Monday Accidents & Lessons Learned: Plane Pushed Into Catering Truck
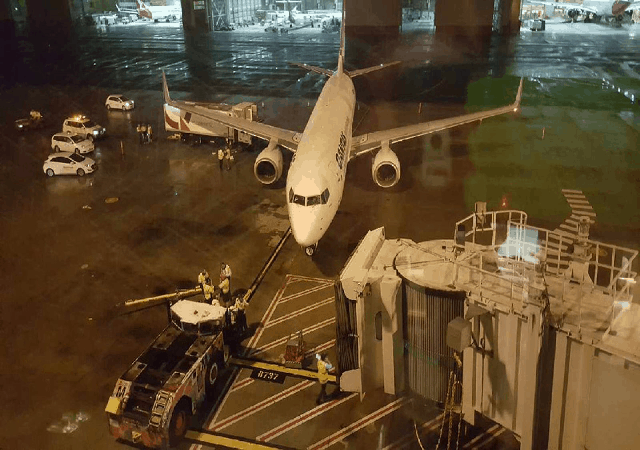
Not all aircraft accidents happen in the air. The Australian Transport Safety Bureau has released the final report on a ground collision in New South Wales. Let’s look at what happened when the aircraft collided with a catering truck on the tarmac of Kingsford Smith airport in Sydney, Australia.
Report summary
On October 14, 2017, the aircraft had been prepared for pushback. An engineer, who had assumed a catering truck was clear of the aircraft, did not visually confirm the path was clear before the pushback began.
When the engineer saw the catering truck was not clear, a few seconds after pushback had started, emergency action was taken to stop. However, the pushback vehicle’s tow bar failed and the aircraft rolled back and collided with the truck. No one was injured. The aircraft suffered damage to the right wing.
This accident illustrates the busy and dynamic environment of airports with various visual limitations. While there is currently no substitute for visually confirming a clear pushback path for an aircraft, aids to support available visual means in the complex environment can help reduce risk.
What happened
At about 6:30 pm (Eastern Daylight Savings Time)[1] on October 14, 2017, the flight crew of a Qantas Airways (Qantas) Boeing 737 boarded the aircraft at Sydney airport, New South Wales, Australia. The aircraft was scheduled to operate a passenger flight to Melbourne, Victoria, with two flight crew, five cabin crew, and 174 passengers.
After boarding, the flight crew found the aircraft had no battery power, as the battery switch had inadvertently been left on. Consequently, another Boeing 737 aircraft, registered VH-VZZ (VZZ) was assigned for the flight. Catering had already been loaded on the originally assigned aircraft so a catering crew (the driver and the marshaller) were tasked to transfer the catering to VZZ.
At about 7:10 pm, a dispatch engineer (engineer) was assigned to the departure of VZZ, which was scheduled for 7:30 pm.
At about 7:21 pm, the engineer arrived at the aircraft, and received a handover from the other engineer who had been in attendance. The engineers discussed the aircraft status under the aerobridge as it had just started to rain. At this time, the catering vehicle (truck) was loading the forward galley through the right forward main entry door (see Figure 1). The pushback vehicle’s (the tug) tow bar was already connected to the aircraft.
Figure 1: Catering truck loading via the aircraft’s right forward main entry door
Source: Qantas, annotated by the ATSB
At about 7:22 pm, the catering crew completed loading the forward galley. They then moved the truck to the right rear main entry door and began loading the rear galley.
The engineer completed his walk around of VZZ and stood under the wing waiting for the catering crew to complete loading. He saw the catering crew close the main entry door and then visually checked that the aircraft door was closed.
The engineer then proceeded towards the front of the aircraft. He put on his headset, which was connected to an external jack point, and contacted the flight crew who confirmed they were ready to depart. As it was still raining, the engineer entered the right side of the tug and sat in its cabin.
Meanwhile, the catering crew retracted the truck’s loading platform and began lowering the truck’s body.
