KISS & Root Cause Analysis
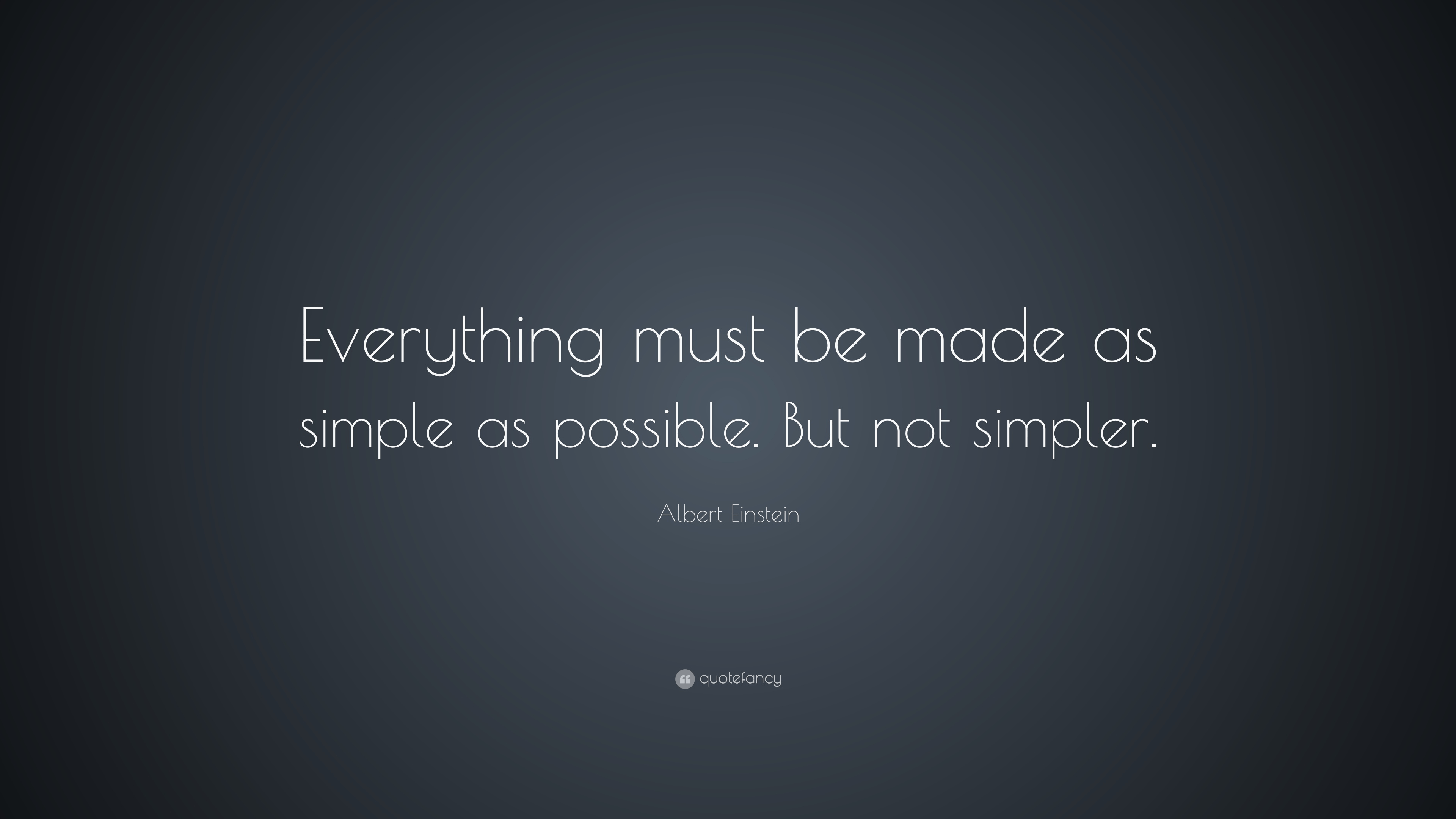
What is KISS?
That’s easy…
Keep It Simple, Stupid!
But how does KISS apply to root cause analysis?
If you listen to many experts, you need a simple root cause analysis system. Otherwise, people in the field won’t be able to use it. (This philosophy seems insulting to people in the field.)
However, you need to listen to Albert Einstein when it comes to making something simple.

Einstein says:
Everything must be made as simple as possible.
But not simpler.
Some Simple Ideas That Are Wrong
I’ve heard people profess the following ideas to “keep root cause analysis simple.”
