan
If you need additional help developing an improvement plan, sign up for a free, one-hour executive briefing with us. We help organizations get the bottom of reoccurring issues.
The Improvement Program Track takes place October 1-3, 2025 at the Knoxville Convention center. This provides businesses with best practices and networking opportunities for continuous improvement.