Pre-Summit Course – Which One Should I Attend?

The Best Pre-Summit Course is the One That Helps You the Most
The 2025 Global TapRooT® Summit in Knoxville, Tennessee, is rapidly approaching on October 1-3. Before the Summit, on September 29-30, there is a set of special courses that Mark Paradies hand-picks to provide valuable ideas to help you improve performance at your company.
What are the eleven pre-Summit Courses being held on September 29-30, and which one is best for you? Read on to find out!
11 Pre-Summit Courses
Here are the eleven courses and some information about each course…
2-Day Analyzing and Fixing Safety Culture
Do you believe you are doing a good job of your root cause analysis, investigations, and corrective actions? Yet these actions don’t seem to work or grow as effectively as you might have thought? You may be missing some underlying cultural traits limiting your efforts to improve your safety culture. Brian Tink and Pat Fortune, both experienced TapRooT® Instructors, will help you solve these issues.

The outcomes of safety culture have always been a part of the TapRooT® Root Cause Tree®. This course is designed to give participants a better understanding of how the TapRooT® Root Cause Tree® Diagram and Dictionary identify the results of existing culture within a company. The program will provide insight and tools to go beyond the RooT Cause Tree® Diagram and help you understand the cultural aspects causing your identified root causes. Utilizing the introduced tools and through discussions during the program, participants will understand how to craft better corrective actions. You will learn how to craft corrective actions to be more effective in your existing culture or design them to change an existing culture.
Each participant will complete a Human Synergistics Organizational Cultural Inventory© Survey and a Human Synergistics Organizational Cultural Inventory™ Ideal Survey during the program. These tools will help you gain detailed insight into your company’s culture and, more importantly, what organizational outcomes this culture will cause. Utilizing the knowledge gained from these surveys, corrective actions will be developed utilizing root causes and cultural attributes. At the end of the session, breakout groups will use their examples and cultural results to work through the TapRooT® process and create corrective actions.
Upon returning to your office, you can use what you have learned in this course to understand what is going on culturally at different levels in your organization and, more importantly, how to improve performance effectively. Improving performance can be tricky (as we know). However, the more profound knowledge gained from the material discussed will help make future improvements more effective.
Equifactor® Equipment Troubleshooting & TapRooT® Root Cause Analysis Training
Equifactor® Troubleshooting Techniques are based on the work of the late equipment reliability expert Heinz Bloch and capture how Best-in-Class Performing organizations think differently about their equipment and systems.

In two days, you will learn:
- How to use Equifactor® Troubleshooting Tables to fix equipment failures
- Going beyond troubleshooting to find the real, fixable root causes of failures
- Maintenance and operational best practices
- Holistic, proactive system reliability techniques to ELIMINATE the reasons (plural) equipment failures occur
The tools you will learn include:
- Equifactor® Troubleshooting Tables – a systematic guide to troubleshooting common equipment problems. Don’t guess – prove!
- Troubleshooting Strategy – don’t lose the data! Develop a troubleshooting plan to capture all failure symptoms and possible causes.
- Failure Modes/Failure Agents – there are only four ways a physical component can fail. Don’t FRETT, build the equipment failure narrative (hint, it’s never just a single-point failure)
- Custom Tables – The best use of Equifactor®! If there are no tables, build them, capture the wisdom of your machine experts, build the perfect training document for new equipment troubleshooters, and cut the troubleshooting turnarounds in way less than half by structuring it.
- Proactive Improvement – True solutions are always proactive, even if they’re motivated by failure. If you truly fix a problem, failures don’t recur!
- Change Analysis – “It was working, and now it isn’t” or “The other machines are working. What’s different about this one?” Change analysis structures the intuitive but messy process of comparing machine failures to past performance or similar equipment.
- Root Cause Tree® Diagram – How to find the root causes of equipment failures, including those caused by human performance.
- Developing Effective Fixes – Using the Corrective Action Helper® Guide to develop more effective fixes for the root causes you discover.
Equifactor® Troubleshooting is for maintenance technicians, equipment reliability specialists, maintenance managers, and non-equipment expert investigators. Develop best-in-class performance by asking best-in-class questions.
Justin Clark will be teaching this class. See the complete course outline HERE.
Advanced Communication/Presentation Skills
As accident investigators, safety professionals, and performance improvement experts, the perception of your professional credibility will be dictated by how well you present your findings and deliver your investigative reports.

