A Practical Guide to HOP, TapRooT® Root Cause Analysis, and Improving Human Performance
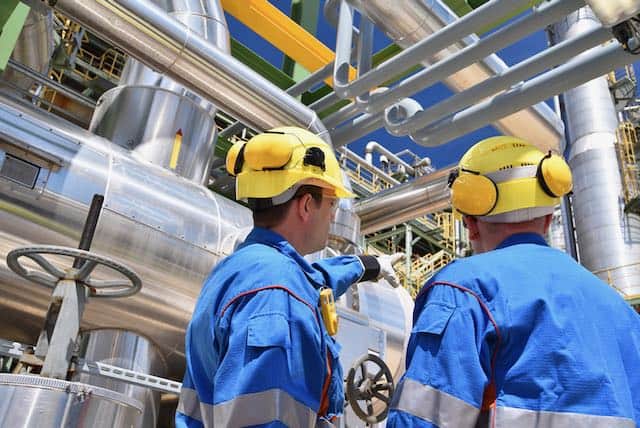
What is HOP?

Before you understand HOP and how it works with root cause analysis, you need to understand the basics of HOP.
HOP stands for…
Human & Organizational Performance
Or some variation of those words. It doesn’t require jumping and has nothing to do with beer. It is related to HU – the nuclear industry abbreviation for Human Performance Tools (HU comes from the first two letters of human).
HOP is a philosophy and a group of techniques mainly developed in the nuclear industry to achieve peak human performance.
Contrary to many practitioners’ beliefs, it isn’t primarily a safety tool or some sort of new “safety differently” approach. Rather, it should be a way to be more efficient and effective when working that improves all human performance (not just safety performance).
We’ve written articles about HOP before, including one article about taking HOP to the next level. (We called it HOP II – CLICK HERE to read.)
What is today’s article about? A recent paper I read titled:
Safety, Leadership and Learning
– A practical guide to HOP
published by The Federation of Norwegian Industries. Unfortunately, I couldn’t find a link to the paper to include here, but I did find a link to a presentation that summarizes what was written in the paper. CLICK HERE to view it.
The Safety, Leadership and Learning paper made me think of how long and how effectively TapRooT® Root Cause Analysis has been used as a human performance improvement tool. I thought many readers might be interested in the topic of how TapRooT® RCA can be used in a human performance program and how TapRooT® RCA can improve HOP.
HOP Principles
In the Safety, Leadership and Learning paper (and in the presentation) are five HOP principles that are a shared belief by many HOP practitioners. They are…

Note that I modified the fourth principle because I believe using the word “behavior” (or the English spelling – behaviour) is blame oriented. I prefer “action,” which doesn’t have any blame connotation. (Action is generally viewed as good where behavior can be associated with a choice, as in “misbehavior.”)
TapRooT® RCA and HOP
If you reviewed the presentation and you are a TapRooT® Root Cause Analysis User, you probably saw many similarities. Marcus Miller wrote about the HOP principles in THIS ARTICLE.
I will detail other similarities and how long the TapRooT® System has been used to accomplish improved human performance in the following sections.
The Performance Plateau
Many different improvement initiatives have reached a performance plateau. The initiative to address serious injuries and fatalities was spurred on by a plateau in the number of fatalities (shown below in a 2015 article in Professional Safety titled Preventing Serious Injuries & Fatalities).

A similar plateau was shown in the Safety, Leadership and Learning paper…

In the past (starting 40 years ago), we have written about reaching a performance plateau and how TapRooT® can be used to see new ways to improve performance and regain momentum in a performance improvement program.
Why do I mention this here? Because finding new ways to improve performance (especially human and organizational performance) isn’t something new. It is what the TapRooT® System is all about and has been all about for over four decades. I will show several examples of this in the following sections.
Context Drives Action
One of the five HOP principles is that “Context Drives Behaviour ACTION.”
Thus, there are things embedded in the system of work that cause action and sometimes cause human errors (or at least make them more likely).
Many times, HOP people call these “Error Traps.” TapRooT® Users see these as root causes on the back side of the Root Cause Tree® Diagram.

An example of one of the Basic Cause Categories on the back side of the Root Cause Tree® Diagram that includes procedure-related error traps is shown below…

