How to Avoid 3 Common Causes of Equipment Failures
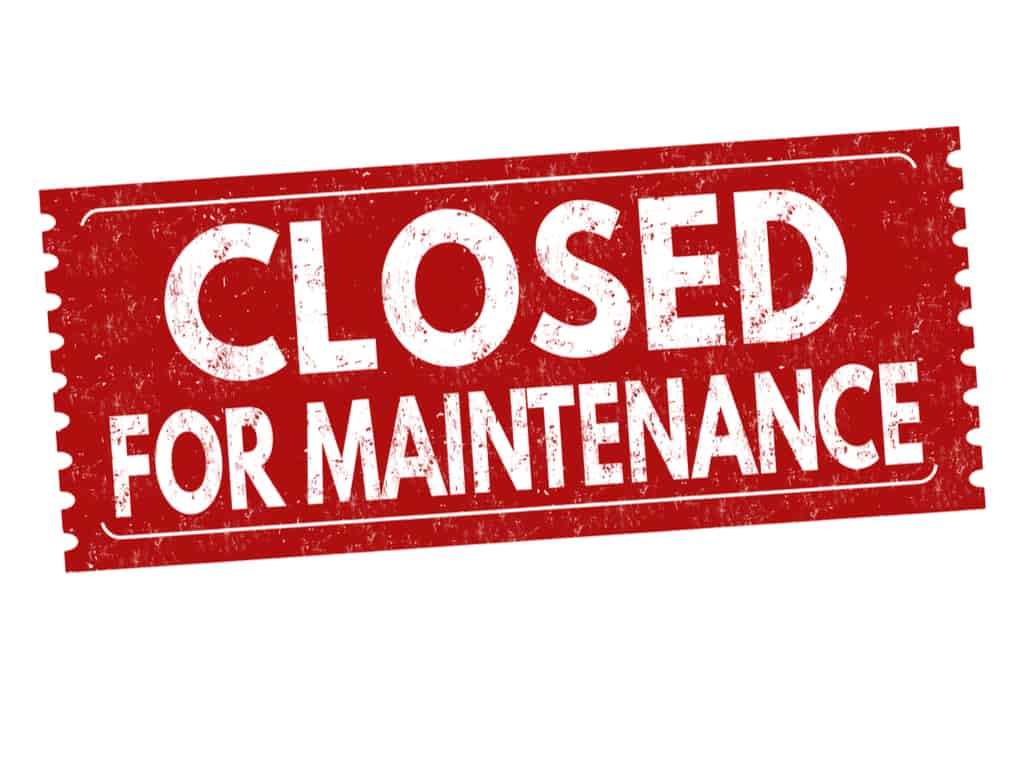
Equipment downtime is costly for all organizations. One of the first lines of defense for avoiding common causes of equipment failures is awareness. Let’s examine three common causes of equipment failures.
One: Improper Operation
Sometimes the root cause of an equipment failure is not due to an equipment problem. Many root causes of equipment failure exist because of human performance problems. How does this happen? We train our workers on operating procedures and safe processes (maybe throwing in a little equipment troubleshooting for good measure). Then someone skips steps in the procedure, takes a safety shortcut “because everyone is doing it,” or asks a worker to work with equipment he/she is not familiar with due to short staff. There are multiple reasons why workers fail to operate machinery properly.
Two: No Preventative Maintenance
When things get busy, preventative maintenance is often the first to go. It’s the “if it ain’t broke, don’t fix it” mentality. When this attitude occurs, early stages of equipment failure go unnoticed by the operators. Small problems with simple, inexpensive solutions turn into major costly breakdowns. The lifespan of the equipment shrinks and costs continue to skyrocket. Keep in mind that every time we take a piece of equipment apart and put it back together again, the expected lifespan gets shorter and shorter!
Three: Failure to Monitor the Equipment
We sometimes adopt a “set it and go” mentality when operating equipment. Manufacturer information, equipment history and real-time data are ignored once the equipment is online. In the rush to get production started, no baseline is established or taught to operators for what good equipment condition looks like. So, operators can’t detect subtle changes which can be used to predict breakdowns and failures.
How familiar are these scenarios to you? Are you ready to reduce costly downtime?
