What Should Your Company Be Doing to Prevent Major Accidents?
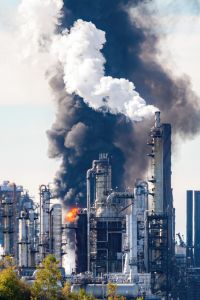
Major Accident Prevention
Is your company doing everything possible to prevent a major accident?
This article will explain three major initiatives that you should be using to prevent major accidents.
But first, what is a major accident?
Major Accident
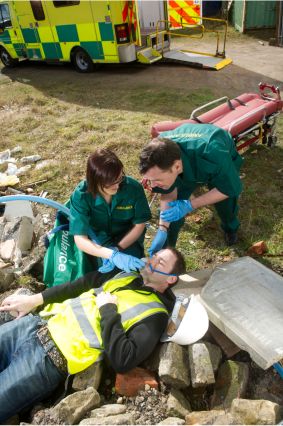
What is a major accident? Here are some examples to explain what is a major accident:
- First responders are called.
- The accident receives press coverage.
- Fatalities.
- Employees or members of the public have injuries that may cause a permanent loss of function.
- Releases of regulated pollutants in excess of regulatory guidelines.
- Accidents that cause a major financial loss (millions of dollars or more).
- A quality issue that receives negative press coverage.
- An incident that receives a regulatory response (on-site investigation by the regulator, a warning letter from the regulator, or a fine).
- A problem requiring notification of the CEO or discussion by the Board of Directors.
That’s not an all-inclusive list, but it should give you an idea of the types of problems we are trying to prevent. In some companies, these are things that get plant managers fired.
Three Major Initiatives to Prevent Major Accidents
There are many “programs” that people suggest to stop or reduce the likelihood of having a major accident at your company. I think that most of them would fit into one of these three categories:
- Learning from your experience (previous accidents and incidents).
- Proactive analysis of high-risk activities.
- Implementing best practices to prevent incidents and accidents.
Read on, and we will describe good examples of each of these initiatives.
Lessons Learned
A good lessons-learned program starts with identifying incidents that we should learn from, finding the incidents’ root causes, and developing effective corrective actions that will prevent future incidents.
Of course, if you have a major accident, that is one of the incidents that needs root cause analysis and effective corrective actions. But you also need to identify and investigate precursor incidents.
What is a precursor incident? Back in 2017, I was on a committee that was writing a book. They were trying to define what was a near-miss. I argued that we shouldn’t use the term near-miss and, instead, should refer to these types of problems as “precursor incidents.” I didn’t get the committee to change their terminology, but I did stop referring to near-misses.
So, what is a precursor incident? Here is the definition that I published in a previous article:
PRECURSOR INCIDENT
Minor incidents that could have been major accidents
if one or more Safeguards had failed.
Here is a video of a real-life example…
What can happen when you don’t effectively investigate and put in place effective fixes for precursor incidents? Here is an example…
How can you judge what “minor incidents” are “precursor incidents”? We wrote an article about that too. CLICK HERE to read it.
If you decide that an incident is a precursor incident, you need to perform an effective investigation with an advanced root cause analysis system that meets the fundamental requirements for a good root cause analysis. What are these fundamentals? They include:
- You need to understand what happened before you try to understand why it happened.
- You need to identify all the Causal Factors (not just one).
- You must dig deeper to understand all the Causal Factors’ root causes.
- You need a root cause system that guides you to the causes of equipment and human performance failures.
- You may need to go beyond root causes to identify generic causes.
- You need to develop effective fixes to prevent the recurrence of the Causal Factors/root causes.
- Management needs to understand your investigation and approve and support the changes necessary to ensure the implementation of the effective corrective actions that you recommend.
For more information about the fundamentals of root cause analysis, CLICK HERE.
So that is your first required initiative. Good root cause analysis of precursor incidents to prevent major accidents.
Proactive Prevention Programs
Becoming proactive means that you are looking for and fixing problems before they become incidents.
These programs include performing audits, observations, assessments, and even risk-based probabilistic safety assessments.
The simplest of these programs are management, supervisory, or peer field observations of tasks with high-risk potential.
What goes wrong with many of these observation programs?
- They aren’t well-planned and don’t look for problems that could cause major accidents.
- They don’t include effective root cause analysis of the “issues” that are identified during the observations.
- The observers don’t recommend effective improvements.
- The findings and recommendations don’t get much attention and, thus, nothing really changes.
What should a good proactive audit (observation) include? Think of the opposite of the list above.
By the way, we teach a 2-day course about auditing and proactive improvement for those that are interested. See THIS LINK.
Implement Best Practices
You might say that implementing the best practices that other companies or facilities have discovered may be the most proactive way to avoid major accidents. But where do you discover these best practices? We have several ideas.
First, in the TapRooT® Root Cause Analysis System, we have compiled best practices into the Corrective Action Helper® Guide/Software Module so that when you identify a root cause, it suggests potential best practices to apply to improve performance. It even provides references to learn more.

Here is an example of the suggestions provided in the Corrective Action Helper® Guide for the root cause “Labels Need Improvement.”

The guide also provides ideas to correct Generic Causes and References to learn more about correcting every root cause on the Root Cause Tree®.

Sometimes, even simple problems, like bad labels, need guidance so that investigators can recommend effective fixes.
Another way to learn effective best practices used by industry leaders is to attend the Global TapRooT® Summit. At the Summit there are many sessions designed to promote best practice sharing and success stories. Find out more about the Summit at THIS LINK. Or, watch this video…
We hope to meet you there.
Learn More About Advanced Root Cause Analysis
You might have noticed that effective, advanced root cause analysis is part of all three of these initiatives to prevent major accidents. Is it time for you to learn more about advanced root cause analysis? Then consider attending a 5-Day Advanced Root Cause Analysis Team Leader Course. Just click on the link to learn more. Here is a LINK to the dates and locations for our TapRooT® Training. And CLICK HERE if you would like to learn more about all of our TapRooT® Training.
Don’t wait to register. You need to start applying advanced root cause analysis NOW!