Are You Getting to the Real Root of your Pharmaceutical Errors?
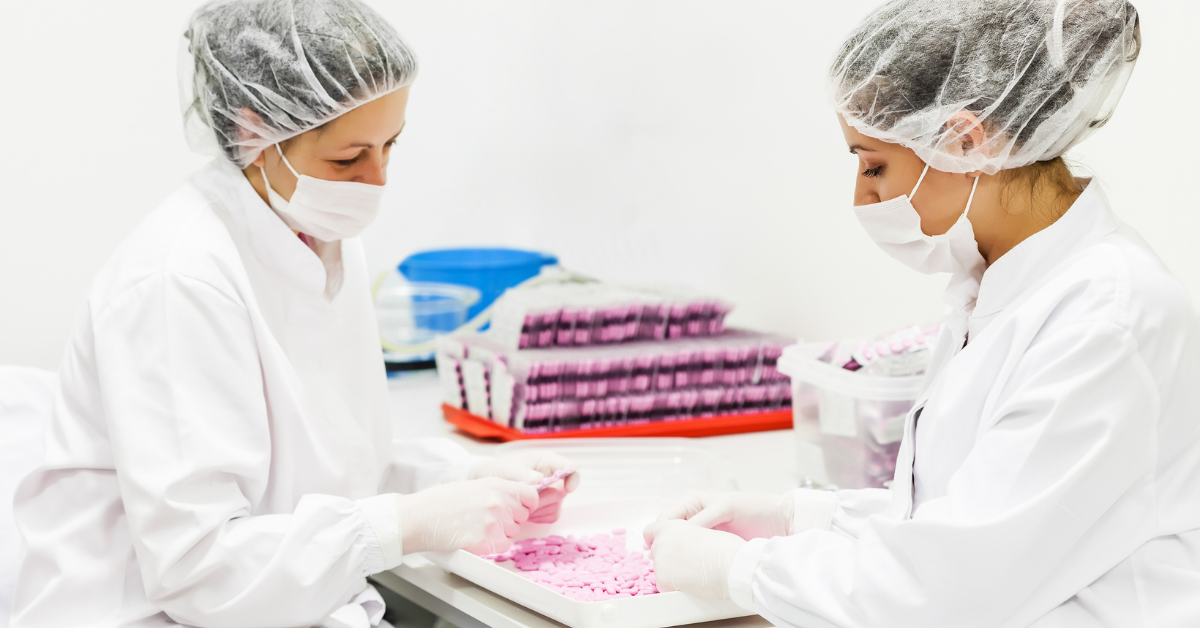
Implementation of a good Root Cause Analysis System will reduce pharmaceutical errors and strengthen your outcome of root causes. Mark Paradies was forwarded a letter a few years ago about American and Canadian Standards Boards with certifying bodies rejecting pharmaceutical quality incident reports because of poor root cause analysis that stated that 90% of the rejections of reports were due to three types of root causes that were unacceptable:
- Employee Error / Human Error / Operator Error OR anyone else who made an error is not an acceptable root cause – Was the training ineffective? Was the procedure too vague?
- Misunderstood the requirement / Did not know it was a requirement / Our consultant told us this was ok OR any other misunderstandings is not an acceptable root cause. Was the training effective?
- We had a layoff / Mona was on maternity leave / we moved locations / we scaled back production / we are still closing out Wayne’s 40 deviations from the last audit OR most other employee or business conditions are not acceptable root causes They are DIRECT CAUSES.
You cannot stop once you get to these causes. But, wait. Are these all root causes, or are some of them Causal Factors? TapRooT® users know what I’m talking about. TapRooT® will help you find out what happened by developing the SnapCharT® and finding your Causal Factors, take those Causal Factors through the Root Cause Tree® in order to find the root causes and then put your fixes in places so that the problem doesn’t occur again.
Adopt the TapRooT® System to improve your root cause analysis and stop pharmaceutical errors. Start by attending a TapRooT® Course to see what it’s all about. Contact me today for an Executive Briefing to learn more.