Three Common Incident Investigation Mistakes
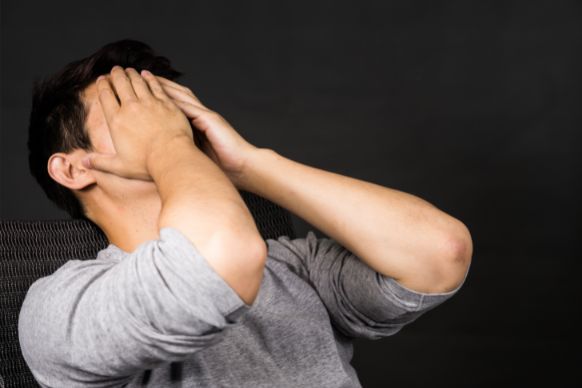
Cost of Three Common Mistakes
Before we discuss the three common incident investigation mistakes, let’s consider why it is crucial to avoid them.
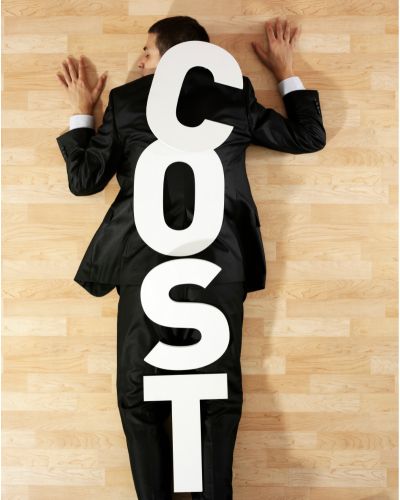
What does it cost if you make mistakes during an incident investigation?
- You waste your time.
- You look bad in front of management if they spot the error.
- If no one spots the error, you waste effort and money implementing fixes that don’t fix the problem.
- A poor investigation that doesn’t fix the problem may lead to a more serious and expensive accident in the future.
None of these outcomes are positive. Some may be extremely expensive for your company and your career.
Therefore, we can agree that avoiding incident investigation mistakes is essential. Thus, the three common investigation mistakes are critical to recognize and avoid.
Three Common Incident Investigation Mistakes
What are the three most common incident investigation mistakes I’ve observed over a 35-year+ career investigating incidents, developing incident investigation systems, and teaching others to investigate incidents? They are:
- Jumping to Conclusions
- Looking for Familiar Causes
- Same Old Corrective Actions
Let’s look at these mistakes and discuss how to avoid them.
Jumping to Conclusions
I had a boss who always knew what “caused” a problem because he had:
“Seen it before.”
And this common mistake isn’t rare. It is the basis for the philosophy of Cause and Effect. So if Socrates, Aristotle, and Plato made this mistake (they invented the concept of cause and effect), you shouldn’t feel bad if you say, “I’ve seen this before,” without investigating adequately.
Here is the simplest explanation of Cause and Effect that I’ve ever seen:
Some techniques promote jumping to conclusions. I already mentioned Cause and Effect, but other common techniques based on Cause and Effect including 5-Whys and Why Trees.
And, of course, sometimes you may be right when you jump to a conclusion.
And jumping to conclusions when you’ve “seen it before” saves time. You don’t waste time collecting evidence because you already know the answer. But do you really know the answer?
Why is jumping to conclusions a problem? Because what you think is the cause of an effect may not be the cause of an effect.
For example, if you have seen a car accident caused by a drunk driver, does that mean that drunk drivers cause all car accidents? Of course not. There can be many potential causes of car accidents. The question is, do you know all the causes? And if you don’t know all the causes, can you find causes you don’t know?
Without a thorough investigation, you won’t know the real cause. Jumping to conclusions is a shortcut that may save you time but may also cause you to jump to the wrong conclusion.
