What is Root Cause Analysis?
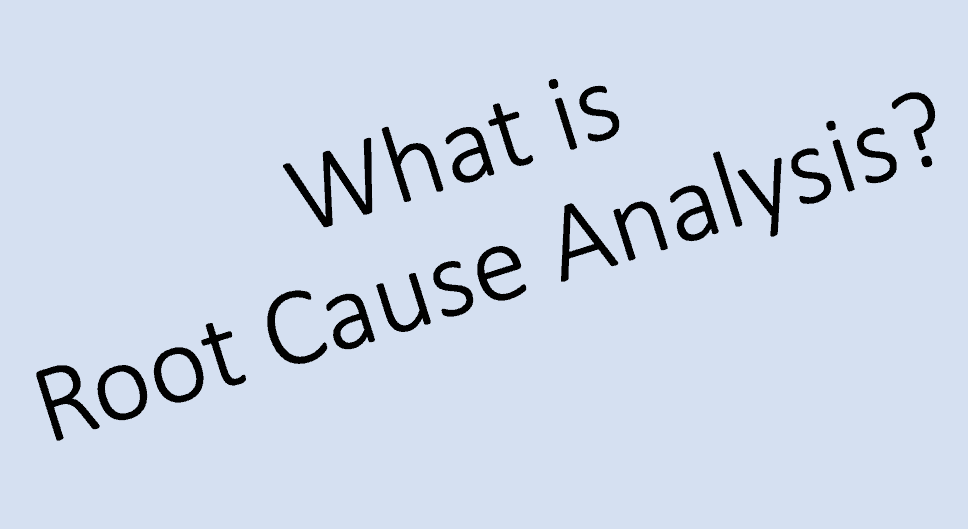
What is Root Cause Analysis?
What is a root cause analysis? Don’t jump to an answer quite yet. According to Thomas Wendell-Wedelsborg in an article in Harvard Business Review:
“In surveys of 106 C-suite executives who represented 91 private and public-sector companies in 17 countries, I found that a full 85% strongly agreed or agreed that their organizations were bad at problem diagnosis, and 87% strongly agreed or agreed that this flaw carried significant costs. Fewer than one in 10 said they were unaffected by the issue. The pattern is clear: Spurred by a penchant for action, managers tend to switch quickly into solution mode without checking whether they really understand the problem.”
If you agree that “problem diagnosis” is akin to root cause analysis, then, on average, 85% of companies don’t understand root cause analysis and that lack of understanding has significant costs for those companies.

Of course, finding a root cause (root cause analysis) depends on what you are looking for. And that depends on your definition of a root cause. So, the answer to “What is Root Cause Analysis?” starts with defining a root cause. And that’s where many companies go astray.
Let’s start with a dictionary definition of root cause from the Collins Dictionary:
“The fundamental reason for the occurrence of a problem.”
I think this type of definition leads many astray. Why? There isn’t an agreement on what is “fundamental.” For example, some may think that a “human error” is a fundamental reason for an occurrence. We’ve discussed this misunderstanding before HERE.
Here is another definition of “root cause” from the American Society for Quality:
The root cause is the core issue—the highest-level cause—that
sets in motion the entire cause-and-effect reaction that ultimately leads to the problem(s).
This definition doesn’t solve the problem of the previous definition. It just changes “fundamental” to “highest-level.” It also adds the idea that the root cause “sets in motion the entire cause-and-effect chain.” I’ve never liked the idea of an initial problem being the “root” – so this definition also leads investigators astray.
Even the definition that David Busch and Mark Paradies created in 1985 and published in 1986 had a similar problem:
ROOT CAUSE DEFINITION
The most basic cause (or causes)
that can reasonably be identified
that management has control to fix.
After all, how much different is “most basic” than the Collins Dictionary’s word “fundamental?” (See more about our early definitions HERE.)
However, by 2006 System Improvements created a new definition for a Root Cause:
ROOT CAUSE
A Root Cause is the absence of a best practice
or the failure to apply knowledge that would have prevented the problem.
This definition fits perfectly with the Root Cause Tree® Diagram, the TapRooT® System’s root cause analysis tool. The TapRooT® System leads investigators to find answers to prevent problems.
Thus, most companies have employees use a root cause tool that doesn’t lead investigators to identify the best practice they are missing or the knowledge they haven’t applied that allowed the problem to occur. Instead, they try the same old answers that haven’t worked before and expect a different result. (Isn’t that the definition of insanity?) And as Albert Einstien said:
“It’s impossible to solve significant problems
using the same level of knowledge that created them.”

