TapRooT® Techniques Contribute to Evolution of Improved Safety, Environment, and Policies
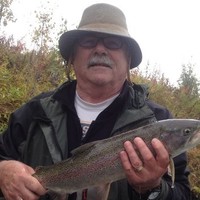
A TapRooT® Success Story from Mike Rodriguez, Exploration, Drilling, and Wells Safety Specialist, ConocoPhillips Alaska, Inc.
In the beginning…
We started using TapRooT® in the mid-1990s after one of our supervisors wanted to instill a more formal process to our investigations. Since then our RCA has been structured around the 7 steps of TapRooT® System. This evolution for us has helped us create an incident investigation committee and more comprehensive training among management that we continue to build on each year.
TapRooT® is a thinking tool
From our experiences, TapRooT® RCA is a wonderful “thinking” tool. The more we expose more employees to it, the more employees understand the importance of our key findings, and more employees appreciate the impact corrective actions can have on all of us. All of this leads to better communication among our teams of employees.
Measurable accountable successes
One of our most visible points of success as a division is our lower TRIR in recent years. Our TRIR used to be in the 4-5 range, and I am proud to say it has been reduced to below 1. HSE changes combined with more proactive use of TapRooT® tools and techniques and the resulting key findings have contributed to this improvement.
It’s all about an evolution
Using TapRooT® RCA certainly helps improve each and every investigation we conduct. However, it goes way beyond that for a company to derive the greatest benefits from implementing TapRooT® Root Cause Analysis. If we simply took the findings and filed them away, who would they help? Corporate culture ultimately changes as a result of the TapRooT® investigations and the corrective actions. This information – the key findings – empowers management to instill even stronger communications, policies, and safety environments in the workplace. I am invigorated knowing that the information we uncover will lead to even better health and safety standards for our employees. We are no longer afraid to ask ourselves, “What is it about our organization that contributed to the failure.” We learn, adjust, and evolve in order to eliminate issues and incidents as well as to continually improve our workplace.
Via TapRooT® RCA, we learn from even minor incidents
We had an employee in the field close a truck door on his hand, causing injury to himself. This was a medical treatment incident; protocol required us to institute an investigation. Our response might have been:
- was the employee distracted,
- was the employee multitasking and not paying attention,
- was it simply human error,
- was the employee not wearing safety gear (gloves), etc?
While all of these questions are critical to the process, we knew we couldn’t stop there. One of TapRooT®’s highest attributes is its ability to help us drive important questions to show intention versus activation in a policy and/or incident. What we learned was critical to field and safety ops for all employees. From this incident and our TapRooT® process we learned that an important communiqué has been omitted from the protocol/policy distributed to employees. We also learned that field operations and company policymakers must work even closer together before policies are distributed in order to take into account a broad range of scenarios and real-world applications. With TapRooT® RCA, our investigations are more forthcoming and revealing than in years past. It comes with knowledge and technology. We are getting better every day.
For me it has been rewarding to see the important changes we can make in our safety policies from even a minor incident. Key findings are uncovered, implemented and shared. The sharing of best practices and policies is a maximum benefit for everyone. This really energizes me because our safety team knows we can be on the cutting edge for the company.
Safety comes first
Success has to be defined within the business we’re in. We want to complete the job on time or under budget and safely. Safety always goes to the front if needed. We don’t compromise on safety for the sake of schedule, time, or money. They are always equal values in stature, but safety comes first, and TapRooT® helps us continually improve and evolve in this area.