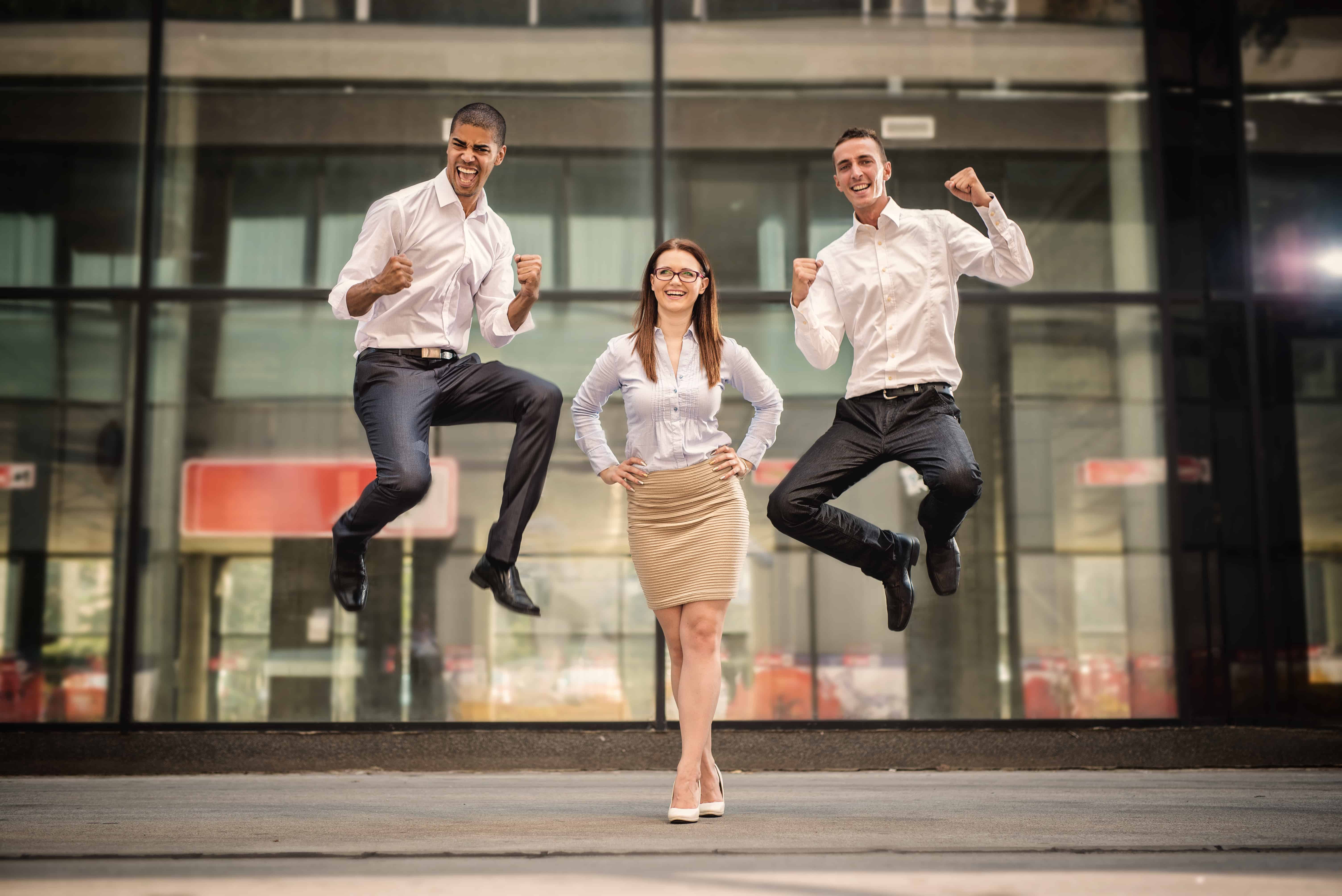
This problem of jumping to conclusions without knowledge leads to the second common mistake.
Looking for Familiar Causes
The second common incident investigation mistake is looking for causes you understand or have heard before. These causes are familiar. You might recall this common saying:
“If the only tool you have is a hammer,
it is tempting to treat everything as if it were a nail.”
Abraham Maslow (1966)
Thus, looking for familiar causes may lead to finding the “same old causes” during every investigation. Looking for familiar causes is especially problematic when investigating incidents caused by human error.
