Procedures Not Used Cause an Accident
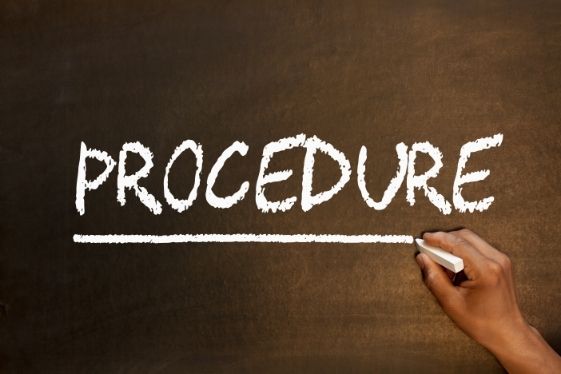
Accidents Caused By Procedures Not Being Used
How many major accidents are caused by the failure to use a procedure? In the TapRooT® System, this is the near-root-cause “Procedure Not Used.”
I’ve seen many famous accidents that included this problem. For example, the BP Texas City Refinery explosion outlined in the report below…

I’ve also seen root cause analysis statistics that have “Procedure Not Used” as one of the most frequently identified near-root causes.
Why Don’t People Use Procedures?
When I talk about procedures, I’m not talking about policies. I’m talking about work-related checklists and detailed written procedures that document how a job is to be performed in a step-by-step way.

So, why do people make mistakes using procedures? The TapRooT® Root Cause Tree® suggests many reasons that operators or maintenance techniques might make mistakes using a procedure. This includes reasons why they might not use or not properly follow procedures.

All of these reasons are described in detail by the questions an incident investigator should answer in the TapRooT® Root Cause Tree® Dictionary.

Here are some of the reasons for procedures not being used or not being followed, as suggested by the Root Cause Tree® Dictionary:
- There was no procedure.
- The procedure wasn’t available or wasn’t easily available for the user.
- The procedure was considered too difficult to use by the operator or mechanic.
- The procedure was written in a different language than the native tongue of the user.
- There is no requirement to use the procedure.
- Procedure usage isn’t enforced (see the Management System, SPAC Not Used Basic Cause Category).
Why Do These Procedure Usage Problems Exist?
Why do these problems exist at so many facilities? After all, if they cause accidents, why haven’t these problems been eliminated?
I believe there are several major reasons:
- Management doesn’t understand the importance of well-written procedures in achieving high-reliability operations.
- Management, supervisors, and operators don’t understand what “using” a procedure means.
- Supervisors don’t understand their role in ensuring procedure usage.
- Operators and maintenance technicians think that procedures are just training aids to be used by trainees. They think performing a procedure from memory is OK (any “good” operator knows the procedure and doesn’t require a written copy).
What should management do to ensure procedure usage and prevent accidents?
- Invest in well-written procedures that are thorough yet easy to use.
- Make sure that procedures are available to plant staff.
- Train people about the importance of procedure usage and what can happen when procedures are not used. This should include the human factors/psychology behind how procedures improve performance.
- Conduct regular supervisor and management audits of procedure usage on all shifts.
- Install cameras to remotely monitor and record operations and procedure usage.
- Develop a rewards program for proper procedure usage
Are the items above part of your human performance improvement program? If they aren’t, you are waiting for an accident to start these improvement efforts?
Where Can You Learn More About Procedures and Human Performance Best Practices?

One of the best places is our Stopping Human Error Training, a highly-rated, interactive course.
Get details about the course HERE.
Our next public course is being held on October 4-5 in Knoxville, TN. Register by CLICKING HERE. Don’t wait. Register TODAY!
See additional course dates by clicking HERE.
If you would like to hold a course at your site, contact Alex Paradies at 865-539-2139 or CLICK HERE to contact him by e-mail.
My personal experience of both conducting and peer reviewing many investigation reports over the years aligns well with your statistical review of root causes that identify “Procedure Not Used” as one of the most frequently identified near-root causes.
I’ve seen too many investigations blame the person for not using the procedure – without giving any consideration to why the procedure wasn’t followed. When you dig deeper, you see far too many verbose procedures, with non-sequential steps, without emphasis or warning of ‘critical steps’ within the procedure, written in non-standard formats, and it’s no surprise they are never used or followed.
The last two paragraphs of your blog provide some very useful tips about how to break the nexus and start improving human performance. – many thanks!
Thanks for the feedback.
I see you’ve been to a 2-Day Equifactor® – Might try 5-Day when you get a chance. Lot’s more about procedures.
Best Regards,
Mark