Book 2: TapRooT® Root Cause Analysis Implementation
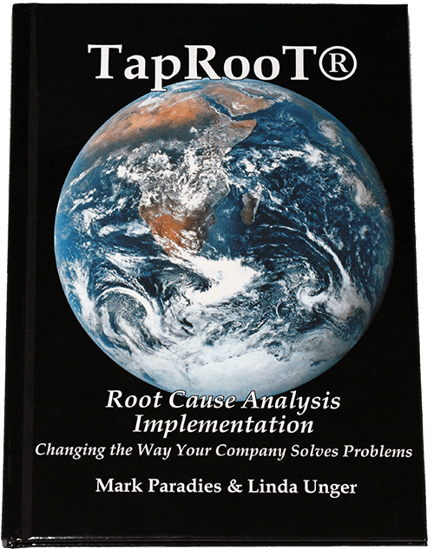
Book 2: TapRooT® Root Cause Analysis Implementation
• • •
Book two of the ten-book series outlining how to implement TapRooT® Root Cause Analysis to improve performance is for leaders who want to implement a world-class improvement program. The book, TapRooT® Root Cause Analysis Implementation, is the guidance that management needs to develop a roadmap to successful TapRooT® implementation and a performance improvement program that can stop fatalities, reduce injuries, improve quality, reduce equipment reliability issues, and find and fix the root causes of all sorts of operational issues.
TapRooT® Root Cause Analysis is an excellent systematic process for finding the root causes of accidents, incidents, quality issues, patient safety events, equipment reliability issues, and operations difficulties. You can achieve maximum results using TapRooT® by carefully planning and continuously improving the implementation of your performance improvement program.
This book can be used as a checklist to evaluate and improve your improvement program. The book provides the best practices that we have observed in world-class improvement programs. Apply the best practices to develop an initial TapRooT® based improvement initiative or use the best practices to improve your already existing performance improvement program. These best practices will help your people save time and perform more effective root cause analysis.
In just 95 pages, the book brings a focus to TapRooT® implementation and new best practices that weren’t available in the three previous TapRooT® Books (all three books shown below – the 3-ring binders published in 1991-1996, the green book published in 2000, and the black book published in 2008).
The new book, pictured below, was written by Mark Paradies and Linda Unger.
Mark Paradies has 42 years of experience in high-reliability organizations, process safety, incident investigation, and root cause analysis. His career started as a leader in Admiral Rickover’s Nuclear Navy (where he earned Engineer Qualification). He also worked for DuPont in the areas of human factors, process safety, and performance improvement management before he started System Improvements in 1988. He has a BS in Electrical Engineering and an MS in Nuclear Engineering (with an emphasis on human factors), both from the University of Illinois.
Linda Unger has 36 years of experience in engineering, process safety oversight, incident investigation, and root cause analysis system implementation. She started her career at DuPont in an engineering group that also performed process safety oversight and incident investigation. She joined System Improvements in 1990 where she helped create the TapRooT® System. She has a BS in Electrical Engineering from the University of Tennessee and human factors training from the University of Michigan.
Chapters
The three chapters and two appendices in the book include:
- Just Do It!
- Adding TapRooT® to an Existing Improvement Program
- Building a Best-In-Class TapRooT® Performance Improvement Program
- Appendix A: A Sample Problem Reporting and Root Cause Analysis Guide
- Appendix B: Incident Reporting Form
The book continues on from Book 1: TapRooT® Root Cause Analysis Leadership Lessons and explains what someone leading an improvement program needs to do to achieve success.
Chapter 1: Just Do It!
Teddy Roosevelt said:
Do what you can, with what you have, where you are.
That’s the focus of Chapter 1, getting started the fastest way possible by attending a 5-Day Advanced Root Cause Analysis Team Leader Course.
Chapter 2: Adding TapRooT® to an Existing Improvement Program
What types of existing improvement programs are we talking about?
- ISO Programs
- Process Safety Management
- Patient Safety Improvement
- Lean
- Six Sigma
- Operational Excellence
- Total Productivity Management
- Reliability Centered Maintenance
- Behavior-Based Safety
- Human Performance
All of these improvement programs require root cause analysis. Many start with basic techniques like:
- 5-Whys
- Brainstorming
- Fishbone Diagrams
- Cause and Effect
- Fault Trees
30+ years ago, these techniques were a start for those who had no knowledge of root cause analysis. But today, these techniques are known not to arrive at effective fixes.
This chapter explains how you can replace these ineffective techniques with advanced root cause analysis.
Chapter 3: Building a Best-In-Class TapRooT® Performance Improvement Program
This chapter is the heart of this book and provides a checklist to develop a best-in-class improvement program based on best practices from TapRooT® Users from around the world.
It starts with an improvement program checklist…

Copyrighted material used here by permission of System Improvements, Inc.
The chapter goes on to detail each of the fifteen items outlined above. This helps you plan your roadmap to success. (Contact us at 865-539-2139 about help developing your roadmap.)
Appendix A: A Sample Problem Reporting and Root Cause Analysis Guide
Do you need a standard incident report format or are you developing an investigation policy? This section gets you started. Once again, we have taken the best practices from around the world and distilled them into a sample report and policy.
Appendix B: Incident Reporting Form
Need a form for an initial report of an incident. This appendix provides a sample based on the best practices that we’ve seen.
Complete 10 Book Set
Now that we have completed the ten-book set, you can order all 10 books and SAVE by clicking HERE. If you just want Book 2, order it by CLICKING HERE.