At the start of our 5-Day TapRooT® Advanced Root Cause Analysis Team Leader Training, I would ask the students how many had any human factors (the causes of human error) training. Sometimes, none had previous training. Sometimes, one or two out of a class of 30 would have had human factors training. I would then ask how many of the students had been asked previously to investigate an incident that included a human error. Almost everyone would raise their hand.
How were these students finding the causes of human errors when they didn’t have any training in the causes of human errors? In most cases, they didn’t find the causes of human errors. Instead, they stopped at human error as the cause and applied one of their standard corrective actions.
This type of mistake is not only made by incident investigators; it is also made by scientists. It is called confirmation bias. Read more about confirmation bias HERE.

This common incident investigation mistake – looking for familiar causes – leads to the third common mistake.
Same Old Corrective Actions
Early in my study of root cause analysis and incident investigation, I learned that people had a proclivity to choose one of three standard corrective actions:
- Discipline. This starts with the common corrective action: “Counsel the employee to be more careful when …”.
- Training. This may be the most used (and misused) corrective action.
- Procedures. If you don’t have one, write one. If you already have one, make it longer.
Do these three appear frequently in your company’s incident investigation corrective actions? Then you, too, may have the same old corrective action problem.
I was reviewing the reports at one company and found that they had repeat incidents. Incidents that happened over and over again. When I looked at the reports in more detail, I discovered that the corrective actions in the reports were almost identical.
This reminded me of the definition of insanity…
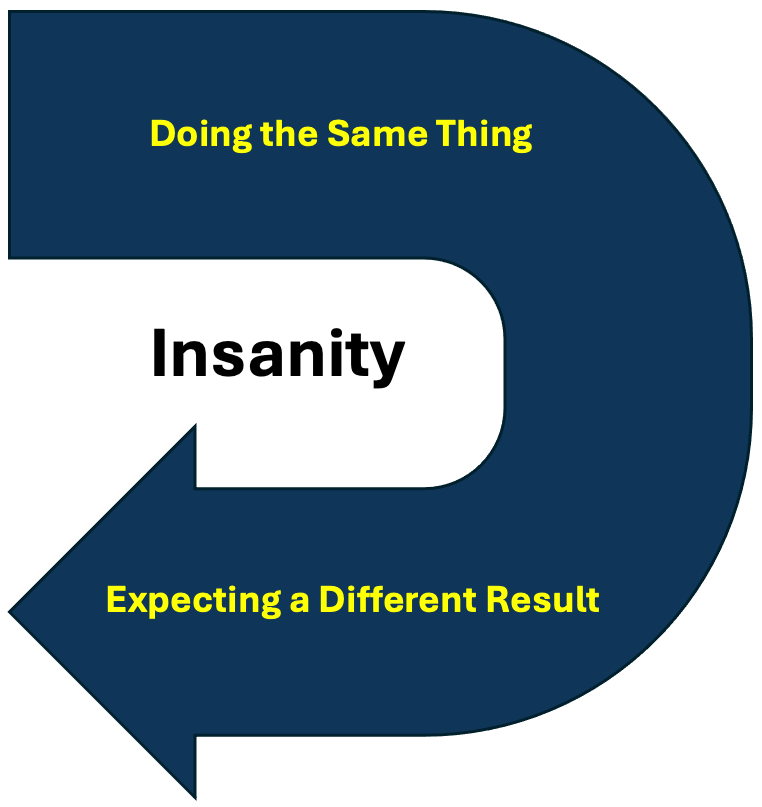
I talked to one of the investigators. When I asked him why I saw the same old corrective actions over and over again, he said:
“If management approved the corrective actions last time,
they probably will approve them again.”
He saw his job as getting corrective actions approved by management. He didn’t see his job as correcting problems.
Fixing the Three Common Incident Investigation Mistakes
You can’t fix the three common incident investigation problems by telling people to work harder or be smarter. You need to address the root causes of these three common problems.
First, you need to ensure that your investigators gather the facts BEFORE they start looking for causes.
Second, you must give your investigators a tool to help them go beyond their current knowledge, especially when investigating human performance/human error issues.
Third, you need to give your investigators a tool (or tools) to help them develop effective corrective actions.
