Stop Normalization of Deviation with Normalization of Excellence
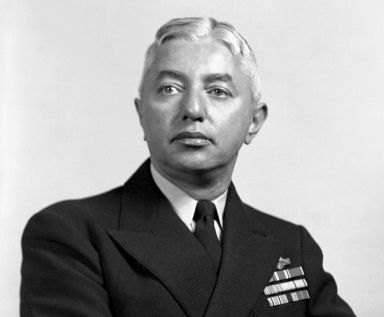
No Such Thing
There is no Normalization of Deviation. Deviation IS NORMAL!
If you don’t think that is true, read this previous article…
Naval Reactors Creates the First High-Reliability Organization
In 1946, Admiral Rickover was one of a small group of naval officers that visited the Manhattan Project in Oak Ridge, Tennessee, to learn about nuclear power and to see if there were ways to apply it in the US Navy. He had the foresight to see that it could be applied as propulsion for submarines – freeing subs from the risky proposition of having to surface to recharge their batteries.

But even more amazing than his ability to see how nuclear power could be used, to form a team with exceptional technical skills, and to research and develop the complex technologies that made this possible … he saw that the normal ways that the Navy and industrial contractors did things (their management systems) were not robust enough to handle the risk of nuclear technology.
Rickover set out to develop the technology to power a ship with the atom and to develop the management systems that would assure excellence. In Ph.D. research circles, these new ways of managing are often called a “high-performance or high-reliability organization.”
Rickover’s pursuit of excellence was not without cost. It made him the pariah in naval leadership. Despite his accomplishments, Rickover would have been forced out of the Navy if it had not been for strident support from key members of Congress.
Why was Rickover an outcast? Because he would not compromise over nuclear safety and his management philosophies were directly opposed to the standard techniques used throughout the Navy (and most industrial companies).
What is the proof that his high-performance management systems work? Over 60 years of operating hundreds of naval nuclear reactors ashore and at sea without a single reactor (process) safety accident (reactor meltdown). And his legacy continues even after he left as head of the Nuclear Navy. The culture he established is so strong that it has endured for 30 years!
Compare that record to the civilian nuclear power industry, refinery process safety incidents, or off-shore drilling. All have seen major accidents. You will see that Rickover developed a truly different high-reliability organization that many with Ph.D.s still don’t understand.
In his organization, deviation truly was abnormal.
What are the secrets that Rickover applied to achieve excellence? They aren’t secret. He testified to his methods in front of Congress, and his testimony is available at this link:
https://www.taproot.com/content/wp-content/uploads/2010/09/RickoverCongressionalTestimony.pdf
What keeps other industries from adopting Rickover’s management systems to achieve equally outstanding performance in their industries? The systems Rickover used to achieve excellence are outside the experience of most senior executives, and applying the management systems REQUIRES focussed persistence from the highest levels of management.
To STOP the normalization of deviation, the CEO and Presidents of major corporations would have to insist on and promote the Normalization of Excellence that is outlined in Rickover’s testimony to Congress.
Sometimes Rickover’s testimony to Congress may not be clear to someone who has not experienced life in the Nuclear Navy. Therefore, I will explain (translate from Nuclear Navy terminology) what Rickover meant and provide readers with examples from my Nuclear Navy career and from other industries.
Read Part 3: Normalization of Excellence – The Rickover Legacy – Technical Competency