When Should I Do a TapRooT® Investigation?
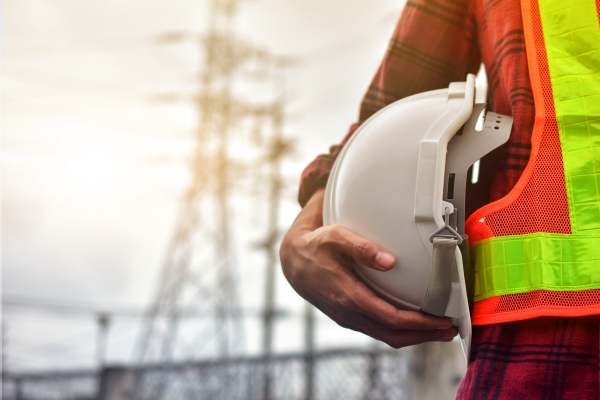
Repeat issues, injuries, or equipment failures tell you that one of the following two is true:
- You don’t understand the problem
- Someone does understand the problem and chooses not to fix it
There are many reasons why people will not do a TapRooT® Investigation. Let’s look at the following example.
“We don’t have enough time to do a TapRooT® Investigation”
EQUALS
“I (or my leaders) don’t care enough about this outcome to prove what allowed it to happen”
EQUALS
“I’m fine if this happens again”
EQUALS
“This was a tolerable failure”
Calling equipment failure “tolerable” or due to “wear and tear” is simply unacceptable. Failures are not tolerable if they
- are not fully understood
- are repeat issues
- stop production
- injure a human
- damage equipment
Do a TapRooT® Investigation When You Want to Prevent the Accident from Happening Again
A TapRooT® Investigation for a single, infrequent minor injury may not be worth it. But living with 600 pinch point or eye injuries a year (I’m looking at YOU construction), you’re ignoring 600 opportunities to improve. 600 unique scenarios? Yeah, right.
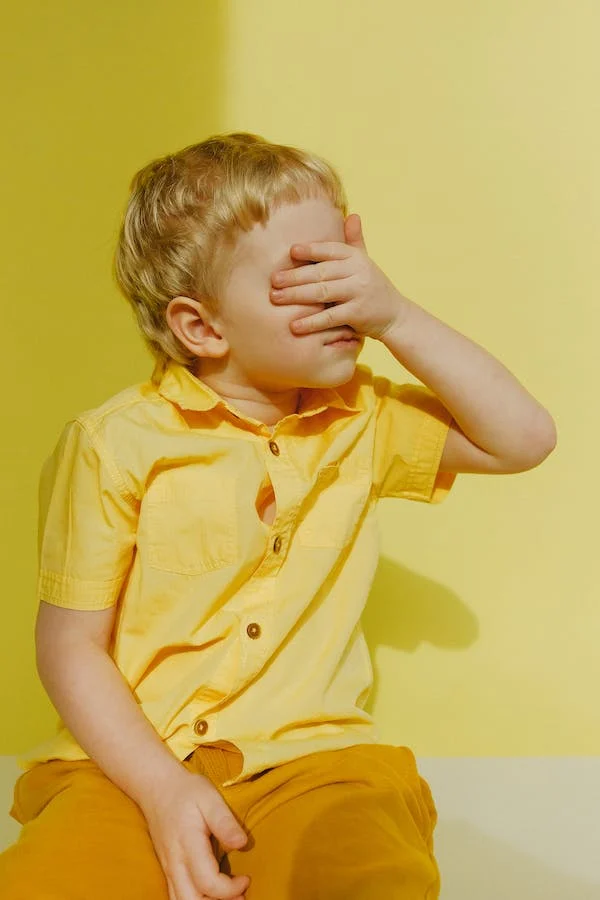
“But I can’t do that many investigations!” You know what, Dr. Jones, you’re absolutely right!
You’re not going to do 600 TapRooT®s, you’re going to do ONE.
TapRooT® RCA is not a system for logging accidents; it’s a Root Cause Analysis methodology to prove, from one investigation, the missing best practices or failures to apply knowledge (root causes) that allowed the accident, and the corrective actions necessary to prevent anything similar from ever happening again.
“It is a SHAME to management and investigators to find and live with repeat issues.“
Now when investigating a truly unique issue, TapRooT® is the only system with a defined, objective endpoint. Guidance and structure tell your investigators when they’ve gone far enough. Standardization isn’t anything new. The secret sauce is, and read this carefully,
If your TapRooT® RCA takes too much time, you’re skipping steps.
5-Why’s investigations can drag on for months because there’s no structure, system, or endpoint when TapRooT® Root Cause Analysis would have made short work. I’ve also seen minor accident TapRooT® investigations drag on for days when they should have taken 4 hours max because the lead investigator simply didn’t follow the standard process.
How long does a TapRooT® investigation take? Less time than documenting 600 injuries.
How many people do I need to be trained? Possibly just one!
Send your lead investigator to a public 5-Day Advanced Root Cause Analysis (Team Leader) course and learn how to investigate everything from sprained ankles to Deepwater Horizon.
Want to learn how everyone from the smallest mom-and-pops to the biggest global corporations has implemented TapRooT®? Come to the Global TapRooT® Summit on Root Cause Analysis. No expo floor to avoid. The Summit is a professional conference to learn and share best practices, and network with leaders and practitioners across all industries.