Six Root Cause Analysis Best Practices
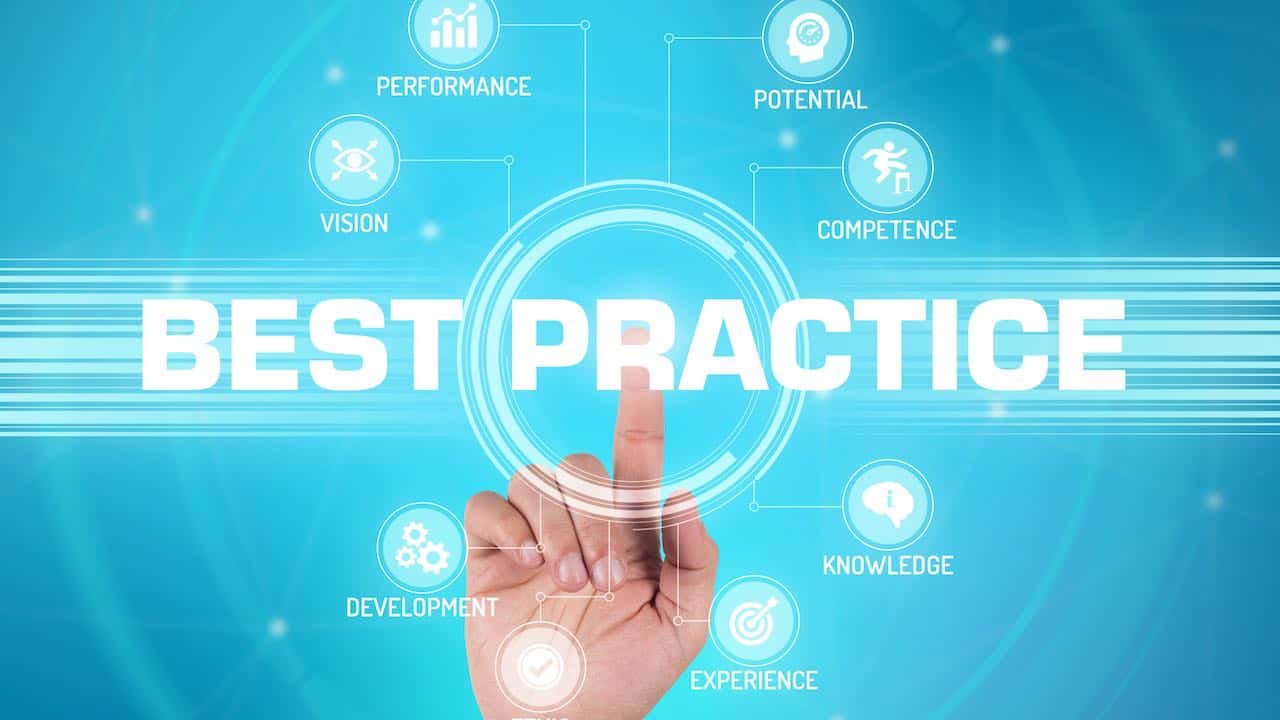
Six Best Practices of Root Cause Analysis
Would your management want you to perform root cause analysis the right way or the wrong way? The six root cause analysis best practices in this article will help you get root cause analysis right!
What is a Root Cause Analysis Performed the “Right Way”
Before we cover the six rights of root cause analysis, we should explain what is a root cause analysis “done the right way.”
So, how would you measure if a root cause analysis was right or wrong? That’s a great question! For the best answer, you should read about grading a root cause analysis HERE.
But to cover the main points quickly, to be successful in completing a root cause analysis, you should:
- Provide a complete, clear picture of what happened.
- Identify all the problems (Causal Factors) that led to the incident being investigated.
- Find the real root causes of each problem.
- Find the Generic Causes of each Root Cause.
- Develop effective corrective actions.
- Get management to understand the problems and solutions and take timely action to get the solutions implemented.
The question is, what best practices do you need to implement to make successful root cause analysis happen?
1st Root Cause Analysis Best Practice
The first thing you should do is provide a complete, clear picture of WHAT HAPPENED.
Without a complete, clear picture of what happened, the investigator is just making things up. The results of the investigation will be guesses.
If you need to provide a complete, clear picture of what happened, you need to:
- Know how to collect evidence.
- Organize that evidence into a complete, easy-to-understand story.
- Share that evidence and story with others (management, other investigation team members, or workers).
How do you do that?
In the 1980s, we discovered a technique taught by the System Safety Development Center at the Department of Energy and used in the nuclear industry (an investigator from Duke Power shared his experience with me) called Events and Causal Factors Charting (E&CF Charting). This technique was based on another technique used by an NTSB investigator. That technique was called Multi-Linear Events Sequencing (MES). We used E&CF Charting in the first generation of the TapRooT® Root Cause Analysis System but eventually simplified and improved the technique – the SnapCharT® Diagram.
The SnapCharT® Diagram is a best practice used by industry leaders worldwide to provide a clear picture of what happened and how it happened to investigation team members, managers, workers, and regulators. We’ve proven its effectiveness and taught it to all workforce levels.
A sample, simple SnapCharT®, is shown below…