- It’s a waste of time to use full root cause analysis on every problem.
- People can’t understand complex root cause analysis techniques.
- Learning simple techniques will get people to start thinking more deeply about problems.
- Simple techniques are just about as good as those fancy techniques.
- Managers don’t have time to do fancy root cause analysis, and they already know what is wrong.
- You can apply those complicated techniques to just the most serious accidents.
- The data from the simple investigations will help you identify the more complex issues you need to solve.
But I believe these ideas actually lead people astray. They try to make root cause analysis “too simple.”
I will debunk each of these ideas and then tell you how you can learn a technique that was designed to be as simple as possible while still meeting the fundamentals of good root cause analysis.
It’s a Waste of Time to Use Full Root Cause Analysis on Every Problem – DEBUNKED
I sort of agree with this statement. What I don’t agree with is the answer experts arrive at. Their answer is that you should apply some “simple” root cause analysis technique (like 5-Whys or Apparent Cause Analysis) to “solve” these problems that don’t deserve a complete root cause analysis.
First, why am I opposed to 5-Whys, Apparent Cause Analysis, or other “simple” techniques? The answer is that those techniques don’t work (or at least don’t work well). Do you need examples to prove this? Try these four articles:
Six Problems I’ve Observed When Root Cause Analysis Becomes Too Simple
The Curse of Apparent Cause Analysis
5-Why Examples [The Best and The Worst!]
But I also believe that many companies are analyzing incidents (performing root cause analysis) that don’t need to be analyzed.
Not every problem deserves a root cause analysis.
What problems don’t need to be analyzed? Problems that aren’t going to teach you anything significant. I call these “paper-cut problems.” You don’t need to investigate paper cuts.
Some people say that you do need to investigate every loss time injury and medical treatment case to prevent more serious incidents. Maybe … maybe not.
You NEED to investigate an incident if it could have caused an outcome that you are trying to prevent. I call these PRECURSOR INCIDENTS. What is a precursor incident? Here is a definition:
PRECURSOR INCIDENT
Minor incidents that could have been major accidents
if one or more Safeguards had failed.

Some medical treatment cases are precursor incidents. For example, the worker got his cut finger, but he could have lost his arm.
Want more examples? See THIS ARTICLE. Or see our “How Far Away is Death?” articles with precursor incidents. Here is a sample…
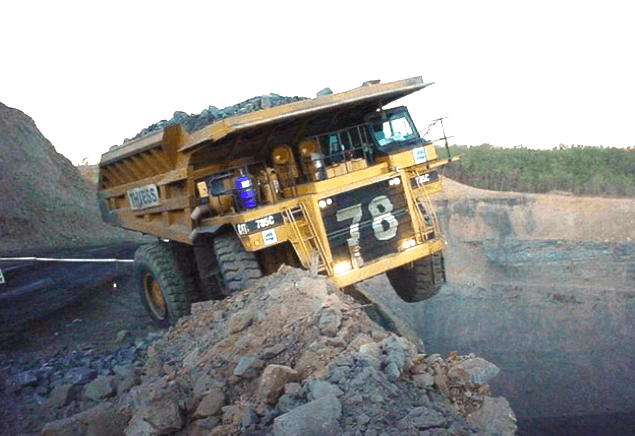
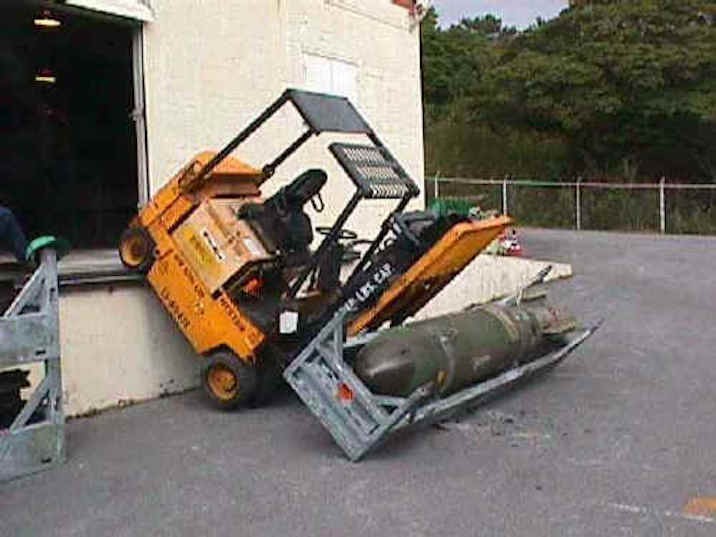
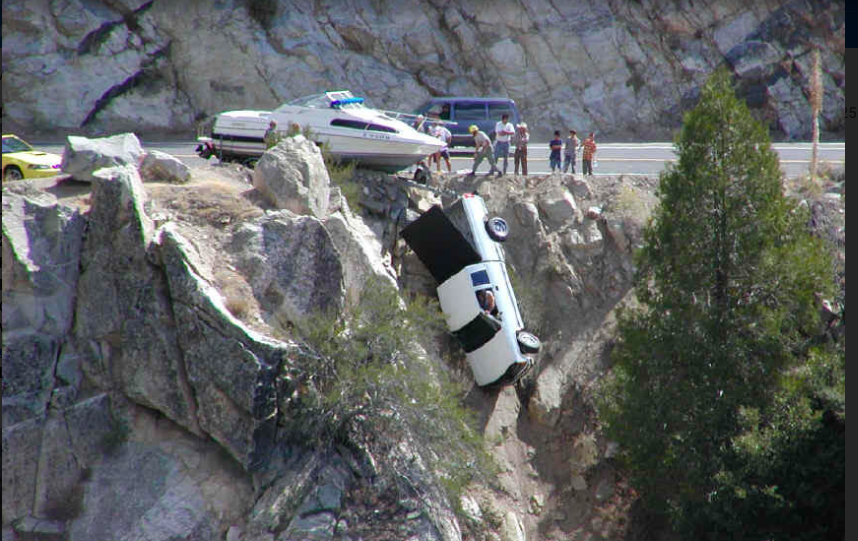
