What Does a Successful Safety Program Look Like?
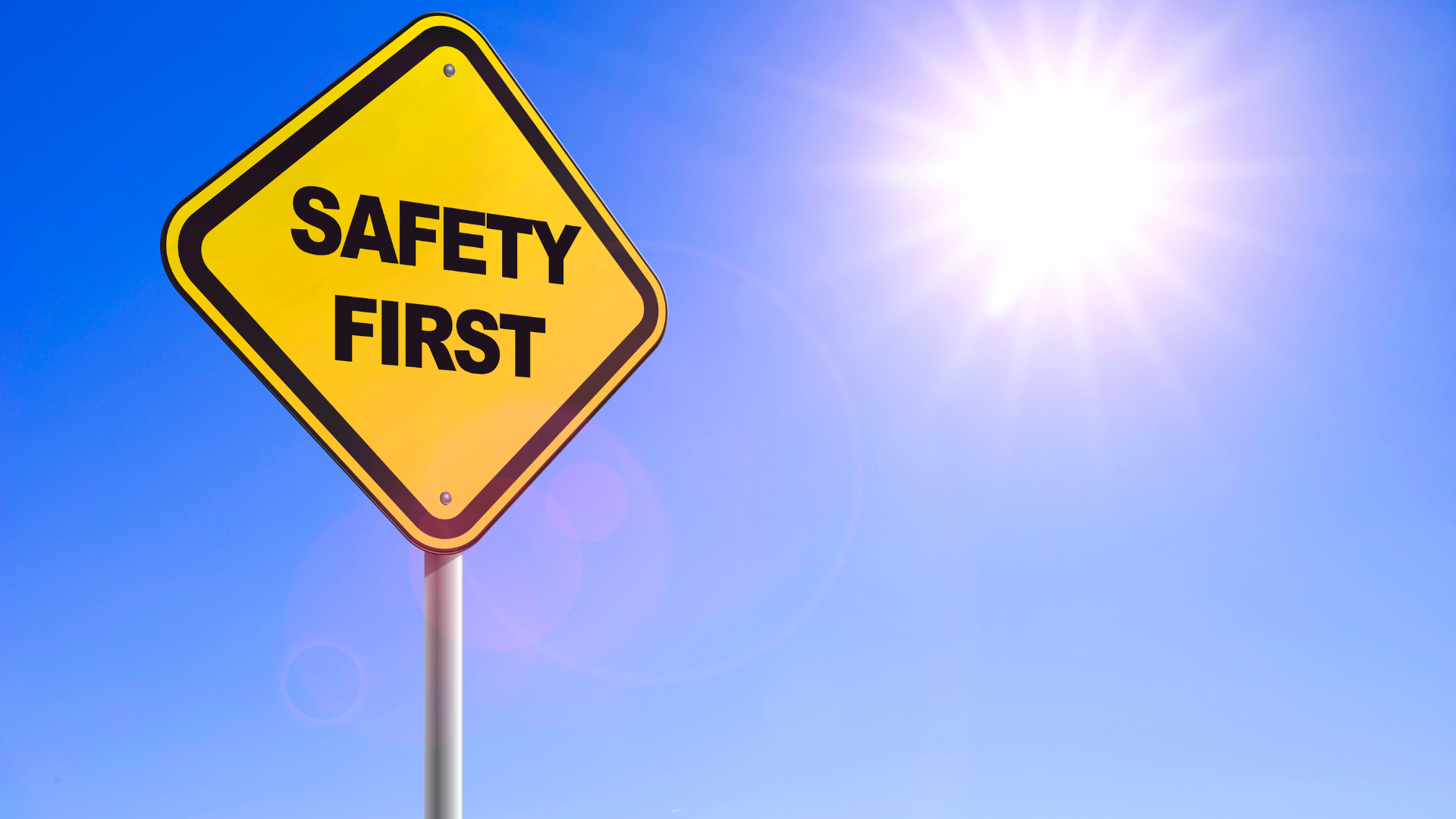
What are the indicators of a successful safety program? If we did a quick poll, we’d probably hear answers like these:
- Fewer near-misses
- No lost-time injuries
- No fatalities
After all, to be best-in-class for safety, your numbers should reflect these types of things. So, what’s wrong with basing the success of your program on the numbers? Well, these numbers are lagging indicators. That means it’s too late to know what was done wrong or even what was done right.
Think about it this way: when a fatality occurs an investigation team must exert a lot of effort and time to understand:
- what happened
- why it happened
- how to prevent it from happening again.
If only the team had understood the hazards that were present before the incident occurred. If only TapRooT® Root Cause Analysis was used proactively to analyze precursor incidents before they turned into major investigations!
Use TapRooT® Root Cause Analysis Proactively for a Successful Safety Program
It takes less time, trouble and heartache to perform a TapRooT® Root Cause Analysis audit than it does to perform a post-incident investigation. If you are ready to build a successful safety program, consider sending your team to 5-Day TapRooT® Advanced Root Cause Analysis Team Leader Training to learn how to use TapRooT® Root Cause Analysis both *proactively* and reactively.
We have courses coming up this summer in Perth, Australia, Monterrey, Mexico, Lake Tahoe, Nevada and Dallas, Texas.
View our upcoming courses worldwide.
The Difference
Define the success of your safety program by what you do to prevent problems from happening, not by the accidents and injuries that do not happen. TapRooT® Root Cause Analysis will help you achieve the success you thought was out of reach in your former approach to safety.