Proactive Equifactor® Troubleshooting
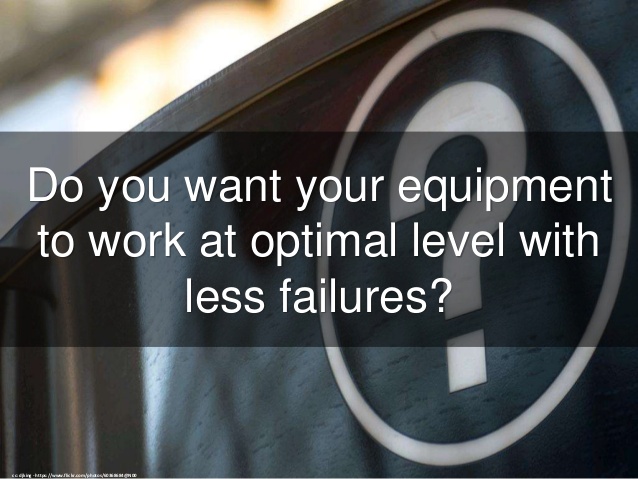
Maybe this is a use of Equifactor® Troubleshooting that you’ve never thought of before…
You have been assigned to a team that has been tasked with installing a new air compressor that will be used as part of a new process.
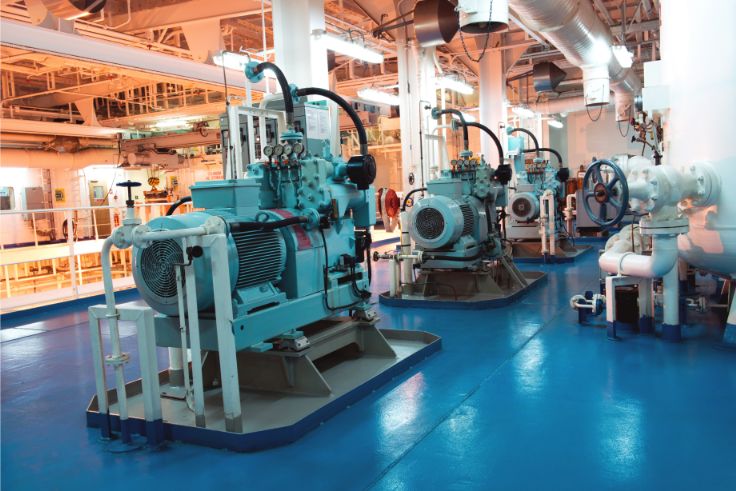
Your specific job is determining what preventive and predictive maintenance activities you will require for the new compressor. Where do you get this type of information?
You can start with the manufacturer’s recommendations, but we all know this is a pretty coarse set of guidelines. Wouldn’t it be nice if you knew how the compressor could possibly fail before it was installed? You could then design your PM and PdM requirements to look for these failure pathways.
As a TapRooT® User, you remember that Equifactor® Troubleshooting is normally used to troubleshoot specific equipment failures and aid in your root cause analysis. But what if we use Equifactor® Troubleshooting to list ALL POSSIBLE equipment faults and then design our monitoring systems to look for these faults?
You can use Equifactor® Troubleshooting Tables to:
- Determine what vibration monitoring is required to look for the listed symptoms
- List what preventive maintenance may be required to prevent the failures from occurring
- Update the operating procedures to keep the equipment operating conditions away from common failure modes
- Design an operator training program to teach your people to look for specific incipient failure conditions
- Include the gear in your company’s lube oil analysis program
- Conduct an RCM analysis to see what maintenance is really required based on known Equifactor® Failure Modes
And you are just getting warmed up!
It is tough to set up your CBM system to try to minimize your maintenance workload if you don’t know what maintenance is required in the first place. Take a look at how you would normally set up these types of programs for new equipment, and see how Equifactor® Troubleshooting can be used as yet one more tool to make your life easier.
For upcoming public Equifactor® Courses, CLICK HERE.
