When a Small System Weakness Is a Potential Major Problem (Hint: TapRooT® Is the Obvious Answer)
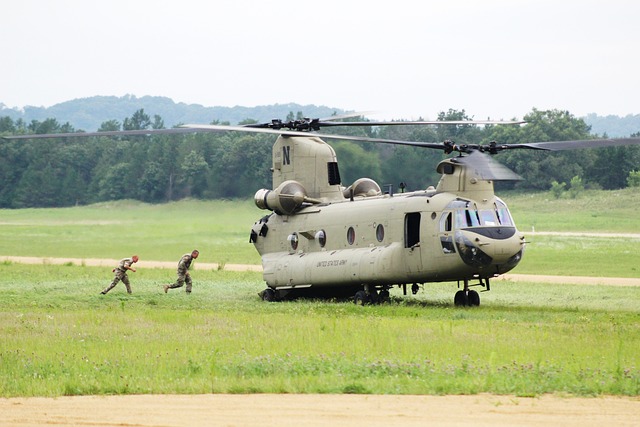
I recently saw a story in the Wall Street Journal about treatment of a major problem, U.S. Army grounds entire fleet of CH-47 Chinook helicopters due to a risk of engine fires.
How does a problem such as this happen — the grounding of an entire fleet? In this case, a design flaw was found on the O-rings AFTER the component was installed on Chinook helicopters during routine maintenance. The design flaw caused a few engine fires because of fuel leakage. Luckily there were no deaths or injuries because of the fires. Out of caution, the army has taken the helicopters out of service until they can be sure the risk is contained. Think about the resources it takes to plan and execute the grounding of 400+ Chinook helicopters while still finding a way to support the movement of troops and supplies.
Obviously, there was a system weakness that allowed the design flaw to go unnoticed until it actually caused a problem. Using the TapRooT® process proactively can help identify and fix system weaknesses before they cause huge disruptions or malfunctions, such as we are seeing with the Chinooks.
System weaknesses and root causes are simply the absence of knowledge or best practices, that if in place, would have prevented the problem.
Using the TapRooT® methodology and RCA tools proactively helps you identify where system weaknesses/root causes exist BEFORE they cause problems.
The proactive identification of system weaknesses allows you to introduce the missing best practices or knowledge through the implementation of effective corrective actions so you don’t have to deal with the consequences of an incident or problem.
You proactively shore up the system weakness so you don’t have the incident. The TapRooT® Corrective Action Helper® will give you ideas on how to build those effective corrective actions for every root cause on the back of the TapRooT® Root Cause Tree.
Why is TapRooT® Training the top RCA training?
TapRooT® RCA has been designed for investigating seemingly simple problems that could have been worse (precursor incidents) by using a simple 5-step process. TapRooT® RCA can also be used to investigate major accidents by using the complete 7-step process.
- The 2-Day TapRooT® Root Cause Analysis Course teaches the essential techniques for investigating precursor incidents and fixing them to prevent major accidents.
- The Equifactor® Training Course also teaches how to use the TapRooT® techniques and Equifactor® Troubleshooting Tables to stop equipment problems.
- The 5-Day TapRooT® Advanced Root Cause Analysis Team Leader Training teaches the complete 7-step TapRooT® process and techniques to investigate major accidents, serious environmental releases, fatalities, major plant upsets, and serious injuries, as well as simple incidents.
Learn to Use TapRooT® RCA Proactively
On April 24-25, there is a special course titled:
Auditing & Proactive Improvement Using TapRooT®
Click on the link above for complete course information.
The course is being held at the Margaritaville Lake Resort, Lake Conroe, near Houston, Texas, just before the 2023 Global TapRooT® Summit (April 26-28).
To register for the course and the Summit and SAVE $300 OFF the course fee, CLICK HERE.
To register just for the course, CLICK HERE.