At about 7:30 pm, air traffic control cleared VZZ for pushback, and its captain informed the engineer accordingly.
When the aerobridge had been retracted, the engineer leaned out of the tug cabin and completed a visual check of the left forward main entry door.
At 7:32:23 pm, the catering truck body had finished lowering and the stabilizers began to raise. The crew exited the truck body.
A few seconds later, the flight crew turned on the aircraft’s anti-collision light.
At 7:32:43 pm, the engineer looked left and right from the tug cabin to check for vehicles. He then gave the “thumbs up” signal to the tug driver to commence pushback. When VZZ began reversing, the engineer approved the flight crew to start the right engine. The crew selected the engine start switch and the engine began rotating. The catering truck driver began reversing the truck at this time.
A few seconds later, the catering truck’s marshaller identified that VZZ was moving and tried to alert the truck driver. At the same time, the engineer saw that the catering truck was not clear and “yelled” at the tug driver to stop. The tug driver immediately applied the brakes. The tug stopped but the pins in the tow bar sheared and it separated from VZZ (Figure 2).
Figure 2: The catering truck behind the aircraft’s wing when the tow bar separated
Source: Qantas, annotated by the ATSB
The flight crew heard a loud “bang” and then saw VZZ moving away from the tug. The catering truck was reversing but still 5-7 m behind the aircraft’s right engine so the engineer asked the flight crew to apply the aircraft’s brakes. The captain applied the brakes as firmly as possible. The aircraft slowed but continued rolling back 3-4 m.
At 7:32:53 pm, the aircraft’s right wing collided with the truck (Figure 3) before it came to a stop. The flight crew then engaged the aircraft’s park brake and turned the right engine switch to OFF and the engine wound down as fuel had not been introduced.
Figure 3: Location of catering truck after the collision
Source: Qantas
By 8:12 pm, a new tow bar was connected to VZZ and it was towed back to the bay. No one was injured in the incident and the passengers disembarked. The aircraft was inspected and found to have substantial damage to its right outboard flaps, wing structure between the flaps and aileron, and the aileron (Figure 4).
Figure 4: Damage to the aircraft’s right wing
Source: Qantas, annotated by the ATSB
Operator’s investigation
An investigation of this incident by Qantas included reconstructing the view of the catering truck from the tug’s location (Figure 5).
Figure 5: View of the catering truck (circled) from the tug in daylight
Source: Qantas, annotated by the ATSB
The investigation also reviewed the engineering dispatch procedures. The procedures stated that the dispatch engineer could conduct the pushback from the tug cabin or walking clear of the aircraft and tug. The procedures included the requirement to confirm that all ground equipment was clear of the aircraft, the aerobridge was retracted, the pushback path was clear and all doors and panels were secured and locked. Once those requirements were met, the engineer could then signal the tug driver to commence the pushback.
The investigation also looked at the sequence and the time usually taken for various ground support operations, such as catering and baggage loading. The baggage belt loader was normally the last ground support equipment to clear the aircraft before pushback, and typically that took less than 30 seconds. A catering truck took longer to move clear (as in this case) but was normally clear before the belt loader.
Safety analysis
The engineer made some checks before signaling the pushback to start. He thought the catering truck was clear but did not visually confirm that it was. In part, the engineer’s assumption that the truck was clear was based on the incorrect expectation that the time required for it to move away would be similar to the short time taken by a baggage belt loader. Additionally, the catering truck was not usually the last equipment to move clear.
There were a number of physical reasons why the engineer did not see the catering truck. He did not have his wet weather gear and, as it was raining, decided to sit in the tug’s cabin for pushback. Seated in the tug, the engineer’s view of the truck was largely obstructed by the aircraft’s wing and a panel door (Figure 5). These obstructions were white, the same color as the truck and blended with the small, unobstructed parts of the truck. Additionally, these parts blended into white hangars in the background. The trucks lighting and reflective strips were not in view. The dark and rainy conditions with lights reflecting off the wet tarmac also made it difficult to see the truck.
