Risk of Waiting to Improve RCA
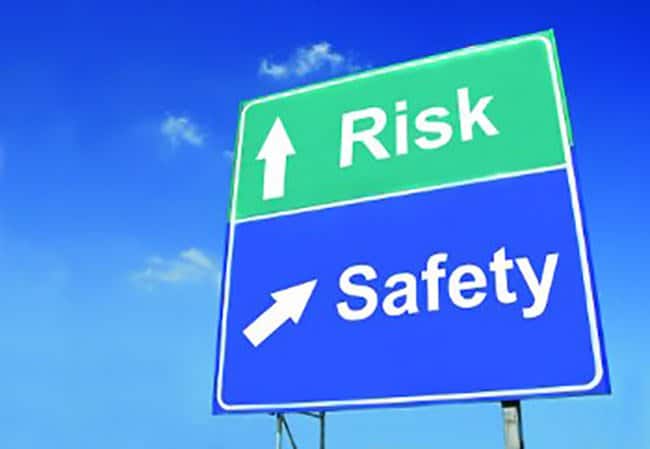
Why Improve?
If you have a poor root cause analysis system, you need to improve it.
What is a poor root cause analysis system?
- No system.
- A system that doesn’t provide guidance to investigators.
- A system whose main feature is that it is easy to use (but is not effective).
- A system that is overly complex and doesn’t work for people in the field.
- A system that management can’t understand.
- A system that is solely chosen based on cost (not effectiveness).
- A system that doesn’t meet the fundamental requirements of root cause analysis.
People with a bad root cause analysis system probably should just use Spin-a-Cause™. At least they would be using the world’s fastest root cause system.
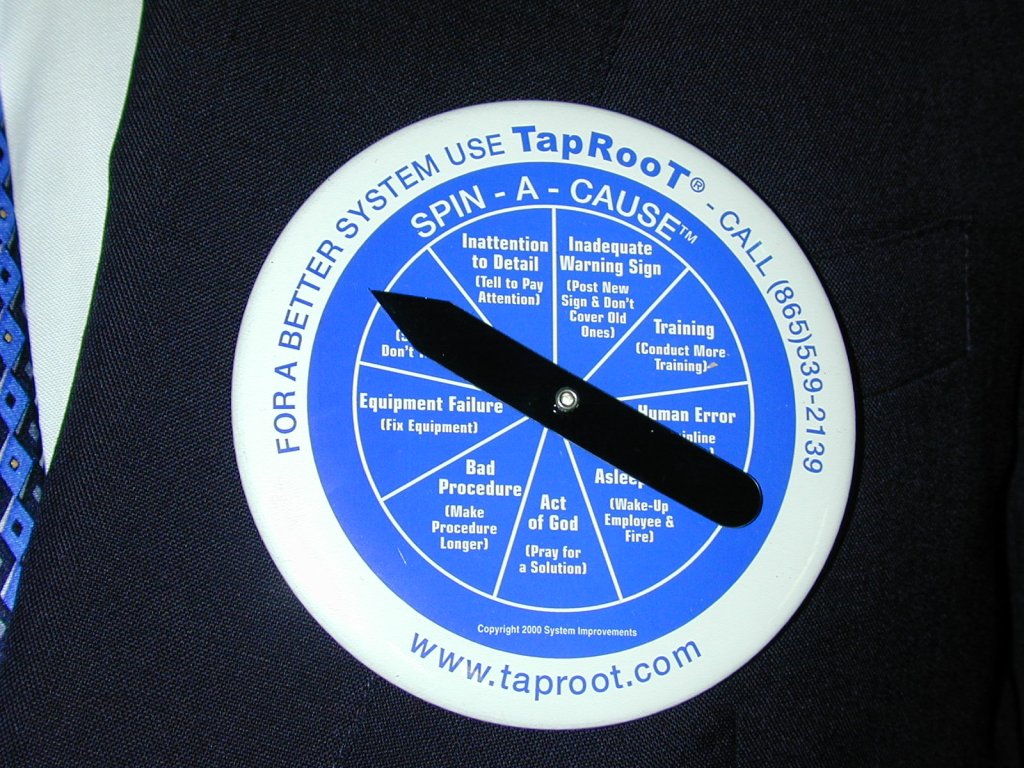
People using these systems know they need to improve their root cause analysis, but they are waiting because:
- They don’t have a budget to improve.
- They can’t decide how to improve.
- They don’t know how to convince management of the need to improve.
- They want a system that costs nothing, is technically excellent, and requires no effort.
- They like procrastinating.
Risk of Waiting
If you are waiting to improve root cause analysis, have you considered the risk of waiting?
What risk?
Every time you do an investigation with a poor root cause analysis tool, you could:
- Fail to recognize a root cause that needs to be corrected.
- Identify root causes that aren’t really root causes and waste time implementing corrective actions that won’t fix the problem.
- Find a root cause but fail to find all the root causes (the single root cause error).
- Find a root cause but recommend an ineffective fix.
What could happen if you fail to find and fix the root causes of precursor incidents? A major accident.
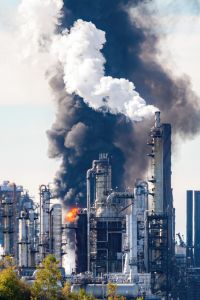
Major accidents can cause fatalities, significant injuries, major expenses, plant downtime, and perhaps even major quality issues—all of which you need to prevent.
Start Your Improvement NOW!
The first step to starting your improvement efforts is to attend a TapRooT® Root Cause Analysis Course. Here are some suggestions…
- If your main focus is improving equipment reliability, I recommend the 2-Day Equifactor® Equipment Troubleshooting and TapRooT® Root Cause Analysis Course.
- If you want to reduce fatalities and significant injuries, I recommend the 5-Day TapRooT® Advance Root Cause Analysis Course. It covers all the TapRooT® Techniques and helps you solve both human performance and equipment reliability issues.
- If you only have a couple of days to learn the essential techniques, I recommend the 2-Day TapRooT® Root Cause Analysis Training.
- If you can’t travel to one of our in-person TapRooT® Courses, I recommend having a course at your site or attending one of our 3-Day Virtual TapRooT® Root Cause Analysis Courses. To get a quote for an on-site TapRooT® Course, CLICK HERE.
Don’t Wait! See all of our public TapRooT® Courses HERE.
If you want to go beyond our initial training, I recommend attending the Global TapRooT® Summit. The Summit includes a best practice track focussed on incident investigation and root cause analysis best practices (as well as seven other tracks). CLICK HERE for more information.
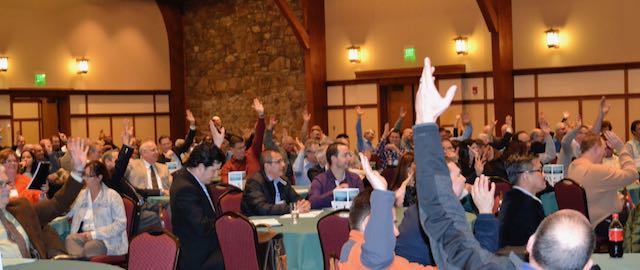