I used the Procedures Basic Cause Category because so many HOP presentations include discussions of work as imagined (the procedure) versus work as done (shortcuts or better ways to do things that deviate from the procedure and are adopted by people in the field). However, if a procedure is well written with help and review by people who perform the work, the variation between work as imagined and work as done can be eliminated or at least made less likely.
Thus, the Root Cause Tree® Diagram is a template for eliminating error traps in procedures. In cases where variation from the procedure is needed, there should be a clear way for operators or supervisors to quickly request an approved variation with appropriate, swift technical review (this should be a management standard).
We have written about procedure problems before (especially about people not using or not following procedures – CLICK HERE). So, these ideas are not new to TapRooT® Users.
Thus, the Procedure Basic Cause Category (of the seven categories on the back side of the Root Cause Tree® Diagram) has 21 root causes (error traps) that can be eliminated to improve human performance. In addition, the TapRooT® System includes the Corrective Action Helper® Guide that provides suggestions to improve/eliminate each of these error traps – both in a specific procedure and in procedures in general (generic causes).
This is an excellent example of how TapRooT® Root Cause Analysis can be used to improve human performance. Many TapRooT® Users have been applying these techniques since the early 1990s (and some even before that).
Reactive Versus Proactive
Chapter 3 of the Safety, Leadership and Learning paper focuses on Risk Assessment – the proactive portion of HOP. They propose a modification to the questions to ask when performing a risk assessment (or when performing a Safe Job Analysis or Job Safety Analysis). Then, they provide a sample of four different categories of error traps (Organizational Error Traps, Task-Related Error Traps, Technical Error Traps, and Individual Error Traps). Each of these has a subset of more specific error traps (for a total of 22 error traps).
Once again, since the early 1990s, we have been teaching people how to find the error traps that are listed on the back side of the Root Cause Tree® Diagram. The tree helps people do this in investigations and proactively when performing audits, assessments, and risk assessments. The back of the tree covers all the 22 HOP error traps plus many more (some of which probably are more important than the 22 HOP error traps).
Therefore, TapRooT® Root Cause Analysis Users have had the ability (which they sometimes haven’t applied) to proactively improve performance and avoid potential future accidents – similar to but even more expansive than the recommendations in the Safety, Leadership and Learning paper.
Other HOP Initiatives
Other HOP initiatives include:
- Avoiding blame
- Learning from normal work
- Safety capacity (defense-in-depth)
- Learning from incidents
- Effective corrective action development (including the hierarchy of controls)
- Leadership involvement
I won’t dive into each of these in detail, but needless to say, we have been writing about these factors in the Root Cause Network™ Newsletter and teaching about them in TapRooT® Courses since the early 1990s. For a good start learning about the TapRooT® philosophy, read TapRooT® Root Cause Analysis Leadership Lessons. For more information about the book, see THIS LINK.

The book is a great way to start your journey to improved performance.
Learn More About Improving Human Performance
There are several courses that we offer to help people on their performance improvement (especially human performance improvement) journey.
Stopping Human Error
The first is our Stopping Human Error Course.

What is included in the course? A broad overview of best practices and bad practices for improving human performance. The objective of the course is to give you the knowledge you need to develop a custom human performance improvement program for your company/facility. A custom program that includes best practices that will be most helpful for your employees while avoiding practices that lead to blame.
For more course information, including a complete course outline, CLICK HERE.
You can have this course at your site (CLICK HERE to contact us for a quote or call 865-539-2139). Or you can attend one of our public Stopping Human Error Courses (CLICK HERE for dates and locations).
Learning From Incidents
How can you perform better “learning meetings,” “learning teams,” or just plain incident investigations of human performance issues? For over 40 years, we have been teaching facilitators how to use the embedded human performance expert systems that are in the TapRooT® System to find the root causes (error traps that need to be fixed) and then effectively fix them. You can see a sample of the variety of courses we offer HERE.
The course I would recommend for people really interested in investigating human performance issues is the 5-Day TapRooT® Advanced Root Cause Analysis Team Leader Course.

The course outline includes:
Day One (8:00 am to 5:00 pm)
- Class Introductions and TapRooT® Introduction
- TapRooT® System Overview – What You’ll Be Learning
- SnapCharT® Basics – Gathering Information
- SnapCharT® Exercise – Practice
- Causal Factors – Identifying the Errors
- Root Cause Tree® Diagram – Eliminating Blame
- Root Cause Tree® Exercise – On Your Own
- Corrective Actions – Developing Fixes
- Corrective Action Exercise
Day Two (8:00 am to 5:00 pm)
- Software Tips
- Generic Causes – Systemic Problems
- Enhanced Corrective Actions
- Preparing for Your Investigation
- Collecting Information
- Interviewing
- Interviewing Exercise
- Interviewing Exercise (RCA)
Day Three (8:00 am to 5:00 pm)
- Management System & Changing Behavior
- Equifactor® Equipment Troubleshooting
- Human Engineering
- CHAP & Exercise
- Change Analysis
- Change Analysis Exercise
- Improving Procedures
- Putting It All Together
- Work Direction & Exercise
Day Four (8:00 am to 5:00 pm)
- Human Factors Jeopardy
- Proactive Improvement
- Auditing Using Safeguard Analysis
- Water Hammer Exercise
- Analyzing Training Problems
- Grading Investigations
- Presenting to Management
- Frequently Asked Questions
- Start Final Exercise (SnapCharT® Diagram)
Day Five (8:00 am to 1:00 pm)
- Final Exercise: Safeguards Analysis
- Final Exercise: Define Causal Factors
- Final Exercise: Find Root Causes
- Final Exercise: Find Generic Causes
- Final Exercise: Develop Fixes
- Final Exercise: Presentations
Course materials provided are:
- TapRooT® Major Investigations Book
- TapRooT® Essentials Book
- Laminated TapRooT® Root Cause Tree® Diagram
- TapRooT® Root Cause Tree® Dictionary
- Course Workbook
- Corrective Action Helper® Guide
The course comes with the following money-back guarantee:
Attend this course, go back to work, and use what you have learned. If you don’t find root causes that you previously would have overlooked and if you and your management don’t agree that the corrective actions that you recommend are much more effective, just return your course materials, and we will refund the entire course fee.
Call us at 865-539-2139 to schedule a course at your site, or CLICK HERE to see our public course dates and locations.
By the way, we have been offering a version of this course since 1993.
Learning From Normal Work
Two courses to consider to improve your efforts to learn from normal work are the Stopping Human Error Course (previously mentioned) and the Auditing & Proactive Improvement Using TapRooT® RCA Course.

