Why Does Blame “Make Sense”?
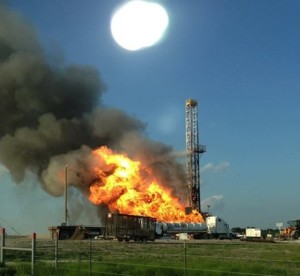
Blame is Common
Think about a recent accident …
- a ship runs aground
- a refinery has a major fire
- an oil well has a blowout and explosion
- a pharmaceutical plant makes a bad batch of drugs, and it gets by the QA process, and customers are harmed
One thing you can be sure of in ALL of the accidents above is that:
Someone screwed up!
You never have a major accident if all the Safeguards function as designed. And guess what … we depend on human actions, in many cases, as a significant or sometimes as the ONLY Safeguard.
Therefore, when an accident happens, there is usually at least one human action Safeguard that failed.
If you are in a blame-oriented organization, the obvious answer is to BLAME the individual (or team) that failed to prevent the accident. If you can find who is to blame and punish them, you can get back to work.
It MAKES SENSE because “if only they had done their job …” the accident would not have happened. Punishing the individual will set an example for everyone else, and they will try harder not to make mistakes.
Sure enough, when the same accident doesn’t happen again right away, management believes they fixed the problem with blame and punishment.
Mistake and Blame
I was thinking of this the other day when someone was talking to me about an investigation they had done using TapRooT®. They had recently adopted TapRooT® and, in the past, had frequently blamed people for accidents.
In this case, a worker had made a mistake when starting up a process. The mistake cost the facility over $100,000. The operator thought that she probably was going to be fired. Her apprehension wasn’t reduced when someone told her she was going to be “taprooted.”
She participated in the investigation and was pleasantly surprised. The investigation identified a number of Causal Factors, including her “screwup.” But, to her surprise, they didn’t just stop there and blame her. They looked at the reasons for her mistake. They found there were three “root causes” that could be fixed (improvements that could be made) that would stop the mistake from being made in the future.
She came away realizing that anybody doing the same job could have made the same mistake. She saw how the investigation had improved the process to prevent future similar mistakes. She became a true believer in the TapRooT® System.
Blame Does Not Make Sense
When you discover the real fixable root causes of human performance-related Causal Factors, BLAME DOES NOT MAKE SENSE. In fact, blame is counter-productive.
If people see that the outcome of an investigation is usually blame and discipline, it won’t take long until most incidents, if at all possible, become mystery incidents.
What is a mystery incident?
A refinery plant manager told me this story:
Early in his career, he had been an engineer involved in the construction and startup of a major facility. One day, when they were doing testing, the electrical power to some vital equipment was lost and then came back on “by itself.” This caused damage to some of the equipment and a delay in the startup of the plant. An investigation was performed, and no reason for the power failure or the reason for the power coming back on could be found. No one admitted to being in the vicinity of the breaker, and the breaker was closed when it was checked after the incident.
Thirty years later, they held an unofficial reunion of people who had worked on the project. At dinner, people shared funny stories about others and events that had happened. An electrician shared his story about accidentally opening the wrong breaker (they weren’t labeled) and then, when he heard alarms going off, re-shutting the breaker and leaving the area. He said “Well, I’m retired and they can’t punish me for it now.”
That electrician’s actions had been the cause of the incident. The refinery manager telling the story added that the electrician probably would have been fired if he had admitted what he had done at the time. The refinery manager then added that, “It is a good thing that we use TapRooT® and know better than to react to incidents that way. Now we look for and find root causes that improve our processes.”
Get Beyond Blame
Are you looking for the root causes of incidents and improving processes? Or are you still back in the “bad old days” blaming people when a mistake happens?
If you haven’t been to a TapRooT® Course, maybe you should register to attend one and see how to get beyond blame to find the real, fixable root causes of human error.
See our upcoming TapRooT® Courses by clicking on THIS LINK.
Or contact us to get a quote for a course at your site by CLICKING HERE.
And, if your management still thinks that blame and punishment are good ideas, maybe you should find a way to pass this article along (without being identified and blamed).