Thus the definition of Root Cause Analysis is:
ROOT CAUSE ANALYSIS
“The process of finding the missing best practices
or knowledge needed to prevent a problem.”
That definition seems simple, but, as Admiral Rickover said, “The devil is in the details.”

That’s why the TapRooT® System for root cause analysis is so unique. The folks at System Improvements figured out how to lead investigators beyond their current knowledge to best practices and knowledge they previously didn’t consider. This is especially important when trying to solve problems caused by human errors.
The REAL Definition of Root Cause Analysis
The TapRooT® System for Root Cause Analysis leads problem solvers to solutions based on identifying fixable root causes. It is a guided root cause system that helps people solve human performance and equipment reliability problems. Over the past 37 years, the staff at System Improvements has developed and improved the system to make it an international best practice for root cause analysis.
Why does TapRooT® Root Cause Analysis solve the problems many executives believe cost their companies money? Quite simply, it meets all the requirements of the fundamentals of root cause analysis. It’s an expert system that guides problem solvers in their investigation, root cause analysis, and development of effective corrective actions.
Thus, the expert systems in the TapRooT® System consistently lead investigators to root causes and corrective actions that introduce knowledge and best practices needed to stop problems.
The TapRooT® System is the REAL definition of Root Cause Analysis.
The TapRooT® Root Cause Analysis System
TapRooT® Root Cause Analysis System has two processes: a simple process for incident root cause analysis (precursor incidents) and a more complete process for major investigation root cause analysis (major accidents with high consequences).
The first process for simple incidents (low-to-moderate risk) is shown below…

One important part of this simple root cause analysis process is that it uses all the essential TapRooT® Tools and provides investigators with a way to save time and effort if they find, early on, that there is nothing to be learned from further investigation. Once they have the initial information on their SnapCharT® Diagram, they can STOP the investigation if they decide there is nothing significant to learn.
What is the process for major investigations? It is shown below…

This root cause analysis process for a major accident has all the TapRooT® Tools (essential and optional) and even looks for Generic Causes.
How Does TapRooT® Root Cause Analysis Work?
What TapRooT® Tools make these processes work (and so special)? These four tools provide a basis for advanced root cause analysis…
- The SnapCharT® Diagram
- The Equifactor® Troubleshooting Tables
- The Root Cause Tree® Diagram and Dictionary
- The Corrective Action Helper® Guide/Module
The SnapCharT® Diagram helps you collect and organize information to help you understand what happened.
The Equifactor® Troubleshooting Tables help you understand what happened to cause equipment failures.
The Root Cause Tree® Diagram, which includes the Human Performance Troubleshooting Guide, guides you to the root causes of human performance and equipment reliability issues.

The Corrective Action Helper® Guide/Module helps you develop effective fixes based on research (knowledge) and best practices from around the world.

These tools, plus the optional TapRooT® Techniques, are included in the patented TapRooT® Software.
Of course, that’s just the start of what makes the TapRooT® Root Cause Analysis System an international best practice.
Click on the picture below to download a white paper that describes the TapRooT® Root Cause Analysis System in more detail and provides an example of an environmental incident root cause analysis.

Now is the Time To Learn More About REAL Root Cause Analysis!
To learn how to investigate precursor incidents and major accidents, attend our 5-Day TapRooT® Advanced Root Cause Analysis Team Leader Training. See the dates and locations of upcoming public 5-Day Courses being held around the world by CLICKING HERE.
Want to hold a root cause analysis course at your site? Contact us by CLICKING HERE. Then have your whole staff learn, “What is root cause analysis?” and how to use the best root cause analysis – TapRooT® Root Cause Analysis – to find and fix the real root causes of accidents, precursor incidents, quality issues, equipment failures, maintenance problems, cost overruns, and operational issues.

If you would like to discuss what makes TapRooT® Root Cause Analysis so unique, get a demo of the TapRooT® Software, and learn how your site can implement TapRooT® RCA to improve performance, CLICK HERE to contact us or call one of our TapRooT® Implementation Advisors at 865-539-2139.