Why Do We Still Have Major Process Safety Accidents?
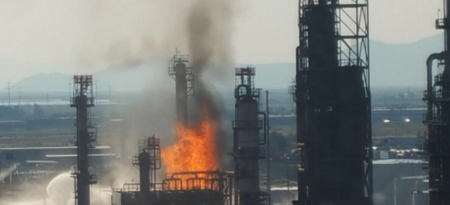
Disagreement Leads to Understanding
Why do we still have major process safety accidents? I had an interesting disagreement with a colleague at a conference. It was about root cause analysis and process safety. The person argued that 5-Whys was a good technique for root cause analysis of process safety incidents with low consequences. I disagreed. Read on for the understanding that I realized that might be why we keep having major process safety accidents…
Low-Consequence Process Safety Incidents
MOST process safety incidents have low actual consequences. Many times these low-consequence incidents are just one Safeguard away from a major accident. Occasionally that Safeguard is luck.
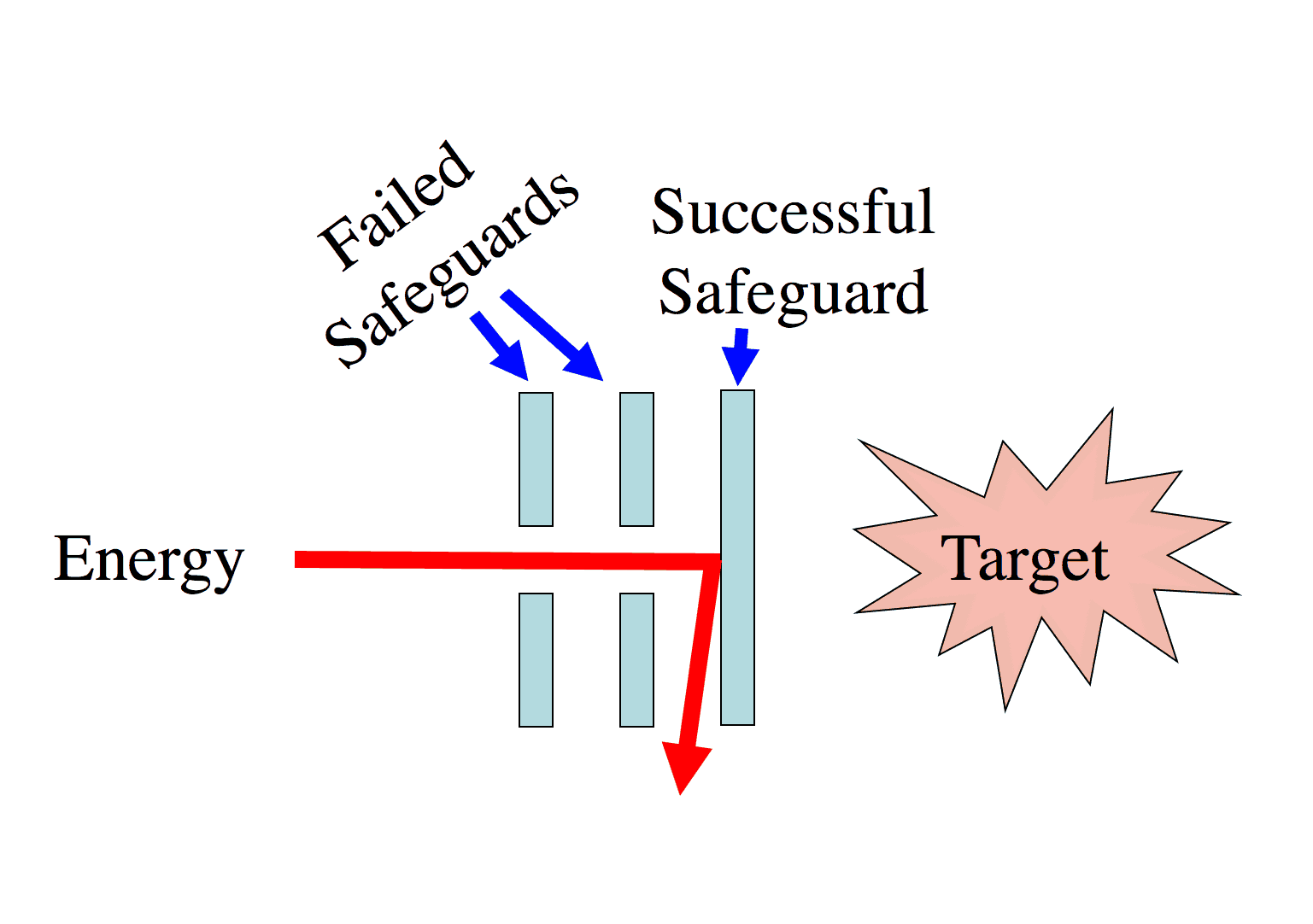
Why do these low-consequence process safety incidents need to be taken seriously? They are major accident precursors. If one or more additional Safeguards had failed, they would become a major accident—a disaster. The Chemical Safety Board, OSHA, and/or the EPA might send a team to investigate. And in many jurisdictions, criminal charges might be brought against the company or company management. And worse yet, they could result in multiple fatalities.

