The Missing Component of TPM – Effective Root Cause Analysis

What is TPM?
Before we talk about the missing component of TPM (root cause analysis), here is a brief overview of TPM (Total Productive Maintenance).
TPM was developed in the 1960s and provided a holistic approach to improve equipment performance including:
- preventing breakdowns
- reducing defects
- operating equipment effectively/efficiently
Click on the image below for an article about TPM.

It was often implemented as part of a Lean Manufacturing process.
Watch this one-hour YouTube video (a slide from the video is the intro picture to this article) to learn more about TPM and Lean…
What is Missing from TPM?
I can’t say that effective root cause analysis is missing from every TPM implementation, but I know it is missing from many. How do I know? Easy. If you say your program uses:
for root cause analysis of problems, then I know you have ineffective root cause analysis. Just click on the links above to see why those common techniques are ineffective.
To have an excellent TPM implementation, you need effective root cause analysis to help you solve the problems that are uncovered in a TPM program.
How To FIX What is Missing
First, if you are still having trouble understanding what is wrong with a common technique like 5-Whys, read this article:
So what is missing from many TPA implementations? Advanced root cause analysis. And what is advanced root cause analysis? The TapRooT® System.
The article above explains TapRooT® RCA and should give you ideas on why it is advanced and outperforms common techniques. Ideas that include:
- Understanding what happened BEFORE you start trying to find why it happened (and a tool – the SnapCharT® Diagram – to help you do this).
- Guidance to troubleshoot equipment problems (the Equifactor® Troubleshooting Tables).
- Guidance to analyze the #1 cause of equipment problems – human error.
- Guidance to develop effective corrective actions.
- Comprehensive, guaranteed training to understand how to use advanced root cause analysis.
Learn Advanced Root Cause Analysis for Improved TPM
Where can you learn about advanced root cause analysis including using the Equifactor® Troubleshooting Tables and the TapRooT® Root Cause Tree? In our 2-Day Equifactor® Equipment Troubleshooting & TapRooT® Root Cause Analysis Training or the 5-Day TapRooT® Advanced Root Cause Analysis Team Leader Training.
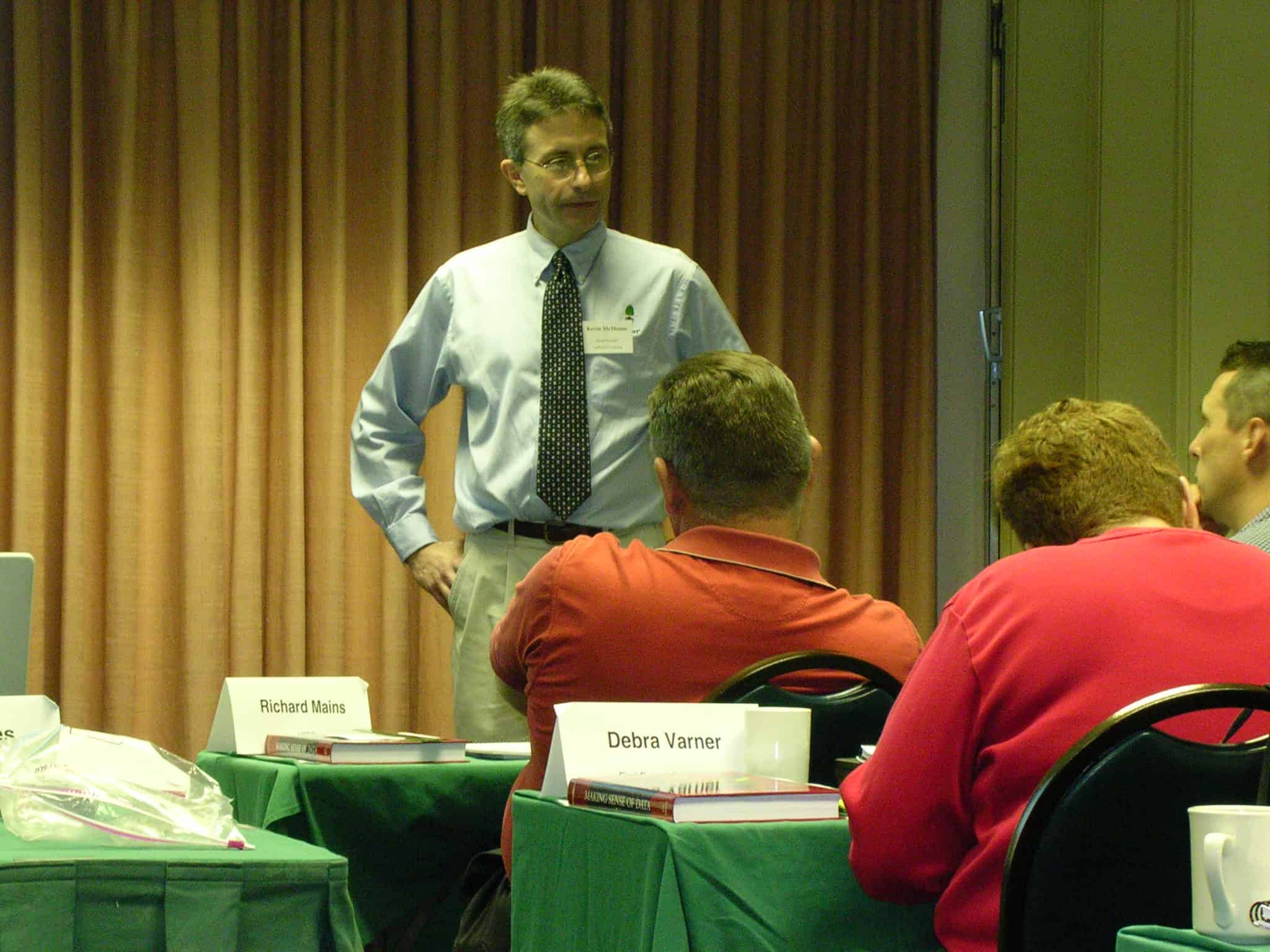