Yokotenkai and TapRooT® RCA
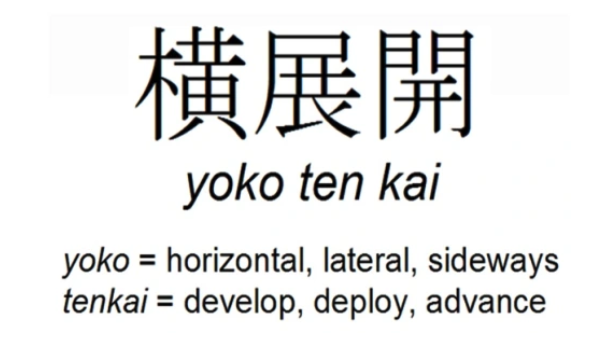
Yokotenkai
The Toyota quality control system is legendary. I’m very new to the quality world, and liked a term I learned while talking a representative from Lego, who has obviously been using that system with equally legendary success.
From the Kaizen Institute

Yokoten essentially means best practice sharing.
This concept is deeply ingrained in TapRooT® Root Cause Analysis. Here’s the definition we use for a root cause:

Gathering best practices and lessons learned should be a constant activity for any organization looking to improve:
- The way they do business,
- Their root cause analysis,
- Their imperfect human performance, and
- The way they achieve equipment reliability.
Unique Best Practice Sharing on April 24-28
The most efficient and reliable way to gather best practices is to attend conferences designed specifically for “Yokoten shimasu” with experts and practitioners from around the world.
If you have a solid quality control program, expand your capability from 5-Why’s and fishbone diagrams by gathering all the best practices for Root Cause Analysis at the Global TapRooT® Summit on April 26-28 at the Margaritaville Lake Resort near Houston. There are eight Best Practice Tracks to share lessons learned and network with industry peers and experts:
- Improving Human Performance Track
- CAPA and Continuous Improvement Track
- Equipment Reliability Track
- Creating a Superior Improvement Program Track
- Safety Improvement Track
- TapRooT® Immersion Experience Track
- Advanced TapRooT® Skills Track
- Instructor Recertification Track
Each track has its own list of speakers/sessions that cover sharing best practices, new techniques to improve performance, and lessons learned by others. Just click on the links above to see the details for each track.
Before the Summit on April 24-25, attend one of these pre-Summit Courses:
- TapRooT® Root Cause Analysis Course
- Equifactor® Equipment Troubleshooting & TapRooT® Root Cause Analysis Course
- Effective Communication Certification
- 2-Day Risk Assessment and Management Best Practices
- TapRooT® Evidence Collection and Interviewing Techniques Course
- Measurement, Trending, and Predictive Analytics: How the Best Use Data to Improve Work
- Getting the Most From Your TapRooT® Software
- Audits and Proactive Improvement Using TapRooT®
- Stopping Human Error
- 1-Day TapRooT® Executive Leadership Course (Tuesday)
Click on any title above for details about that course. If you want to expand your root cause analysis knowledge, I would suggest either the first or second course.
REGISTER for a pre-Summit Course and the Summit and SAVE $300 by CLICKING HERE.
Yokoten shimashou!