A more complex SnapCarT® for a more complex incident is shown below…

If you want some tips to draw a great SnapCharT® Diagram, see this video…
SnapCharT® Diagrams are used throughout the investigation process, from planning your investigation to presenting your investigation to management to get your corrective actions approved and implemented.
2nd Root Cause Analysis Best Practice
Identify all the problems (Causal Factors) that led to the incident being investigated.
Many people focus on a single problem (even a single root cause) when they are investigating an incident. If the investigator focuses on a single cause, they will miss other opportunities to improve performance and stop future incidents. Why? Because usually, there is more than one problem (Causal Factor) that leads to an Incident.
The best practice we discovered in the 1980s is that even for fairly simple incidents, there are usually multiple problems that need to be analyzed.
We call these problems Causal Factors and teach students how to identify them.
3rd Root Cause Analysis Best Practice
Find the real root causes of each problem.
Even with all the evidence in front of them, people can get tricked into the wrong root cause. How? There are several common errors, but here’s a shortlist of potential problems:
- Confirmation Bias
- Favorite-Cause-itis
- No human factors training/guidance
- No systematic process
- Thinking they know the cause
- Picking from a list of causes
We could write a whole article about these problems (and we have HERE, HERE, and HERE), but instead, let’s look at a best practice that provides advanced, guided root cause analysis – the Root Cause Tree® Diagram.

We started the development of the Root Cause Tree® Diagram in the 1980s. The Root Cause Tree® Diagram is based on human factors research/principles from Mark Paradies’ work at the University of Illinois and equipment reliability best practices from the Nuclear Navy. But there is more. There are 30 years of research and development. Read more about the Root Cause Tree® Diagram’s development HERE and HERE.
The Root Cause Tree® Diagram is supported by the Root Cause Tree® Dictionary, which helps investigators consistently find the real root causes of problems.

To read more about how the Root Cause Tree® Diagram is used, CLICK HERE.
4th Root Cause Analysis Best Practice
Find the Generic Causes of each Root Cause.
Some people stop when they find a root cause. But we’ve found a best practice that goes beyond a simple root cause analysis. We suggest that you find the Generic Causes.
Generic Causes start with the root causes and then go beyond the root cause to find what is allowing the root cause to exist. Fixing Generic Causes can help you eliminate whole classes of problems. Here is an example…
Let’s say that you have a problem with a procedure that has more than one action in a step. On the Root Cause Tree® Diagram, you would identify the root cause:
- more than one action per step
To fix that procedure, you would rewrite the procedure with just a one action per step.
Once you have finished fixing the one procedure involved in this incident, you might start thinking:
What about our other procedures?
Do those procedures have similar problems?
If you find that many procedures have “more than one action per step,” then you know there is a Generic Cause. You need to ask what in the system allows procedures to be written and approved with more than one action per step.
See more about going beyond root cause analysis by CLICKING HERE.
5th Root Cause Analysis Best Practice
Develop effective corrective actions.
You might think that once an investigator finds the real root and Generic Causes, they are home-free. What could go wrong? But in the 1990s, we discovered that many people, even when identifying root causes, still didn’t develop effective corrective actions. That was when we developed another best practice – The Corrective Action Helper® Guide (first published in 2000).