In 2024, 82% of professionals acknowledge that public speaking and giving presentations are in the top 10 professional fears. Public speaking is no longer standing on stage or reading from notecards. Today’s investigators must be effective communicators and speakers during interviews, virtual calls, voicemails, video messages, and face-to-face presentations.
When you are called upon to demonstrate your investigative skills or report the occurrences detailing an incident, the more you can speak with poise, clarity, and professionalism, the more your messages will be received with less scrutiny and more respect.
The course was developed and is taught by Vincent I. Phipps, one of our most highly praised Keynote Speakers at prior TapRooT® Summits. Don’t miss this chance to learn from a communication expert. See the complete course outline HERE.
2-Day TapRooT® Root Cause Analysis Training

If you have never attended TapRooT® Root Cause Analysis Training and you are looking for a better way to find and fix the root causes of problems that cause accidents or precursor incidents, this is the course for you. See the complete course outline HERE.
If you are a Certified TapRooT® Instructor and you haven’t attended a 2-Day TapRooT® Course given by System Improvements in the past four years, attending this course is a way to view the latest course changes and refresh your skills.
Developing Incident Command System – A New Value Proposition Using TapRooT® Tools
Those who serve on emergency response teams need to quickly assess the complexities of the incident, using their sense of hazard awareness to respond with decisive action and direct a cohesive response effort. If these essential skills are not deliberately cultivated and drilled, a workplace emergency can quickly become far more serious.

In this course, attendees will use the essentials of the 2-Day TapRooT® course and gain the fundamentals of incident command and control, using SnapCharT® to build tabletop drills with the key response components. They will also use the Root Cause Tree® Diagram and Dictionary and Corrective Action Helper® Module to identify opportunities for improvement based on human performance during drills and emergencies. These tools will give first responders, operations personnel, and people in refining, chemical, and industrial settings the tools to take charge and direct their team members to address various aspects of an emergency effectively.
This is a course developed and taught by Joel Solomon. See the complete course outline HERE.
TapRooT® Advanced Case Study Workshop
If you want to sharpen your TapRooT® Skills by using the TapRooT® Root Cause Analysis Techniques to solve practice examples from various industries, this course is for you. This practice analysis will provide excellent refresher training and advanced knowledge for Certified Instructors.

This course has been updated with new examples for 2025 by Tim Diggs. See the complete course outline HERE.
Measurement, Trending, and Predictive Analytics: How the Best Use Data Every Day to Improve Work
Kevin McManus developed and teaches this remarkable course. The course teaches how to develop performance measures and trend them to improve performance.

Too many leaders say that their organizations measure many things, but they often fail to use the data they collect effectively. With so many measures in place, why do so many organizations fail to select and use the right measures? For example, why do we struggle to select key indicators and goals that best reflect true process performance or capability? What does it take to sustain higher performance levels versus merely experiencing them for a day or two?
To make things worse, few leaders, let alone staff, understand and know how to apply the measurement basics of process behavior curve, variation, and capability analysis. Trend line use is limited, and improvement efforts are reactionary. Poorly selected process changes often fail to fix the problem, resulting in a waste of resources. Instead of using data to predict and anticipate change, leaders only use data to find and fix obvious problems.
How often do your leaders try to use organizational or business unit-level metrics to diagnose process-level problems and monitor process health? Such an approach often fails to identify key improvement areas. How do you consistently engage your work team members in daily measure analysis? How does the data they capture daily help drive data literacy and continuous process improvement? Too many measurement system designs provide suboptimal value.
Effective trending and analytics are needed to link process measures with the errors and defects that affect their performance. How do your leaders use work system data to predict future process and business outcomes? How often do your aggregate work measures fail to provide the sensitivity to truly identify work system and process design flaws? What system design flaws prevent your processes from performing at higher levels? How do you effectively use data daily to predict and improve current process performance?

