Monday Accidents & Lessons Learned: Drilling Deeper into an Unconventional Well
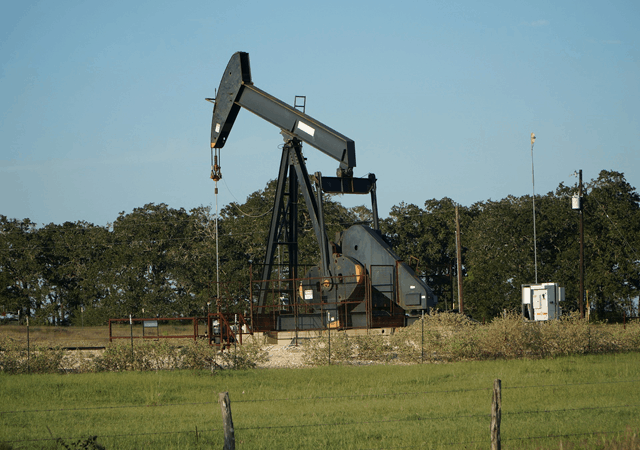
A gas influx in an unconventional well migrated during a BOP test. What are your practices for a flow check before coming all the way out of the hole? Do you ever use a wiper trip to check for swabbing? Are your practices different for tight unconventional wells?
Members of IOGP (International Association of Oil & Gas Producers) allow their personnel, contractors, and other organizations ready access to health- and safety-related information relevant to operations in the upstream oil and gas industry. The narrative below from an IOGP member organization is intended to encourage learning within the industry. Herein, we at TapRooT® share with you to further the dissemination of oil and gas industry safety-related news as most fatal accidents in the oil and gas industry occur due to the lack of proper training and awareness of well control. Please distribute it to interested parties in your company or organization.
Influx from unconventional reservoir with drill string out of hole for BOP test
A well was drilled to 3127m MD and the bit was pulled out of the hole to test the BOPs. After completing the BOP test, the well was observed to be flowing. Due to concerns with being able to bullhead kill the well, a dumb iron BHA with an inside BOP was run in the hole in an attempt to get pipe heavy for stripping operations. Annular stripping commenced at 135m bit depth. At 400m bit depth, stripping was no longer possible due to the uplift force on the string from well pressure. The decision was made to locate a tooljoint under a pipe ram and close the ram to shut the well in and counteract the pipe-light condition. During this procedure, the pipe started uplifting out of the well and the lower rams were closed. The blind shear rams were also actuated to shear the drill pipe and provide an additional well control barrier. Uplift force and friction pressure from the closed lower pipe ram kept the sheared drill string suspended in the BOP. SICP was 3300 psi below the lower pipe ram.
What went wrong?
A tight shale gas play was being drilled below 9-5/8″ casing with 18.0 ppg diesel-based mud. It is suspected that a shallower formation at 2550m MD with some permeability and higher pore pressure allowed gas to slowly migrate into the well while out of the hole for the BOP test. Kick modeling suggests some gas went into solution deep but a considerable amount of free gas migrated higher up in the wellbore before the well was shut in.
Corrective actions and recommendations
While drilling, the circulating ECD maintained adequate overbalance on the suspected feed zone. While tripping out of the hole, the well took the correct of amount of mud. No wiper trip was performed prior to the full trip after circulating and conditioning at 3127m MD. A wiper trip and another bottoms up could have heightened awareness of a possible gas feed in from the zone at 2550m MD with the mud pumps off.
Have you ever worried about confirming and maintaining BOP integrity while managing a well control incident?
With the sheared pipe suspended in the lower pipe ram and the blind shears closed, it was problematic to pressure test and establish that the blind shears had successfully energized the ram seal face. Wellbore pressure on the blind shear rams was a significant concern should the lower pipe rams begin to leak. Only a low pressure test of the closed blind shear ram was possible without risk of “hydraulically pushing” the sheared pipe through the closed lower pipe ram. To address this concern, the annular preventer was nippled down and a high pressure blind ram was installed above the closed blind shear ram for another wellbore barrier prior to bullheading.
Circumstances can crop up anywhere at any time if proper and safe sequence and procedures are not planned and followed. We encourage you to learn and use the TapRooT® System to find and fix problems. Attend one of our courses. We offer a basic 2-Day Course and an advanced 5-Day Course. You may also contact us about having a course at your site.
Join us at the 2019 Global TapRooT® Summit at La Torretta Lake Resort & Spa in Montgomery, Texas, March 11 – 15, 2019. Register Here for the 2019 Global TapRooT® Summit. Learn more about the 2019 Global TapRooT® Summit, and get a preview of all the Summit Keynote Speakers.