Learn how to find and fix the root causes of equipment failures. This is a great course for incident investigators, equipment operators, and maintenance personnel. Learn how to analyze equipment failures for human performance issues so that no root causes are missed as well as learn how to use the Equifactor® Troubleshooting Tables for true equipment problems.
This course is only offered a few times each year. Register for the next opportunity.
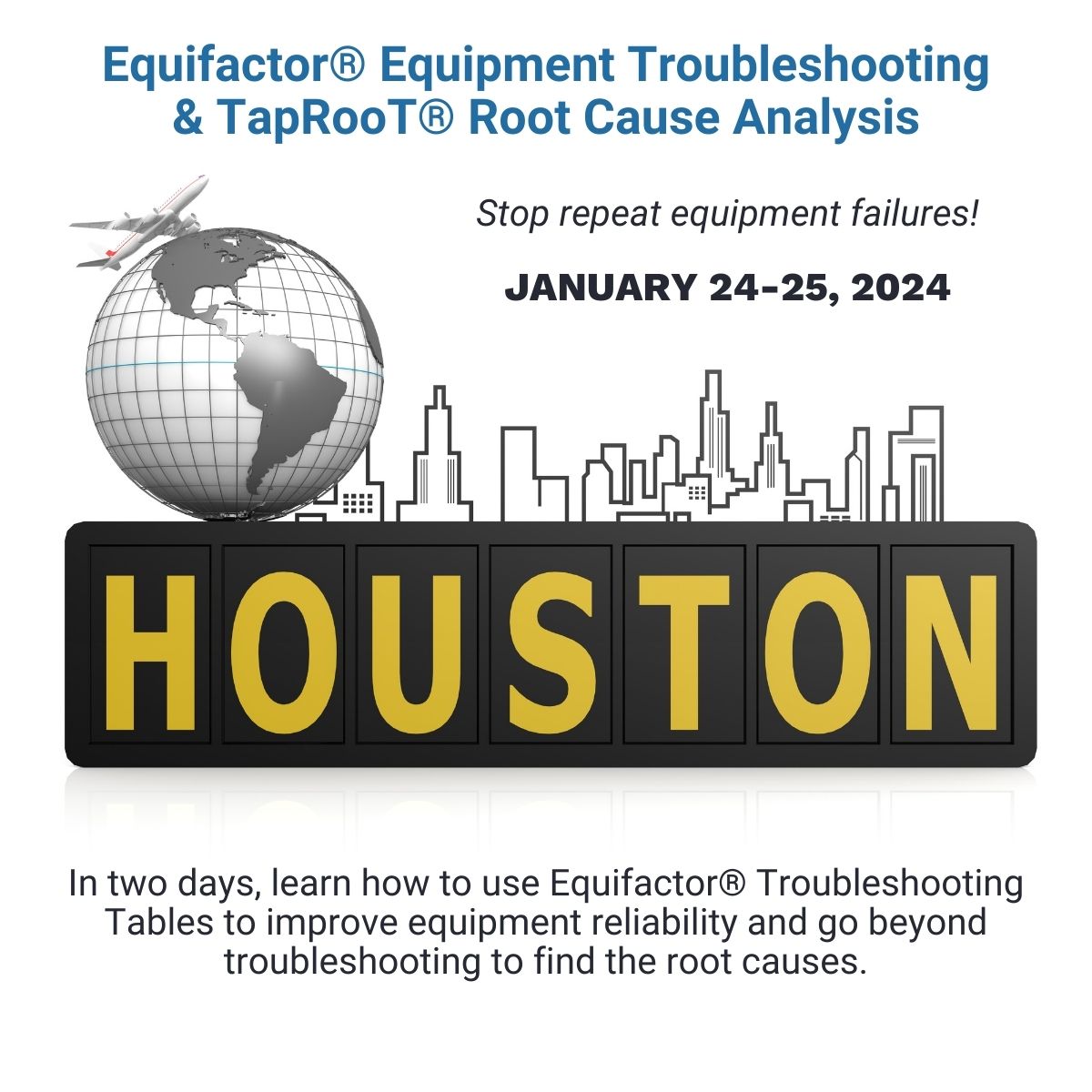