Influx following failure of reservoir isolation device
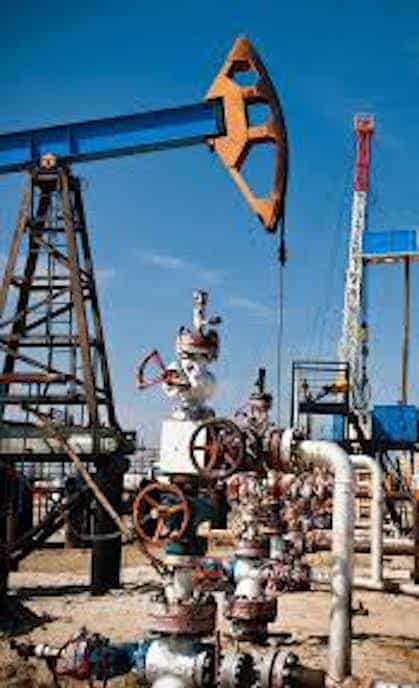
A hydrocarbon influx was taken when a reservoir isolation device failed during the displacement of a well to packer fluid
• • •
On a subsea well, the lower completion—including a pressure-actuated reservoir or formation isolation device (RID / FIV)—had been installed. The upper completion was also run, the tubing hanger successfully landed and tested, and the well was being reverse circulated, down the annulus and up the tubing, to underbalanced packer fluid prior to setting the production packer.
During the displacement, an increase in gas trends was observed in the fluid returns. Monitoring of the well was switched to the trip tank and increasing volume was observed; the well was flowing. Displacement to packer fluid was stopped and the well was bullheaded confirming that the reservoir isolation device had failed. The reservoir isolation device had been previously tested to 4,000psi and was planned to only be opened once the upper completion had been run and the production packer set.
Overbalanced brine was bullheaded down the tubing, the upper completion production packer was then set, and the well controlled.
What went wrong?
The root cause is believed to be the failure of the reservoir isolation device either due to a manufacturing or materials defect or due to the pre-job preparation of the valve’s pressure cycle count.
Other possible failure options that were considered but have been ruled out following investigation include:
- Lower completion packer leak.
- Accidental pressure cycling of ‘half-cocked’ reservoir isolation device causing the valve to jump cycles.
- Accidental cycling of the valve during transportation or gravel pack operations.
- Nitrogen quality, pre-charge pressure, or leak.
- Inadvertent mechanical shifting of the valve.
Corrective actions and recommendations
The well’s primary barrier element failed, and it was only the crew’s attentiveness and subsequent courage to take action that prevented this well control incident from becoming much worse.
The following recommendations specific to reservoir isolation devices have been adopted:
- Increase QA/QC level during onshore preparation of reservoir isolation devices.
- Ensure full understanding of how pressuring cycling on reservoir isolation valves can cause the valve to inadvertently jump cycles.
- Perform a low-pressure test of reservoir isolation device after the last known high-pressure test to ensure the valve is not prematurely cycled open prior to installation of completion.
The incident in this blog post is shared from the Well Control Incident Lesson Sharing System of the International Association of Oil & Gas Producers. IOGP Well Control Incident is IOGP WCI Lesson-Sharing 20-4.
Founded in 1988, the TapRooT® Root Cause Analysis System solves hurdles every investigator faces
TapRooT® Root Cause Analysis Training System takes an investigator beyond his or her knowledge to think outside the box. Backed with extensive research in human performance, incident investigation, and root cause analysis, TapRooT® is a global leader in improved investigation effectiveness and productivity, stopping finger-pointing and blame, improving equipment reliability, and fixing operating problems.
System Improvements, the creator of the TapRooT® System, has a team of investigators and instructors with years of extensive training providing assistance worldwide. We also offer ongoing support to our clients through free newsletters and root cause tip videos, the root cause analysis blog, and our annual Global TapRooT® Summit.
Our staff and technical support team are here for you. Feel free to connect by phone (MAIN: 865.539.2139; SUPPORT: 865.357.0080) or email.