By the time the engineer saw the catering truck a few seconds after pushback started, it was too late to stop it safely. Emergency action was taken but the tow bar failed, and the aircraft rolled back and collided with the truck. Other than the truck’s marshaller, no one else was in a position, or had the opportunity, to identify the conflict.
Findings
These findings should not be read as apportioning blame or liability to any particular organization or individual.
- The dispatch engineer assumed that the catering truck was clear and did not visually confirm it was before he cleared VH-VZZ for pushback. In part, this assumption was based on an incorrect expectation of the time required for the truck to move clear.
- The engineer’s view of the truck from the pushback tug’s cabin was largely obstructed by the aircraft. The dark and rainy conditions also made it difficult to see the truck, and the engineer saw it too late to prevent the collision.
Safety action
Whether or not the ATSB identifies safety issues in the course of an investigation, relevant organizations may proactively initiate safety action in order to reduce their safety risk. The ATSB has been advised of the following proactive safety action in response to this occurrence.
QANTAS
As a result of this occurrence, Qantas advised the ATSB that it has taken, or proposed, the following safety action:
- Issued a safety information notice to all staff involved in aircraft dispatch activities highlighting the specific visual limitation issues associated with B737 aircraft pushback operations, and the importance of physically ensuring the pushback path is clear.
- Provided relevant training to the dispatch engineer involved in this occurrence.
- The engineering aircraft receipt and dispatch-training package will be revised to highlight the visual limitations and the risks which may be present during aircraft pushback operations.
- Lessons learned from aircraft pushback occurrences will be included in the human factors training program.
- Initiated a trial of cordless headsets to improve visibility during aircraft pushback.
- Conducted an assessment of the risk associated with the engineer sitting inside the tug during aircraft pushback.
Safety message
This accident illustrates the busy and dynamic environment of airport aprons with various visual limitations. While there is currently no substitute for visually confirming a clear pushback path for aircraft, aids to support available visual means in the complex environment can help reduce risk.
The ATSB conducted a study into Ground operations occurrences at Australian airports, which occurred over a 10-year period. Pushback occurrences represented about 26 percent of the total, and the most frequent ones involved tug connection/disconnection. The report concluded that there were a variety of reasons for the occurrences, but the main theme was communication between the dispatcher, flight crew, and pushback tug driver. Communication and a common understanding is vital between involved persons operating in the dynamic environment of an airport apron.
__________
Date: | October 14, 2017 | Investigation status: | Completed |
Time: | 7:32 EDT | Investigation phase: | Final report: Dissemination |
Location (show map): | Sydney Airport | Investigation type: | Occurrence Investigation |
State: | New South Wales | Occurrence type: | Taxiing collision/near collision |
Release date: | November 14, 2018 | Occurrence class: | Operational |
Report status: | Final | Occurrence category: | Accident |
Highest injury level: | None |
Aircraft manufacturer: | The Boeing Company |
---|---|
Aircraft model: | 737-838 |
Aircraft registration: | VH-VZZ |
Serial number: | 39445 |
Operator: | Qantas Airways |
Type of operation: | Air Transport High Capacity |
Sector: | Jet |
Damage to aircraft: | Minor |
Departure point: | Sydney, NSW |
Destination: | Melbourne, Vic. |
Circumstances can crop up anywhere at any time if proper and safe sequence and procedures are not planned and followed. We encourage you to learn and use the TapRooT® System to find and fix problems. Attend one of our courses. We offer a basic 2-Day Course and an advanced 5-Day Course. You may also contact us about having a course at your site.
Join us at the 2019 Global TapRooT® Summit at La Torretta Lake Resort & Spa in Montgomery, Texas, March 11 – 15, 2019. Register Here for the 2019 Global TapRooT® Summit. Learn more about the 2019 Global TapRooT® Summit, and get a preview of all the Summit Keynote Speakers.