Even though no one was injured in any of the above accidents, there could have been serious injuries or fatalities (sometimes called a SIF). Therefore, you really need to find and fix the incident’s root causes to prevent future serious injuries and fatalities.
So, if the common “simple” techniques don’t work well to prevent future SIFs, what should you use to investigate precursor incidents?
That’s the question we set out to answer when we wrote the book, Using the Essential TapRooT® Techniques to Investigate Low-to-Medium Risk Incidents. To order a copy, CLICK HERE.
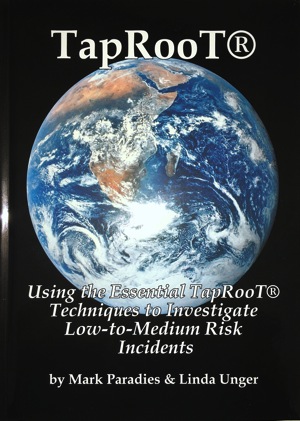
To start, we designed a simple process that guides the investigator through the essential TapRooT® Techniques…

Note that after the first step, finding out what happened and drawing a SnapCharT® Diagram, you can decide to go forward with root cause analysis or stop if you think there is nothing more to learn.
Stopping if there is nothing more to learn is a great way to prevent wasted effort.
I won’t talk you through the remainder of the process here (CLICK HERE for a summary), but once you know how to do a real “simple” investigation with an effective technique, you won’t need to do a bad root cause analysis with an ineffective technique.
Thus, the first idea about “simple” root cause analysis has been debunked. You don’t need (and shouldn’t use) an inferior technique to analyze simple incidents.
People Can’t Understand Complex Root Cause Analysis Techniques – DEBUNKED
I don’t know every “complex” root cause analysis technique, but I do know that this statement does NOT apply to TapRooT® Root Cause Analysis. Why? Because we’ve tested it.

One “test” was at a refinery. The Operation Manager (a good guy) thought that TapRooT® RCA was a good system but wasn’t sure his operators would understand how to use it. So, we ran a test.
We decided to teach a 2-Day TapRooT® Course to the refinery’s union stewards. Then, refinery management could conduct a focus group with the shop stewards to see if they thought it could be used at the refinery.
I was one of the instructors, and from the course examples they analyzed, I knew that they really enjoyed finding real root causes rather than placing blame.
After the course, they performed a focus group (with us in another room). I could hear what was going on. The facilitator asked the first question: “Did you understand the TapRooT® Root Cause Analysis Technique?” One of the shop stewards said …
“If I can run a Cat Cracker, I can certainly understand this.
After all, it’s not rocket science!”
And that’s one of the great parts of TapRooT® Root Cause Analysis. We’ve added expert systems for analysis of equipment and human performance problems, but we’ve kept the system understandable. We made TapRooT® RCA easy to use.