TapRooT® Root Cause Analysis Solves the Three Common Incident Investigation Problems
First, the TapRooT® System guides investigators through the investigation process.

Simple TapRooT® Investigation Process
It starts with a tool to gather and organize the information investigators collected. That tool is called a SnapCharT® Diagram.
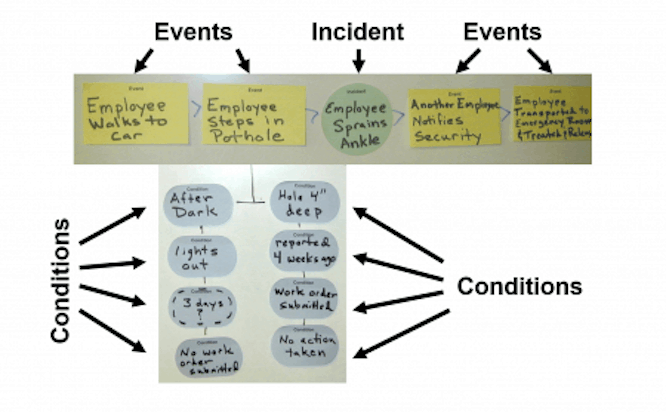
Note that information collection starts before looking for root causes. Thus, you understand what happened before tring to understand why it happened. This helps solve the problem of jumping to conclusions.
Second, the TapRooT® System includes the Root Cause Tree® Diagram.
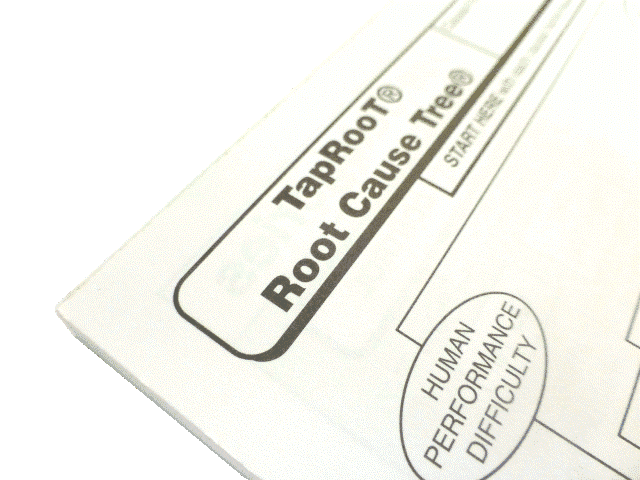
The Root Cause Tree® Diagram is an expert system (AI for root cause analysis) that guides investigators beyond their current knowledge to find the root causes of human performance and equipment issues.
This assistance helps solve the problem of only finding root causes that the investigator is familiar with.
Third, The TapRooT® System helps investigators go beyond the same old corrective actions by using the Corrective Action Helper® Guide/Software Module.
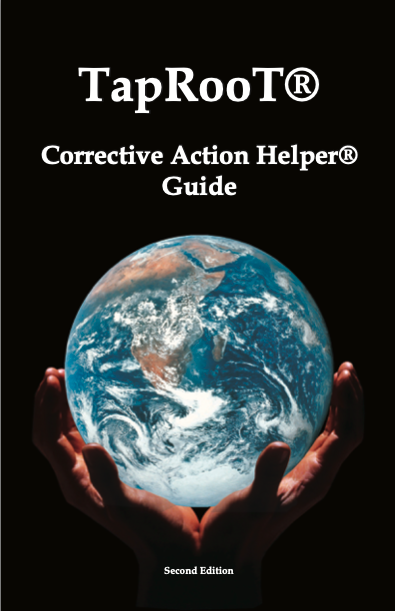
The guide suggests corrective actions for every root cause on the Root Cause Tree® Diagram, improving the investigator’s creativity. It also provides ideas to solve generic causes (programmatic issues).
Find out more About TapRooT® RCA
Where can you learn more about TapRooT® Root Cause Analysis and how it can help improve incident investigations? First, see this WHITE PAPER.
