What’s the Difference Between Equipment Troubleshooting & Root Cause Analysis?
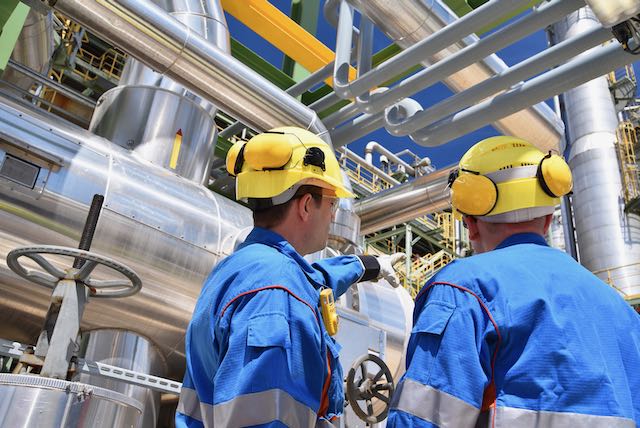
Difference Between Troubleshooting & Root Cause Analysis
Back in the 90s, we had people using TapRooT® to find the root cause analysis of equipment failures. But there was a problem. There wasn’t a clear line between equipment troubleshooting and root cause analysis.
Many times people tried to start looking for root causes when they hadn’t finished troubleshooting the equipment failure.
So, what’s the difference between troubleshooting and RCA?
Equipment troubleshooting starts with knowledge of the equipment and the symptoms of the failure.
For example, if a pump won’t pump rated capacity, that’s a symptom. To troubleshoot the problem, you need to know what kind of pump it is.
In the TapRooT® System, this troubleshooting is done in the Equifactor® Module of the TapRooT® Software.
Equifactor® Troubleshooting Process
You would use the Equifactor® Process below…

First, you would use the Equipment Troubleshooting Tables and identify the pump as a centrifugal pump. That’s an item of equipment (pump – centrifugal) in the Equifactor® Troubleshooting Tables outlined above.
For this failure, we would build a preliminary SnapCharT® that will hold the information we find. It might start off looking like this…

Next, we would open the applicable troubleshooting table for the symptom – insufficient capacity. It looks like the screenshot below…

Your job is to review the table and eliminate as many possible causes as possible.
For example, you could check to see if the suction strainer is clogged and eliminate that cause if it is clear.
Usually, you try to eliminate all the causes that don’t require the disassembly of the equipment. If disassembly becomes necessary, you need to develop a troubleshooting checklist to determine how you are going to eliminate causes while you perform the disassembly. Some things might require measurements during disassembly.
For example, in the case of a double volute (double suction) pump, the impeller may be installed backward. The mechanic would need to note this before the impeller is removed from the shaft.
The checklist you develop for this troubleshooting exercise might look like this…

That’s a summary of what troubleshooting is all about. If you haven’t finished troubleshooting, you aren’t ready for root cause analysis.
And that’s what we discovered. People were trying to find the root cause of why the pump wasn’t pumping at rated capacity before they knew that the impeller had been installed backward.
Once you do the troubleshooting and update your SnapCharT® (below), you are ready to identify Causal Factors and find root causes using the Root Cause Tree®.

In this example, the Causal Factor is that the mechanic had installed the impeller backward. This is analyzed using the Root Cause Tree® and isn’t an Equipment Failure after all. It is a Human Performance Difficulty.

Who Needs to Know What?
In the example above, the troubleshooting might have been performed by a mechanic or the mechanics supervisor. The root cause analysis might have been performed by the supervisor, the maintenance manager, or perhaps a reliability engineer.
Therefore, who should be trained in what?

All mechanics, mechanical supervisors, the maintenance manager, and the reliability engineer would be trained to perform troubleshooting using the Equifactor® Troubleshooting Tables.
Everyone could be trained to perform root cause analysis. Or you could just train those who will be performing the root cause analysis – the reliability engineer, the maintenance manager, and perhaps, the mechanical supervisors.
To teach people to do troubleshooting and root cause analysis takes two days. The course outline is below.
DAY ONE
- Introductions
- Understanding What Happened – SnapCharT® Basics
- SnapCharT® Exercise
- Collecting Information
- Failure Modes and Failure Agents
- Equifactor® Troubleshooting Tables
- Human Errors
- Process Troubleshooting
- Example: Troubleshooting a Seawater Pump
DAY TWO
- TapRooT®/Equifactor® Software Introduction
- Identifying Causal Factors
- Introduction to the Root Cause Tree®
- Exercise: Walking Through the Root Cause Tree®
- Exercise: Teams Find Root Causes Using the Root Cause Tree®
- Change Analysis
- Change Analysis Exercise
- Final Exercise: Solving a Major Equipment Issue
To teach people just troubleshooting requires just the first day of the two-day course outlined above.
Therefore, a facility with a large maintenance staff might hold a 2-Day Equifactor® Equipment Troubleshooting and TapRooT® ® Root Cause Analysis Course where certain people are selected to attend the whole course, and some are selected just to go to the first day (the troubleshooting day) of the course to save on course costs and people’s time.
Find Out More – Schedule a Course

Would you like to find out more about Equifactor® Training? See THIS LINK.
To see our upcoming public courses, see THIS LINK.
If you would like to sponsor a course at your site (or virtually), please contact us by calling 865-539-2139 or by CLICKING HERE.
Don’t wait. Equipment failures are expensive, and you want to troubleshoot them efficiently and effectively and then find out and fix the root causes. Equifactor® and TapRooT® are the way to get superior results.