Lessons Learned: Long Maintenance Work Period
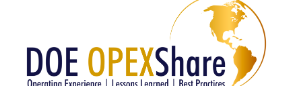
The purpose of having a long maintenance work period is to complete a list of work activities within a short time frame.
Although it is a challenge to complete all the necessary work, it is achievable with proper planning, communication, and teamwork — and, of course, a long maintenance work period.
Discussion: Why have a long maintenance work period?
Each year at the Waste Isolation Pilot Plant (WIPP), an extended maintenance work period is performed. The maintenance period interrupts Transuranic waste shipments and emplacement. Also, it is impactful to WIPP Site operations and generator sites throughout the Department of Energy complex.
On March 28, 2024, an outbrief meeting was conducted to discuss the details related WIPP’s annual long maintenance work period that took place from February 5, 2024, to March 24, 2024.
Over the course of the seven-week period, 146 of the 160 work activities planned and 1,560 work packages were completed. (Note: It was identified that 16 work activities were removed to avoid conflicts with completion of the Waste Station Leveling Project and the upcoming Waste Handling Downloading Schedule.) Activities in the maintenance period included mining to create a dedicated exhaust air route for future waste panels; waste station work at the base of the waste hoist needed due to salt creep; waste hoist motor maintenance and calibration on the Supplemental Ventilation System, Interim Ventilation System, and the 860-series fan system; and several maintenance projects in the Contact Handled Waste (CH) Bay. At the meeting members had the opportunity to share their thoughts about what went well during the maintenance period and what can be improved for the following year. Throughout the meeting, three key factors were mentioned that allowed d the maintenance period to be successful: Pre-planning, Communication, and Teamwork.
Pre-Planning the Long Maintenance Work Period
During the discussion, members communicated that the pre-planning stages were critical to the maintenance period’s success. It was mentioned that the maintenance period schedule was planned by a team six months in advance. The cross functional team was formed by selecting representatives from the following organizations: Radiological Control, Engineering, Safety, Facility Operations, Underground (U/G) Facility Operations, Waste Handling, Hoisting, Mining Operations, Transportation, Work Control, Information Technology, Maintenance, Projects, Training, Environmental Safety and Health, Fire Fighters, Security, and Plant Helpers. Over the six months, the team worked together to ensure work packages and engineering documents were developed, reviewed, and approved. Members did acknowledge that the work packages were of excellent quality because they were provided adequate time to complete them without feeling schedule pressure.
Additionally, the time allocated prior to the maintenance period helped members to strategically plan and coordinate the work activities. It was noted that the first week was loaded heavily to allow for activities to flow into the following week (if needed) and that higher risk jobs were planned in the later weeks. Members stated that this was the best approach to building the schedule based on previous successes.
Overall, the efficient pre-planning allowed everyone involved to prepare work packages and preventative maintenances (PM) before the start of the maintenance period, resulting in a productive maintenance period with minimal delays.
Communication
Effective communication was essential to the maintenance period’s success. Briefings were given in several weekly/daily meetings like the morning escalation meeting and the Facility Shift Manager daily planning meeting. The purpose of the briefings was to update everyone about the scheduled activities and potential delays that needed to be addressed. The scheduled activities were documented in the 2024 Long Maintenance Work Period Tracker. The tracker provided information related to the Scope of Work, department work activities, areas affected/plant configuration, scheduled dates, current statuses, and competition dates. If there were any updates or changes to the tracker, it was communicated to the workforce during the meetings. Workers expressed that continuous communication allowed them to be aware of their roles and responsibilities and helped them to adjust to any necessary modifications to the schedule.
Teamwork
Collaborative efforts between the supporting organizations allowed the maintenance period to run safely, compliantly, and efficiently. Many members commented that it was the best maintenance period because of the strong teamwork. For instance, personnel utilized others’ knowledge and expertise to tackle challenging tasks. Also, through the maintenance period, individuals became familiar with the supporting organizations roles and responsibilities which in turn, built camaraderie.
Since they gained an understanding of one another, they came together as a team to accomplish the various work activities. Additionally, working groups were committed to staying on track with the schedule and were willing to work overtime, if needed.
Gratitude was expressed to the employees who worked together to ensure that the tasks were finished in accordance with the maintenance schedule.
What Can Be Improved?
Participants highlighted many positives about the maintenance period, but they also shared their thoughts about what can be improved next year such communicating changes and having additional support.
Communicating Changes
During the maintenance period, some changes to the schedule were not clearly communicated to supporting organizations. For example, because certain working groups completed their tasks earlier than expected, it was decided to push up the scheduled work activities of other groups. The groups whose work schedules were altered, felt frustrated and overwhelmed with the workload. The amount of time they thought they had to complete their LO/TOs, walkdowns, etc., was now rushed because of the changes. To mitigate this issue for next year, contingency plans for work activities will be planned and approved. Therefore, if work groups finish their tasks, they can begin completing the next set of tasks that do not impact other working groups or facility conditions. Additional Support: Workers experienced issues related to power generators. For instance, many power generators simultaneously shut down, resulting in buildings without light or heat. To prevent this issue from occurring next year, it was advised for power generator PMs to be finished before the maintenance period and to have a backup supply of generators in the event multiple generators quit functioning. Also, since power generators are not consistently used, there will be system health checks designated to Subject Matter Experts to ensure the generators are in good condition and function properly so that they supply sufficient power for the designated working groups and/or buildings.
Conclusion
The meeting concluded that pre-planning, communication, and teamwork played pivotal roles in creating a successful long maintenance work period. Although there were some minor delays in the schedule and miscommunication of work activities, the members were overall pleased with the results. Overall, the WIPP team’s dedication to the mission allowed them to accomplish majority of the planned tasks while keeping safety at the forefront.
RECOMMENDATIONS
- Utilize Contractor Assurance personnel to publish information shares weekly via various communication outlets. The information shares will provide updates about the maintenance period and what improvements need to be made for the following weeks to help mitigate/reduce potential delays.
- Ensure PMs are completed prior to the maintenance period for equipment that is not consistently used.
- Prepare contingency plans for working groups that complete tasks ahead of the schedule.
Content/image credit/source: This Lessons Learned, “LONG MAINTENANCE WORK PERIOD AT THE WIPP SITE,” is from DOE OPEXshare, Dept. of Energy, published 4/15/2024.
Would you like to become TapRooT® Trained? Register for a TapRooT® course to put yourself on the best career path to skills development and effective training in troubleshooting to identify the root causes of issues and incidents.
TapRooT® Trained professionals have the training and skillsets necessary for investigation, problem-solving, and root cause analysis.