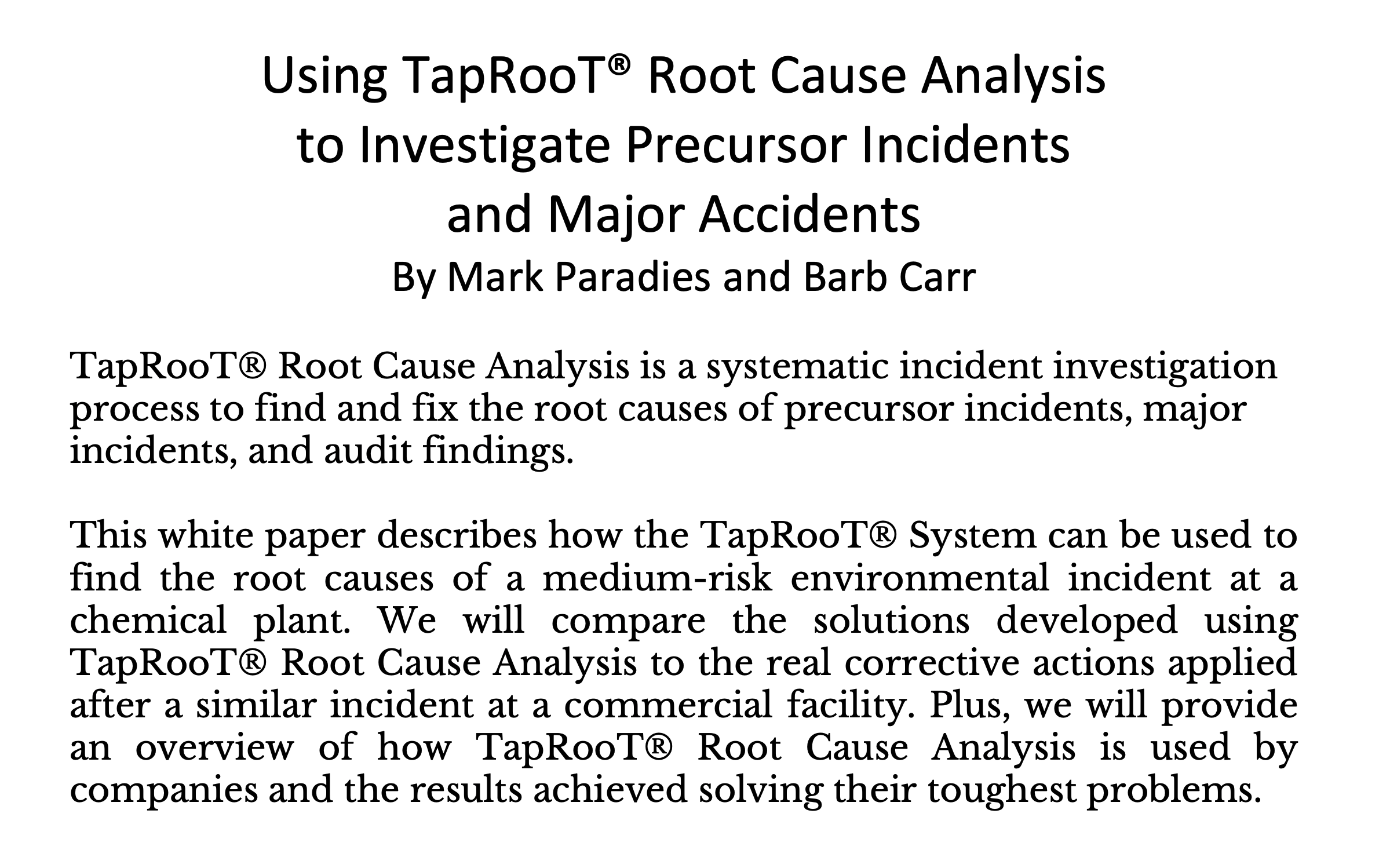
However, the best way to learn advanced root cause analysis – TapRooT® Root Cause Analysis – is to attend one of our courses. See the course descriptions HERE.
