TapRooT® RCA Provides Consistency, Guidance, and Influences Positive Culture Change
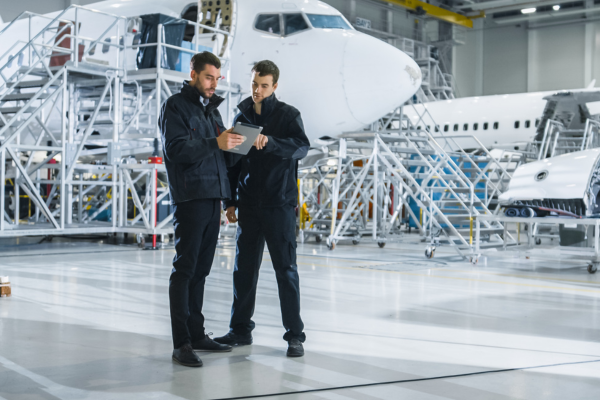
Root cause tools that lack systematic guidance provide inconsistent results and often depend on the knowledge and experience of the investigator conducting the investigation. Michael Fitzmorris, Senior Director, Regulatory Compliance, Training and Safety shares how TapRooT® Root Cause Analysis helped Air Canada Maintenance overcome this challenge.
Challenge
Air Canada Maintenance became interested in what the TapRooT® Root Cause Analysis System had to offer to fill in the gaps they noted in other root cause tools. Many RCA methodologies are simply tools and not systematic investigation processes. RCA “tools” provide inconsistent results and offer little guidance for investigators.
This is significant because in the aircraft maintenance and engineering world, regulatory bodies require that an RCA methodology is in place. It must be clear to the regulator what the methodology is, and how it is used.
Action
Success is a continuous improvement goal. Air Canada Maintenance committed themselves to improve performance by learning and understanding how a robust root cause analysis system like TapRooT® Root Cause Analysis System is an effective tool for safety, quality, and compliance as well as the business overall.
Senior leadership and professionals across the organization dedicated time to learning about the benefits and opportunities the TapRooT® System provides. This is an important step because when the leadership team commits to improving performance, employees become more motivated and committed to improvement.
Results
Air Canada Maintenance achieved leadership and organizational support for effective root cause analysis. They established awareness that RCA is not just a tool for safety, quality, and compliance, but is a valuable business tool for all business units to identify systemic issues and take effective action against repeat occurrences.
As part of an organization that oversees maintenance and engineering across the world, they were able to educate many MRO’s and providers on the effectiveness of TapRooT® RCA and share the ideas and opportunities. In some cases, they sent vendors to TapRooT® Training as a way of helping them help themselves.
Repeat findings are decreasing and the discussion and understanding around effective RCA and corrective actions are more prevalent. Implementing TapRooT® RCA has contributed to positive culture change.
Learn more about how a systems approach can improve performance at your organization. Talk with our thought leaders by scheduling a free, 1-hour Executive Briefing.