In other words, their potential consequences are high even though their actual consequences are low.
Why is this? Process safety usually employs several redundant safeguards. Some call it defense in depth. Therefore, the failure of a single safeguard, or even multiple safeguards, doesn’t cause a major accident.
Because of this redundancy, people can start to become complacent when a single Safeguard fails. After all, there are several more, and nothing really happens when a single Safeguard fails. People may even jumper protective relays or allow the operation of a system with alarms malfunctioning (failed Safeguards). You can see where this leads – a reduced safety margin. We get closer and closer to a major accident without realizing it.
Thus, the failure of a single Safeguard, or several Safeguards, seems like an insignificant incident when, in reality, it is a precursor to a major accident.
An Example of a Failure to Investigate Precursor Incidents
Do you need an example of the failure of multiple Safeguards causing a major process safety incident? There are many, but how about a fire that could be seen from space (as in the NASA photo below)? That’s the Buncefield tank explosion and fire.
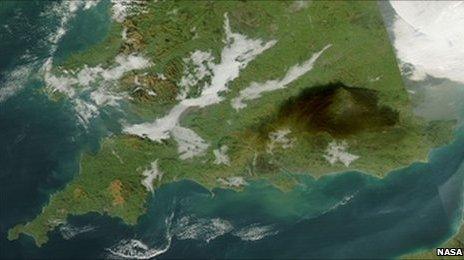
HERE is a description of the failure of multiple Safeguards. It includes the failure of:
- the operator’s observation of the filling,
- a tank’s level sensor,
- two level alarms,
- an independent safety instrumented system, and
- the physical containment.
All of these Safeguards had failed in the past, but they had never all failed simultaneously. When those previously mentioned failures combined with a still, windless night with high humidity, a major explosion and fire occurred.
Supervisors had informally investigated the previous failures of independent components, but they were not recognized as precursor incidents, and advanced root cause analysis had not been effectively applied. If the precursor incidents had been thoroughly investigated with effective root cause analysis and corrective actions, this major process safety accident could have been prevented (see page 672 of A Technical Analysis of the Buncefield Explosion and Fire).
5-Whys is an Inferior RCA Technique

From my previous writings, you know that I consider 5-Whys to be an inferior root cause analysis tool. Just these three examples of my writing should convince you (if you need convincing)…
- Comparing 5-Whys with Advanced Root Cause Analysis
- Under Scrutiny
- Teruyuki Minoura (Toyota Exec) Talks About Problems with 5-Whys
If you don’t have time to read the links above, then consider the results you have observed when people use 5-Whys. The results I commonly see are:
- Inconsistent analysis (different people get different results when analyzing the same problem)
- Analysis prone to bias (they get what they look for)
- Analysis that stops at human error
- Failure to identify management system root causes
And that’s just the start of the list of 5-Why performance problems.
Don’t Take That Risk!
So, why do people say that 5-Whys is a good technique (or a “good enough” technique) for investigating simple process safety incidents? It usually comes down to their CONFIDENCE.
They are confident in their ability to find the causes of problems without a systematic approach to root cause analysis. They are smart people and believe they already know the answers to these simple problems. They believe advanced root cause analysis is a waste of time when they already know the answers. Thus, their knowledge and a simple (inferior) technique are enough.
Because they have so much confidence in their ability, it is difficult to show them the weaknesses in 5-Whys because their answer is always:
“Of course, any technique can be misused,
but a good 5-Whys wouldn’t have that problem.”
And a good 5-Whys is the one they do.
If you point out problems with one of their root cause analyses using 5-Whys, they say you are nitpicking and stop the conversation because you are “overly critical” and “no technique is perfect.”
Of course, I agree. No technique is perfect. But some are much better than others. The results show when the techniques are applied, and the results are compared.
And that got me thinking …
How many major accidents had precursor incidents
that were investigated using 5-Whys, and the corrective
actions were ineffective (didn’t prevent the major accident)?
Next time you have a major process safety accident, look for previous precursor incidents and check why their root cause analysis and corrective actions didn’t prevent the major accident. Maybe that will help provide convincing evidence that 5-Why root cause analysis isn’t adequate for process safety incident investigation.
However, I suggest that you shouldn’t wait for the next major process safety accident. That is a RISK that you shouldn’t take. Instead, you need to learn advanced root cause analysis NOW and start applying it to precursor process safety incidents to learn how to stop major process safety accidents.
One Additional Benefit
There is one additional benefit when investigators apply advanced root cause analysis to precursor process safety incidents. The investigator gets practice applying the techniques. This helps them become better investigators.

Of course, preventing major process safety accidents is the main reason to apply advanced root cause analysis. But the practice gained when investigating low-consequence process safety incidents will help your investigators gain confidence when applying the techniques when investigating process safety accidents with serious outcomes (if you ever have one).
How to Learn Advanced Root Cause Analysis
What course should you take to learn advanced root cause analysis? If you are going to analyze process safety incidents that have the potential for serious consequences (and perhaps one day lead a team investigating a major accident), I recommend the 5-Day TapRooT® Advanced Root Cause Analysis Team Leader Training.
This course includes the following money-back guarantee:
Attend this course, go back to work, and use what you have learned. If you don’t find root causes that you previously would have overlooked and if you and your management don’t agree that the corrective actions that you recommend are much more effective, just return your course materials, and we will refund the entire course fee.
This iron-clad guarantee should assure you that you will benefit from this advanced root cause analysis training and learn to investigate both minor and major incidents and develop effective corrective actions to prevent future incidents.
To register for an upcoming public 5-Day Course, see the dates and location at THIS LINK.
To hold a 5-Day Course at your site, contact us by CLICKING HERE or call us at 865-539-2139.
And to see the other root cause analysis training that we provide, CLICK HERE.

(Note: This article was originally published in this blog in 2018 and was revised and republished here. We think the lessons suggested above are just as applicable today. We hope that you agree.)