What Happens When a Flight Crew Faces a Non-Normal Situation?
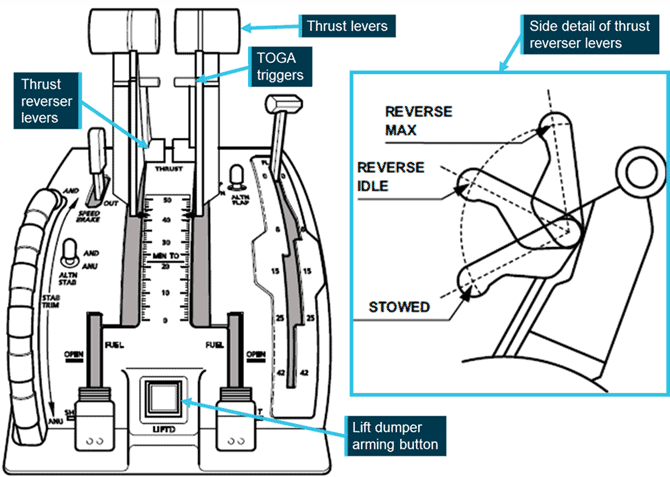
Uncommanded TOGA mode activation shows how flight crews can be faced with non-normal situations.
The unplanned activation of TOGA (take-off/go-around) mode during the landing of a Fokker F100 highlights that flight crews can be faced with non-normal situations that require good judgement and expertise to safely manage, according to an Australian Transport Safety Bureau (ATSB) investigation into the incident.
On September 1, 2020, Virgin Australia Regional Airlines Fokker F100 VH-FNR was landing at West Angelas aerodrome in Western Australia’s Pilbara region, on a scheduled passenger service from Perth — faced with a non-normal situation.
Just prior to touching down, the aircraft’s take-off/go-around mode activated, preventing automatic deployment of the lift dumpers to slow the landing roll.
The flight crew reported that, after touching down right wheel first, they selected the engine thrust reverser levers to the idle position
However, they did not deploy. The thrust reversers were selected a second time, but again they did not deploy.
The first officer then moved the levers beyond reverse idle and applied manual braking, at which point both thrust reversers and lift dumpers deployed. The landing then proceeded as normal.
After the landing, the captain observed on the primary flight display that the go-around (GA) flight mode was active. The multi-function display unit also indicated the TOGA thrust mode.
The ATSB’s investigation into the event concluded that the TOGA mode activated for an unexplained reason, preventing automatic activation of the lift dumpers
In addition, the weight on wheels sensors gave an intermittent signal during landing. This was most likely due to a softer than typical landing, combined with the lift-dumpers not automatically deploying due to the TOGA mode being activated.
The intermittent weight on wheels signal delayed the manual activation of the lift dumpers and deployment of reverse thrust.
“Despite the high reliability of modern flight control systems, this event highlights that flight crews can still be faced with non-normal situations that require their combined judgement and expertise to safely manage,” said ATSB Director Transport Safety Dr. Stuart Godley.
“Delayed deployment of reverse thrust, lift dumpers, or a combination of the two, has contributed to runway overruns in the past.”
Under normal operation, the F100’s TOGA mode is selected by pulling two triggers located on the thrust levers. The flight crew reported the motion to actuate the triggers would be an intentional one, and they did not believe it could happen accidentally.
After the incident, maintenance engineers tested the TOGA switches, weight on wheels sensors, lift dumpers, thrust reversers, flight computers and auto-throttle systems. No anomaly or unserviceability was found.
The aircraft was then returned to service, and at the time of publication there had been no reoccurrences of inadvertent TOGA mode activations.
This Lesson Learned is from an Australian Transport Safety Bureau investigation report release. Read the final ATSB report.
Do you have a story to share about the failure of critical equipment?
We’d like to hear from you about what happened. What was the response? The sequence of actions? Feel free to comment on this blog post.
The best root cause analysis leads to effective corrective actions
The TapRooT® System teaches you to be a very effective problem-solver. The System is a process with techniques to investigate, analyze, and develop corrective actions to solve problems. The TapRooT® process and tools are completely described in the TapRooT® Investigation Essentials Book Set.
Safety and Quality experts already know that a TapRooT® Root Cause Analysis (RCA) is the best option to get human-performance-based root causes. It is the only system that uses scientifically derived root causes to eliminate bias and avoid blame.
What they don’t know is that the Equifactor® Equipment Troubleshooting Module should be used whenever there is an equipment failure. Use Equifactor® anytime an equipment failure is involved in your investigation. It’s a great way to make sure you are fully covering all the possible errors and failures during your TapRooT® RCA analysis.
Fix your equipment problems with Equifactor®
Attend one of our 2-Day TapRooT® Equifactor® courses. These courses are designed to teach your equipment experts how to use both TapRooT® and the Equifactor® module during their investigations. You can register for one of these courses here.
We are available to train you and your staff on-site at your workplace; reach out here to discuss your needs. Call us at 865.539.2139 for any questions you may have. We are here to help you.