Making it seem like it isn’t rocket science (even though a whole bunch of science is embedded in it) is the secret sauce of TapRooT® Root Cause Analysis. And that’s why we can certainly say that the idea that TapRooT® is too complex for people to use has been DEBUNKED.
Learning Simple Techniques Will Get People to Start Thinking More Deeply About Problems – DEBUNKED
Learning to count is required before you learn calculus, BUT counting over and over again does not teach you calculus.
If you don’t understand the causes of human performance problems, you won’t find the causes of the problems by asking why. And I don’t care how many times you ask why … it still won’t work.
For years, we did a basic poll at the start of our 5-Day TapRooT® Advanced Root Cause Analysis Courses. We asked:
“How many of you have had any formal training
in human factors or the causes of human error?”
Only about 2% of the attendees had ANY training on the causes of human error.
Then we asked how many people had been asked to find the root causes of an incident that included a human error. Almost everybody raised their hand in every course.

Maybe that’s why so many people who haven’t been trained in TapRooT® RCA stop at “human error” as a root cause. They just don’t know that they could discover fixable root causes for human error.
So, NO. Learning simple techniques DOES NOT get people to “think deeper” about problems. That idea has been DEBUNKED.
Simple Techniques Are Just About as Good as Those Fancy Techniques – DEBUNKED

NO WAY.
First, I’ve never seen a good example of 5-Whys. I’ve seen hundreds of bad examples that 5-Why experts thought were good examples. One “good example” that I remember was published in Quality Progress, the magazine of the American Society for Quality (ASQ). I couldn’t stand it. I had to write a reply. When I sent the letter to the editor, they asked me to write a whole article … so I did. To see the example and my article that was published in Quality Progress, see page 32 of the edition of Quality Progress linked below…
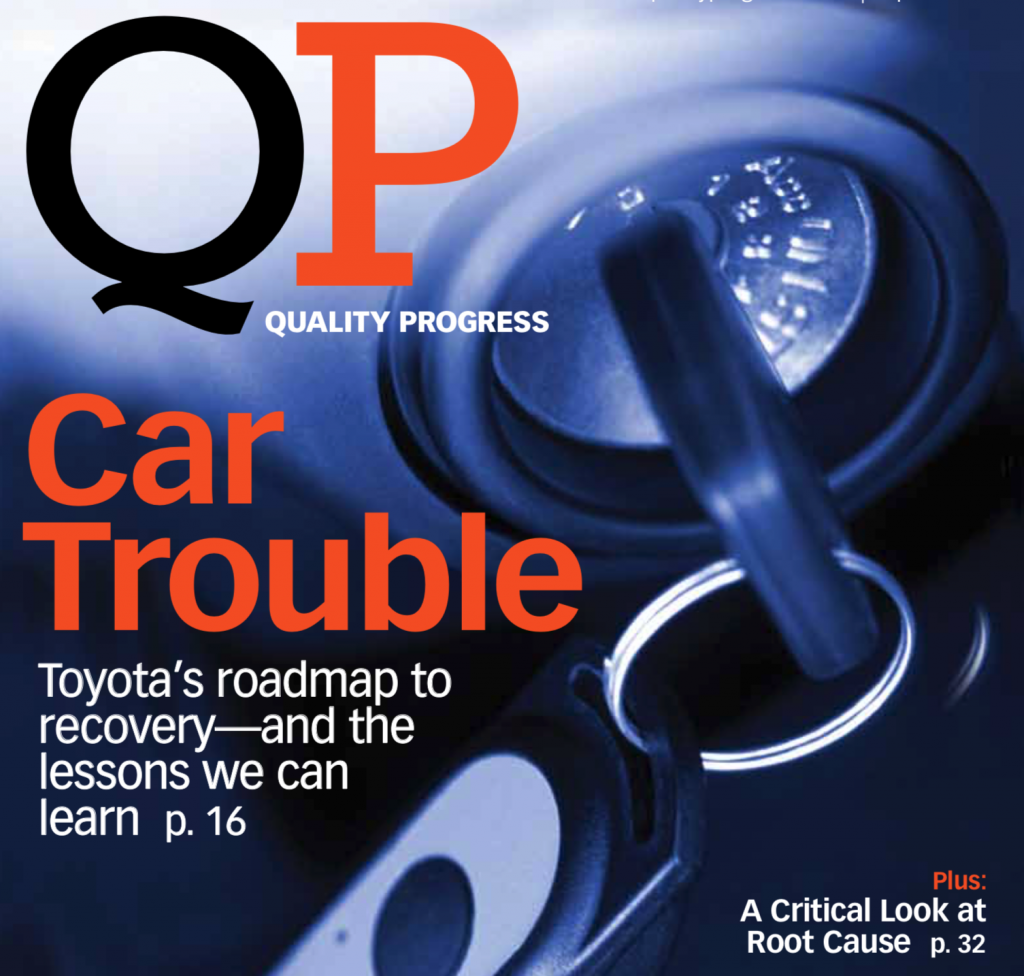
Simple is not “almost as good” as real root cause analysis (TapRooT® RCA). If you would like another example, see Comparing 5-Whys with Advanced Root Cause Analysis.