To schedule Equifactor® Training at your facility, contact us by CLICKING HERE.
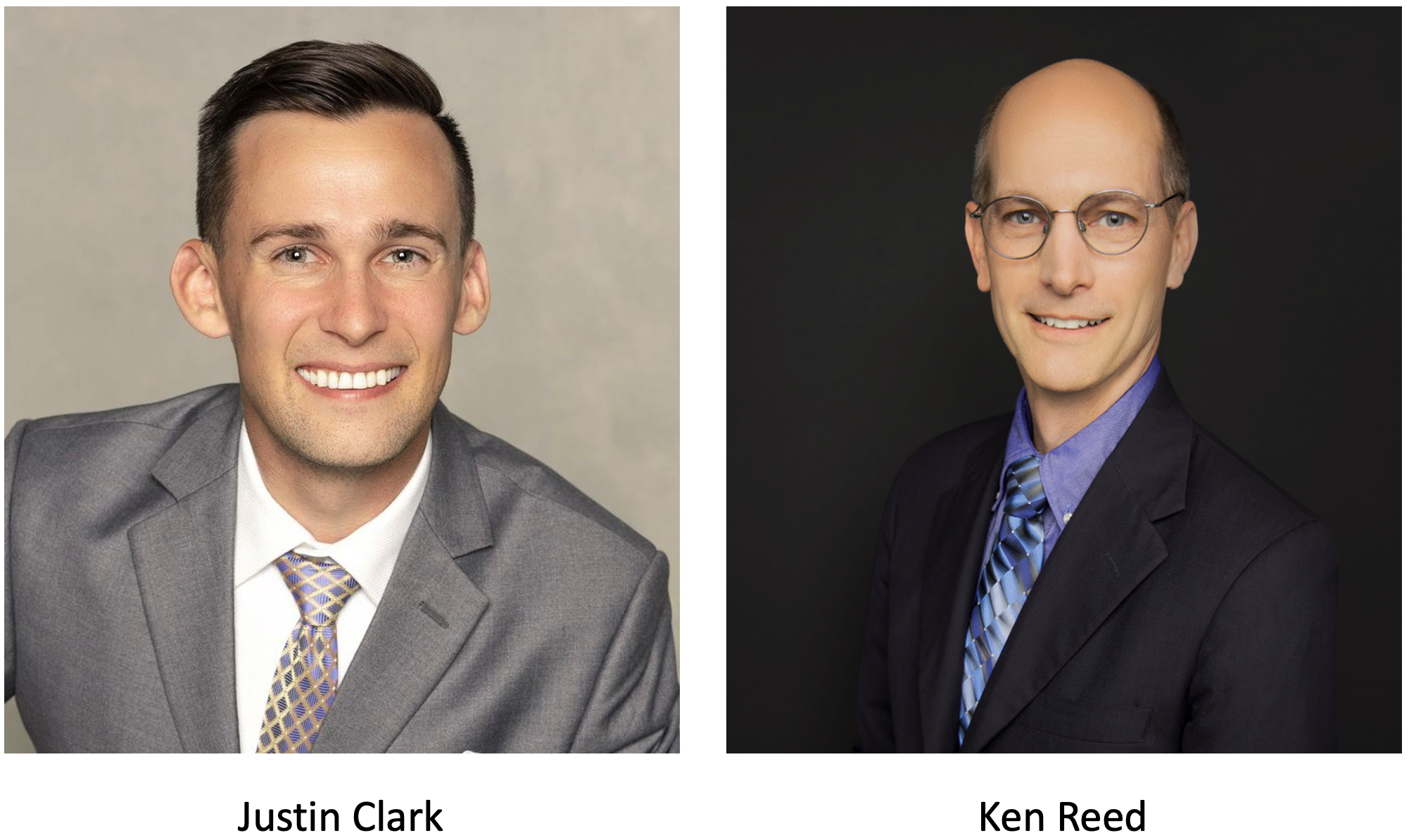