When Should a Supervisor Be at the Job Site Supervising? How Do They Know?
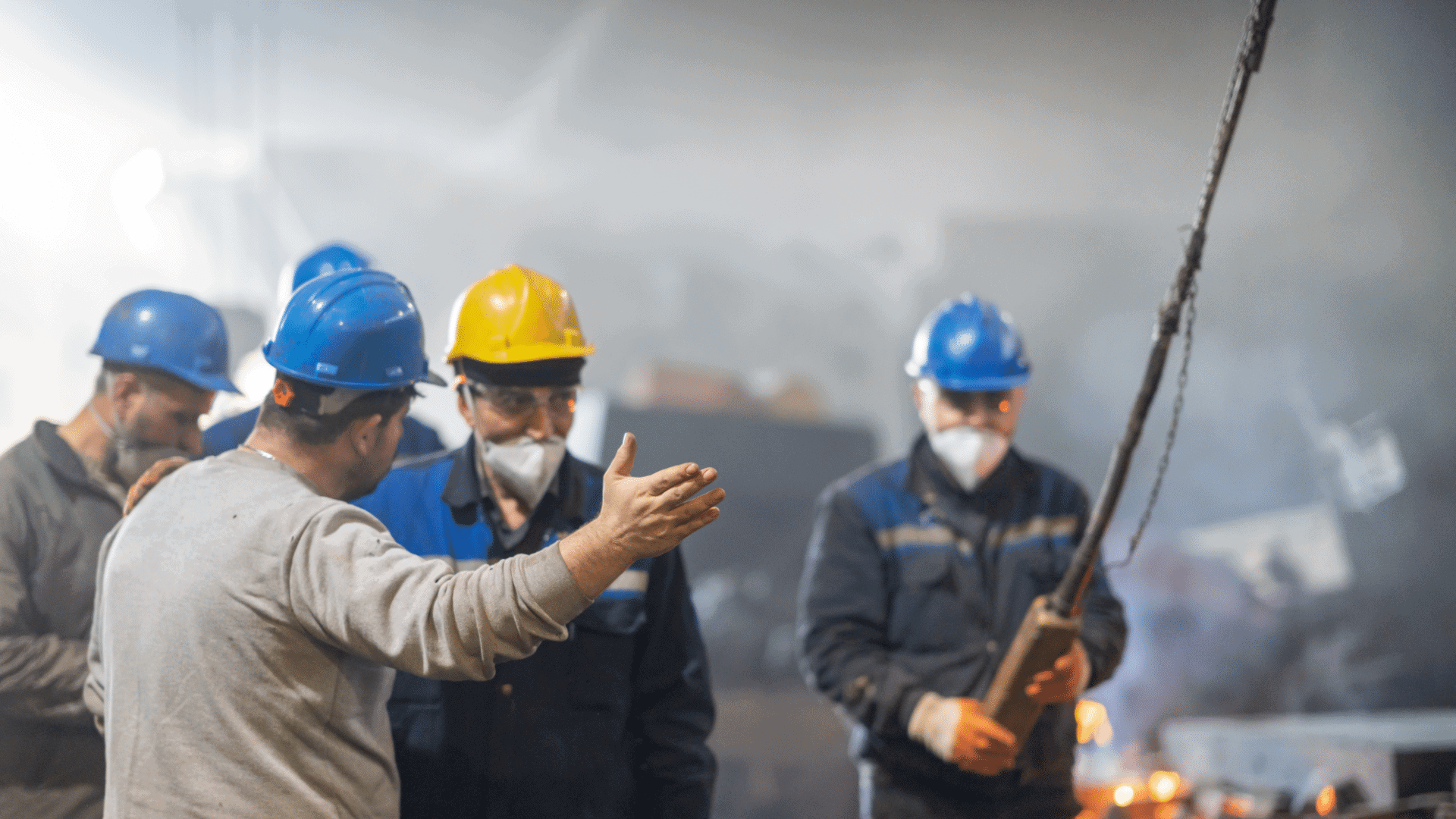
Is Supervision Important for Good Human Performance?
Supervisors always have too much to do. Administrative tasks seem to take more and more time. Many supervisors find it difficult to get out of the office and into the field.
Can you give supervisors guidance for when it is critical for them to be in the field when work is occurring? Can supervisors provide themselves with guidance about the critical times to observe work and coach workers?
Those questions are part of the Stopping Human Error Course that is coming up on October 4-5 in Knoxville, Tennessee.
Hazard Analysis, Safeguards, PPE, & Supervisors
Pre-Job Hazard Analysis (sometimes called a pre-job safety assessment or a job safety assessment – JSA) is a critical tool to help supervisors prepare for a job. It helps them:
- Prepare their pre-job brief
- Understand the PPE requirements
- Evaluate existing Safeguards
- Develop work permits
- Decide when they need to be in the field to observe the work
In the Stopping Human Error Course we teach a seven step process to help supervisors perform a pre-job hazard analysis and incorporate the results into the list above.
We also teach other advanced concepts, including the Hazard Wheel, to help supervisors perform a better pre-job hazard analysis.

Applying these tools helps the supervisor become a critical part of management’s efforts to stop Normalization of Deviation – a critical part of preventing major accidents (especially process safety-related accidents).

Learn More About the Supervisors Role in Excellent Human Performance
Often supervisors are left without much guidance on where to focus their efforts. Sometimes this leaves them to concentrate on paperwork rather than the critical tasks that need their attention. This can result in operators and mechanics believing that shortcuts are OK (or maybe even encouraged).
Supervisors need guidance on when to be in the field checking on the use of Safeguards and PPE. They need to be aware of the critical steps in the job. They can provide guidance for themselves by applying pre-job hazard analysis.
Would you like to learn more about this important technique and other techniques that can make significant improvements in the excellence of your operator’s and mechanic’s human performance? Then plan to attend the Stopping Human Error Course coming up in Knoxville, TN, on October 4-5.
Several years ago at Barrick we struggled with the problem of ‘how much time in the field’. After considerable debate and discussion a senior VP said “let’s try for: senior managers 10%, middle managers/foremen 30% and frontline supervisors 90% time in the field”. When site managers pushed hard this worked well. Other site managers who didn’t buy in did not have the same improvement. Overall, striving to meet those targets (sometimes achieved, sometimes not) resulted in a dramatic decrease in incidents.
Thanks Bruce – Sounds like good advice. Especially if supported by senior management.