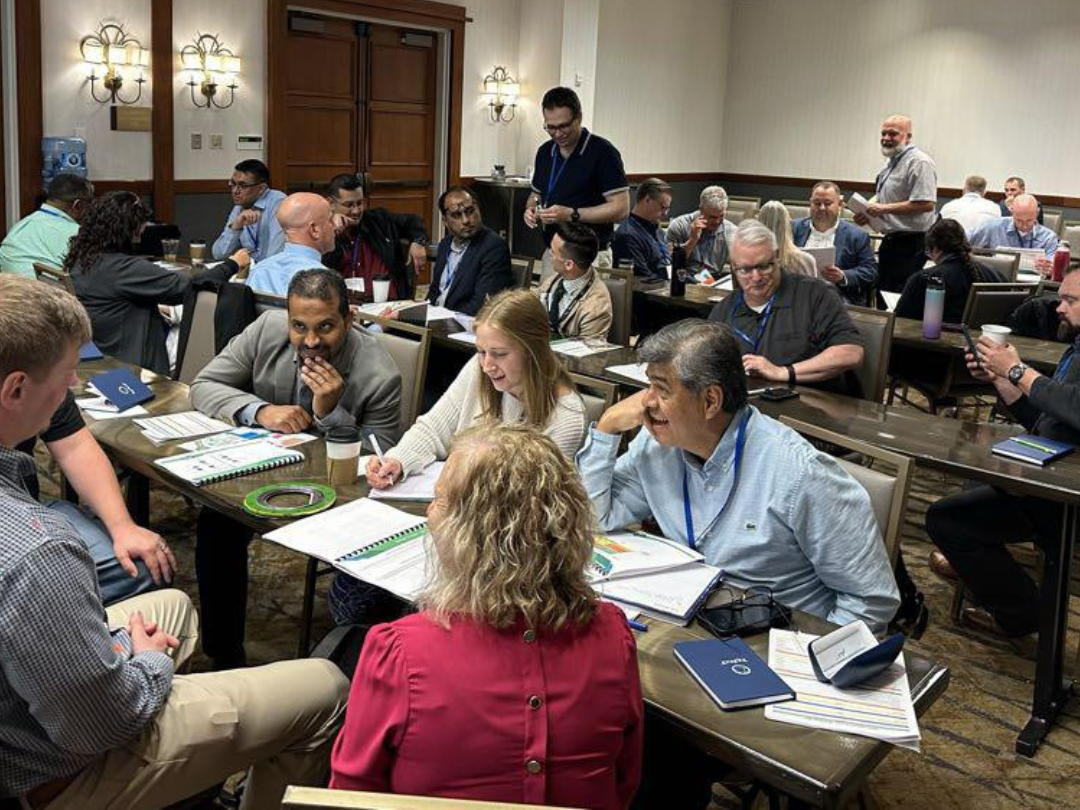
See our upcoming public TapRooT® Course dates and locations HERE.
BONUS: Don’t Investigate Things That Don’t Need Investigating
Another incident investigation mistake I’ve observed is people wasting time investigating incidents that should never have been investigated. Incidents that didn’t provide an opportunity to learn something of value. I call these:
Paper Cut Incidents
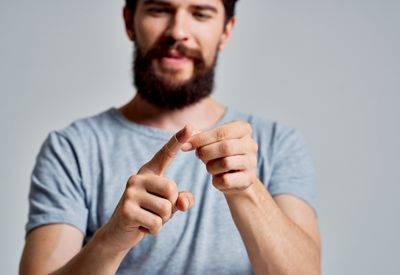
They have no significant consequences, and they are NOT precursor incidents.
Therefore, the costs of investigating these types of incidents are not worth the benefits.
Why would an investigator spend their time investigating this type of incident? Because management made a policy that required it. For example, management might say every medical treatment case requires a root cause analysis. They want to prevent major accidents by learning from minor incidents, but not every minor incident can cause a major accident. Your investigation system/policy needs a way to stop the investigation if there is nothing significant to learn. The TapRooT® System has that way out.
Also, your management must understand the value of investigating and correcting precursor incidents to assign adequate resources to these investigations.
Where can your management learn about root cause analysis, the resources needed for reasonable investigations, and their role in incident investigations and root cause analysis? In a TapRooT® Executive Leadership’s Role in Root Cause Analysis Course. Find out more about this training HERE.