That’s it – this idea is DEBUNKED. Those “simple” techniques are NOT just about as good as TapRooT® Root Cause Analysis.
Managers Don’t Have Time to Do Fancy Root Cause Analysis, and They Already Know What is Wrong – DEBUNKED
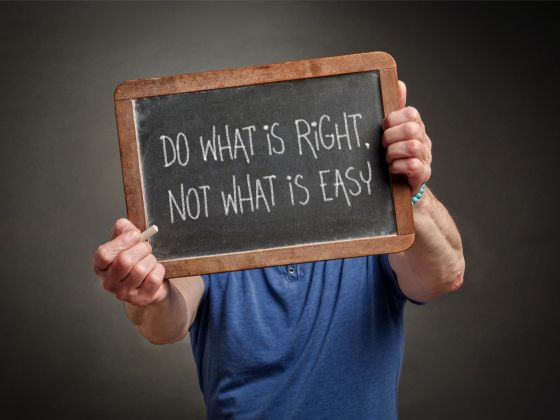
Once again, I’m reminded of a saying:
Why is there never enough time to do it right,
but there is always enough time to do it over?
How many times have I seen managers misdiagnose problems because they didn’t find the root causes and then have bigger accidents because they didn’t fix the near-misses and small accidents?
What managers don’t have time for is repeat incidents. Managers don’t have the resources to waste implementing ineffective fixes.
The statistics for how many people have human factors training above (about 2%) is very similar to the for managers. They don’t teach human factors in MBA programs. This means that managers need an effective root cause analysis technique … just like investigators need an effective technique.
So, if you don’t have time, don’t worry. You WILL make time to do it over and over again.
That reminds me of a quote from a plant manager I knew…
“If we investigated every incident,
we’d do nothing but investigate incidents!”
If you used effective root cause analysis, you wouldn’t have repeat incidents, and you would have time to investigate the few incidents that you would have.
Thus, management not having time and already knowing what to do is DEBUNKED.
You Can Apply Those Complicated Techniques to Just the Most Serious Accidents – DEBUNKED
First off, good root cause analysis isn’t complicated (we have already shown that).
However, I’ve seen companies save their “best” root cause analysis for big accidents. Here are the two problems I see with that…
FIRST, they have big accidents BECAUSE they didn’t solve the precursor incidents. Why? Because they didn’t do a good root cause analysis on the precursor incidents. Thus, applying poor root cause analysis to the lesser incidents CAUSES big accidents.
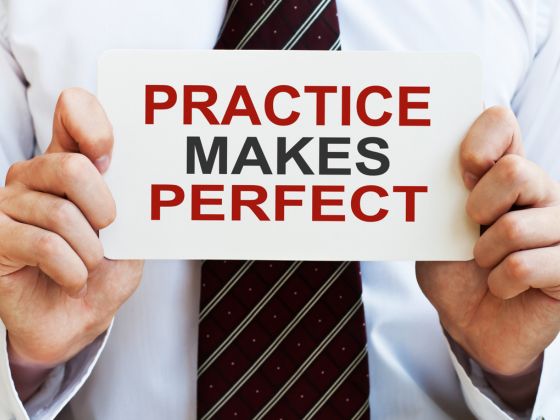
SECOND, their investigators don’t get practice using their “best” root cause analysis techniques because the “most serious” incidents are infrequent. Therefore, their investigators get rusty, or they never really develop the skills they need by using the techniques on smaller incidents that could give them practice. Plus, they learn bad habits using the “simple” tools.
The key here is to learn to use TapRooT® Root Cause Analysis to investigate smaller problems and big problems. And that’s why we wrote a book about using TapRooT® for simple incidents: Using the Essential TapRooT® Techniques to Investigate Low-to-Medium Risk Incidents.