Decades of experimentation, research, and application are captured in the measurement system best practices and strategies Kevin shares in this workshop. This workshop teaches you how to define better measures for any type of work or personal process. It gives you best practice tactics to help you more effectively use the data you capture every day to optimize work process performance. Lastly, it looks at how emerging technologies can help you ‘level up’ your potential for proactive process performance analysis and improvement.
The tested and proven measurement work system designs we share in this workshop will help you significantly improve how you measure, analyze, and improve daily work. Each participant leaves with an action plan for improving their process measurement and analysis processes and a preliminary set of vital signs for those key processes they are responsible for improving.
In this 2-day workshop, you learn how to:
- Identify leading counts and ratios that best reflect the ‘vital signs’ of process performance
- Set up a simple process to capture and crunch daily process information
- Review and use measurement results daily to predict, anticipate, and improve performance
- Recognize and engage team members in effective daily measure use
- Select options to improve the design of your existing measurement work system
Effective Interviewing and Evidence Collection
Barb Carr developed and will teach this class, which is based on the TapRooT® Root Cause Analysis System and ASTM International Standards – a solid foundation for this evidence-collection training. Amy Souders is co-teaching and adds valuable information as an experienced TapRooT® Instructor. Attendees will:
- Learn how to preplan and prepare to document investigations with ease.
- Use a SnapCharT® efficiently as a planning tool for evidence collection.
- Work in teams using a systematic process to collect information,
- Learn how to best label, collect, and record evidence.
- Learn how to conduct an initial site visit.
- Participate in mock interviews practicing the TapRooT® 12-Step Interview Process.

See the complete course outline HERE.
Stopping Human Error
This course, developed by Alex Paradies and Mark Paradies, will help you understand:
- The causes of human error
- Human factors design best practices
- Methods to find error-likely situations
- Techniques to help supervisors and workers prevent human errors
- CHAP (Critical Human Action Profile)
- Human Performance Improvement Technology
- Designing your human performance improvement program.
With the exercises built-in to try the techniques, this is an active, quick-moving, 2-day course that will help you develop a customized, effective, efficient program to improve human performance at your facility.

See the complete course outline HERE.
2-Day Auditing & Proactive Improvement Using TapRooT® RCA
Marcus Miller and Nancy Hitchins developed and will teach the Audits & Proactive Improvement Using TapRooT® Course. This course helps people understand how to use advanced root cause analysis tools to develop their audit protocols and use the human performance and equipment reliability knowledge built into the TapRooT® Root Cause Analysis System to understand the root causes of conditions adverse to quality including non-conformities and non-compliance issues.

Applying TapRooT® Root Cause Analysis proactively when auditing can help your company avoid quality issues, incidents, equipment failures, and accidents by being more effective in your audit processes. See the complete course outline HERE.
TapRooT® Software
Every year, this course evolves to cover the latest improvements in the TapRooT® Software. The course is designed for TapRooT® Software Power Users and Administrators to help them take advantage of all the features built into the TapRooT® Software, including features of the latest releases.
You need to learn how to:
- Create your own Custom Tabs, fields, and pick lists.
- Design and build your own reports.
- Select Global preferences for your company, including Language options.
- Select SnapCharT® preferences for yourself.
- Use Optional investigation techniques.
- Use the TapRooT® App to make investigations more efficient.
Dan Verlinde, Chief Technology Officer, and Angie Comer, Software Project Manager, will teach an intensive review of the TapRooT® VI Software. Whether a System Administrator or a power TapRooT® User, you will learn all the capabilities built into this fantastic software. Don’t get just 10-20% from your software investment. Learn the full power of your TapRooT®Software!
See Dan discuss the course here…
More About the Summit
With all this talk about pre-Summit Courses, you might be interested in learning more about the 2025 Global TapRooT® Summit. The best way to get more information about:
- The five Keynote Speakers,
- The eight Best Practice Tracks, and
- The 44 separate sessions with talks and workshops presented by researchers, industry experts, TapRooT® Users, and TapRooT® Instructors.
is to CLICK HERE.