The Auditing & Proactive Improvement Using TapRooT® RCA Course focuses on using the TapRooT® Root Cause Analysis System proactively during audits and evaluations – an essential part of learning from normal work.
Contact us by CLICKING HERE for a quote for a course at your site, or CLICK HERE to see our upcoming public course dates and locations.
Learning From Success
If you are still considering what to do and you haven’t signed up for one of our courses, what are you waiting for?
Perhaps you need to see what success could look like.
For example, if you are interested in eliminating blame from your investigation, see THIS SUCCESS STORY from ComED-Exelon’s Human Performance Core Team.
Another example is a chemical company that saved about $40 million in two years by stopping procedure usage problems and other “error traps.” For details, see THIS SUCCESS STORY.
If your investigations are inconsistent and need to become systematic, see THIS SUCCESS STORY from Air Canada.
If you are interested in stopping fatalities and significant injuries, see these Success Stories:
- Reducing Lost Time Injuries to Zero
- Stopping Serious Injuries and Fatalities
- Ensuring Employees Go Home After a Safe Day at Work
- Eliminating Serious Injuries in an Oilfield Services Company
Or see all TapRooT® User Success Stories at THIS LINK.
DON’T WAIT

You need the kind of success that TapRooT® Root Cause Analysis brings to improving all types of performance – including (or should I say especially) human performance. Get approval to sign up for a TapRooT® Course today!
Also, consider attending the Improving Human Performance Track at the 2024 Global TapRooT® Summit on April 29 – May 3, being held at the Horseshoe Bay Resort near Austin, Texas.

The Track Leader is Alex Paradies, one of the codevelopers of the Stopping Human Error Course.
What’s in the Improving Human Performance Track? These best practice breakout sessions:
- Using CHAP & Learning Teams Proactively
- Corrective Action Workshop
- Success Story Panel Discussion
- Reducing SIFS & Streamlining Investigations for Improved Performance
- Lessons for Improving Human Performance & Safety (Live Podcast from the Summit)
- Psychological Safety: Building a Stronger HSE Culture
- Lean & TapRooT® ® TCA – Eliminating Waste & Unnecessary Tasks
- Dr. Camille Peres Discusses Human Factors Advances
- Implementing Your Best Ideas
In addition to the talks/workshops in each track, you will hear five Keynote Talks from our lineup of inspiring and insightful Keynote Speakers. The speakers include:
Erika Armstrong (Wednesday AM)

Betsy Allen-Manning (Wednesday PM)

Mark Paradies, Amy Souders, & Alex Paradies (Thursday AM)

Dan Verlinde (Thursday PM)

Karl Mecklenburg (Friday AM)

We know that TapRooT® Users will enjoy the Summit and learn valuable new skills and ideas that they will take back to work and apply. That’s why we can offer this exceptional GUARANTEE:
Attend the Global TapRooT® Summit. Go back to work and implement your roadmap to success. If you don’t save 10 times the cost of the Summit fee, let us know and return your Summit materials, and we will refund 100% of the Summit registration fee.
This guarantee shows how certain we are that you will learn valuable best practices to take your team’s and your organization’s performance to the next level.
Plus, this guarantee also applies to people who have not implemented TapRooT® RCA yet. So, if you are a TapRooT® User or just someone interested in improving performance, you should REGISTER for the 2024 Global TapRooT® Summit NOW!

And if you want to get the most from that Global TapRooT® Summit, bring a team of managers, investigators, and people interested in performance improvement to turbocharge your improvement program. See the savings possible with the discounts for bringing a team shown below.

Get Started NOW!

General George S. Patton said:
A good plan violently executed now is better
than a perfect plan executed next week.
So, now is the time to learn to use:
- TapRooT® RCA to improve your investigations and root cause analysis,
- The Stopping Human Error Course to proactively improve human performance and
- The Global TapRooT® Summit to network with industry leaders from around the world and learn the latest performance improvement best practices to improve human performance.
Get started NOW by using the links above to register for all three.
Do you have questions? Contact one of our TapRooT® Implementation Advisors by by CLICKING HERE or calling 865-539-2139.