The Guide (also a part of the TapRooT® Software – The Corrective Action Helper® Module) helps the investigators think outside the box and develop effective corrective actions.
Here is an example of the suggestions provided for the root cause “Labels Need Improvement:”

The guide also provides ideas to correct Generic Causes and References to learn more about correcting every root cause on the Root Cause Tree®.

Of course, our corrective action best practices include more than just the Corrective Action Helper® Guide/Module. Here is Ken Reed discussing additional best practices to improve your corrective actions…
6th Root Cause Analysis Best Practice
Get management to understand the problems and solutions and take timely action to get the solutions implemented.
Now you:
- Understand what happened,
- Defined the Causal Factors,
- Identified all the Causal Factors’ root causes,
- Identified any Generic Causes, and
- Developed effective corrective action.
What’s left? Getting management to approve the corrective actions and get them implemented.
And that’s where the last best practice comes in. The last best practice is an effective method to present the investigation to management and get their approval to implement effective corrective actions.
This best practice includes a tool mentioned in the 1st Best Practice – the SnapCharT® Diagram.
We find that management is much more likely to commit resources to corrective actions when they understand:
- What happened,
- Why it happened, and
- How can they can get it fixed so that it won’t happen again.
All you need to do is to make this fit together into an easy-to-understand presentation.
The SnapCharT® Diagram is a great way to communicate what happened when presenting an incident to management. We teach using the SnapCharT® Diagram to make presentations in the 2-Day TapRoot® Root Cause Analysis Course and the 5-Day TapRooT® Advanced Root Cause Analysis Team Leader Course. See the upcoming worldwide public course locations and dates HERE.
Best Practice Root Cause Analysis Processes
If you are familiar with the TapRooT® Root Cause Analysis System, you probably already recognize that Best Practices 1-6 are built into both the TapRooT® Simple Investigation Process and the TapRooT® Major Investigation Process. Both processes are shown below.


Learn both processes in the 5-Day TapRooT® Advanced Root Cause Analysis Team Leader Course.
BONUS RCA Best Practice … The Summit
In addition to the six root cause analysis best practices and two best practice processes, THERE IS MORE. Our TapRooT® Users teach us dozens of new best practices each year. Where can you learn about them? At the Global TapRooT® Summit.
The Global TapRooT® Summit is a meeting of TapRooT® Users and performance improvement experts from around the world. Participants share new best practices and lessons learned. Experts present the latest root cause analysis, incident investigation, and performance improvement technology.
But perhaps the best part of the Summit is the networking. As they say, it’s not what you know but who you know. And you will meet some great people at the Global TapRooT® Summit.

In addition to the networking, there are interesting, inspiring Keynote Speakers and highly educational Best Practice Tracks. Plus, there are special pre-Summit Courses for even more learning.
Where and when is the next Global TapRooT® Summit? CLICK HERE to find out.
I don’t think you will find any other Summit or Conference with a GUARANTEE, but here is the guarantee for the Global TapRoot® Summit…
GUARANTEE: Attend the Global TapRooT® Summit. Go back to work and implement your road map to success. If you don’t save 10 times the cost of your attendance at the Summit, let us know and return your Summit materials and we will refund 100% of the Summit registration fee. This guarantee shows how certain we are that you will learn valuable best practices to take your facility’s performance to the next level.
Thus, attending the Global TapRooT® Summit is a guaranteed Best Practice. Don’t miss it! REGISTER HERE.
Get Your Root Cause Analysis Best Practices Started
Attending TapRooT® Training is the best way to get your root cause analysis best practices started. CLICK HERE for upcoming worldwide course locations and dates.