Or download the Summit brochure by CLICKING HERE.
Or see the complete Summit schedule by CLICKING HERE.
How Do You Register?
Just click THIS LINK to register for the course of your choice and the Summit!
Register for a pre-Summit Course and the Summit and get $300 OFF the course fee.
Bring a team to the Summit and a pre-Summit Course and SAVE up to $900 OFF the combined Summit/Course fee.
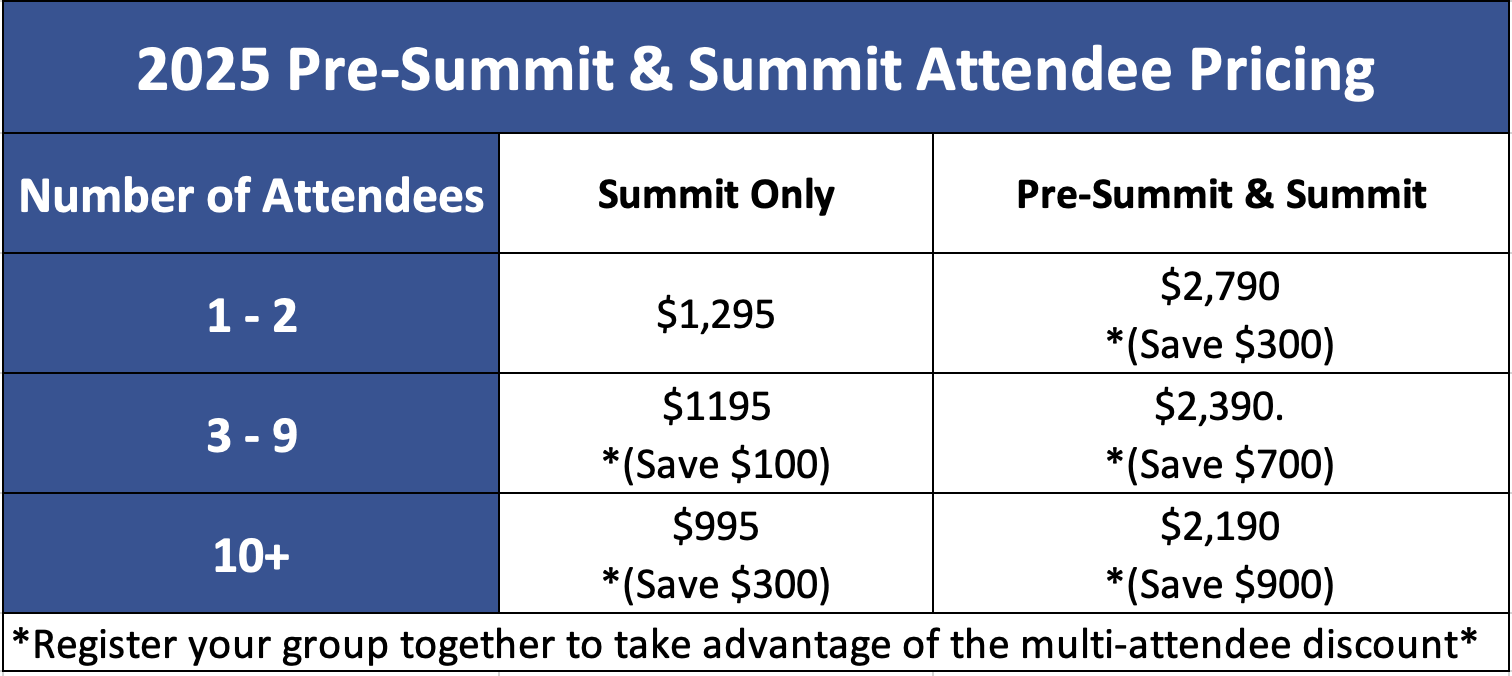
Don’t wait. These pre-Summit Courses fill up fast, and you need the knowledge from these courses to improve performance at your company.