Don’t wait for big accidents to find and fix the causes of your biggest risks. Find and fix them when they give you warnings (the precursor incidents). And this DEBUNKS the save your best for the biggest incidents idea.
The Data From the Simple Investigations Will Help You Identify the More Complex Issues You Need to Solve – DEBUNKED
Why do people think that analyzing lots of bad data will yield good results? I think it is a misconception about mathematics. A good formula doesn’t provide knowledge from bad data.
If you don’t really know how to analyze data, you should attend our pre-Summit course:
As W. Edwards Deming said:
“Without data, you’re just another person with an opinion.”
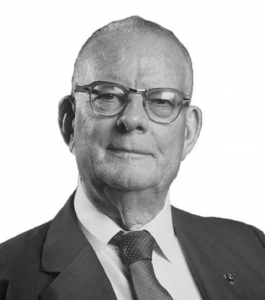
And if you know much about Deming, you know that he was very interested in the accuracy of the data and thought that opinions should be backed by FACTS.
If you aren’t finding the real root causes, data about your BAD ANALYSIS only tells you what you were doing wrong. You now have data about what was NOT the causes of your problems. Analyze that!
So data from BAD simple investigations DOES NOT help you solve your more complex issues. All it does is mislead your management.
Thus, the theory of good data from bad root cause analysis is DEBUNKED!
NOW is the Time to Learn the BEST Root Cause Analysis
If you are using “simple” techniques, now is the time to learn effective, advanced root cause analysis – TapRooT® RCA.
When and where can you learn about TapRooT® Root Cause Analysis? See the dates and locations (around the world) HERE.

Or schedule a TapRooT® RCA Course at your site by calling 865-539-2139 or CLICKING HERE.
Don’t wait. You need advanced root cause analysis to prevent future accidents.
NOW is the Time to Improve Your Root Cause Analysis
If you already use TapRooT® Root Cause Analysis, NOW is the time to make your use of TapRooT® RCA even better. How? By attending the 2024 Global TapRooT® Summit being held at the Horseshoe Bay Resort near Austin, Texas, on April 20 – May 3.
The Summit started with optional, advanced training on April 29-30. See all the pre-Summit Courses HERE.
Then comes the Summit on May 1-3 (Wednesday – Friday).
First, you will learn from motivational, informative Keynote Speakers.
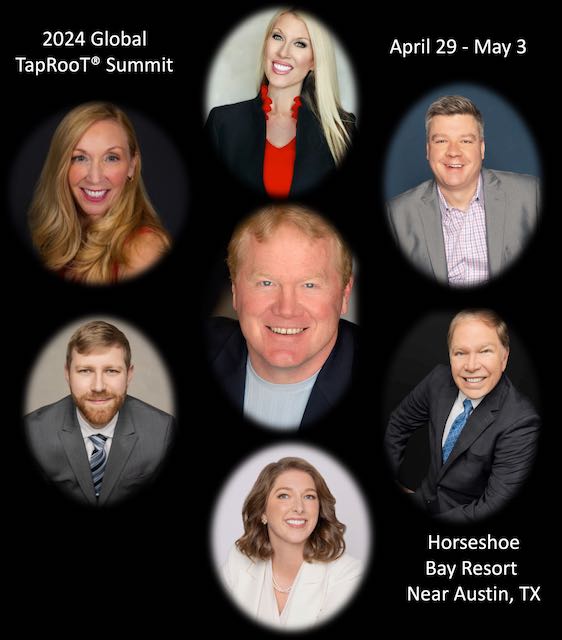
Plus there are seven Best Practice Tracks to choose from, including:
- Improving Investigations & RCA
- Improving Human Performance
- Psychology of Improvement
- Safety Improvement
- Better Improvement Programs and CAPA
- Maintenance and Reliability
- Instructor Recertification
Each of these tracks has nine sessions. Just click on the track name above for details about that track.
The sessions are designed to share best practices from improvement professionals from around the world. Plus, people share new ideas and technology that they have tried, and it worked.
Finally, we have designed the Summit so you will have fun learning and networking. Come to the Summit with one good idea to share, and you will go back home with 20!
We look forward to seeing you there!
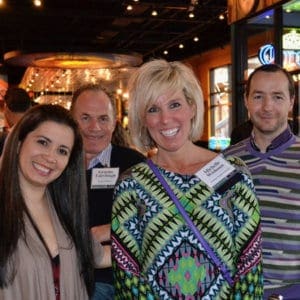