Improving Patient Safety By Using FMEA and TapRooT® RCA to Proactively Analyze a Process
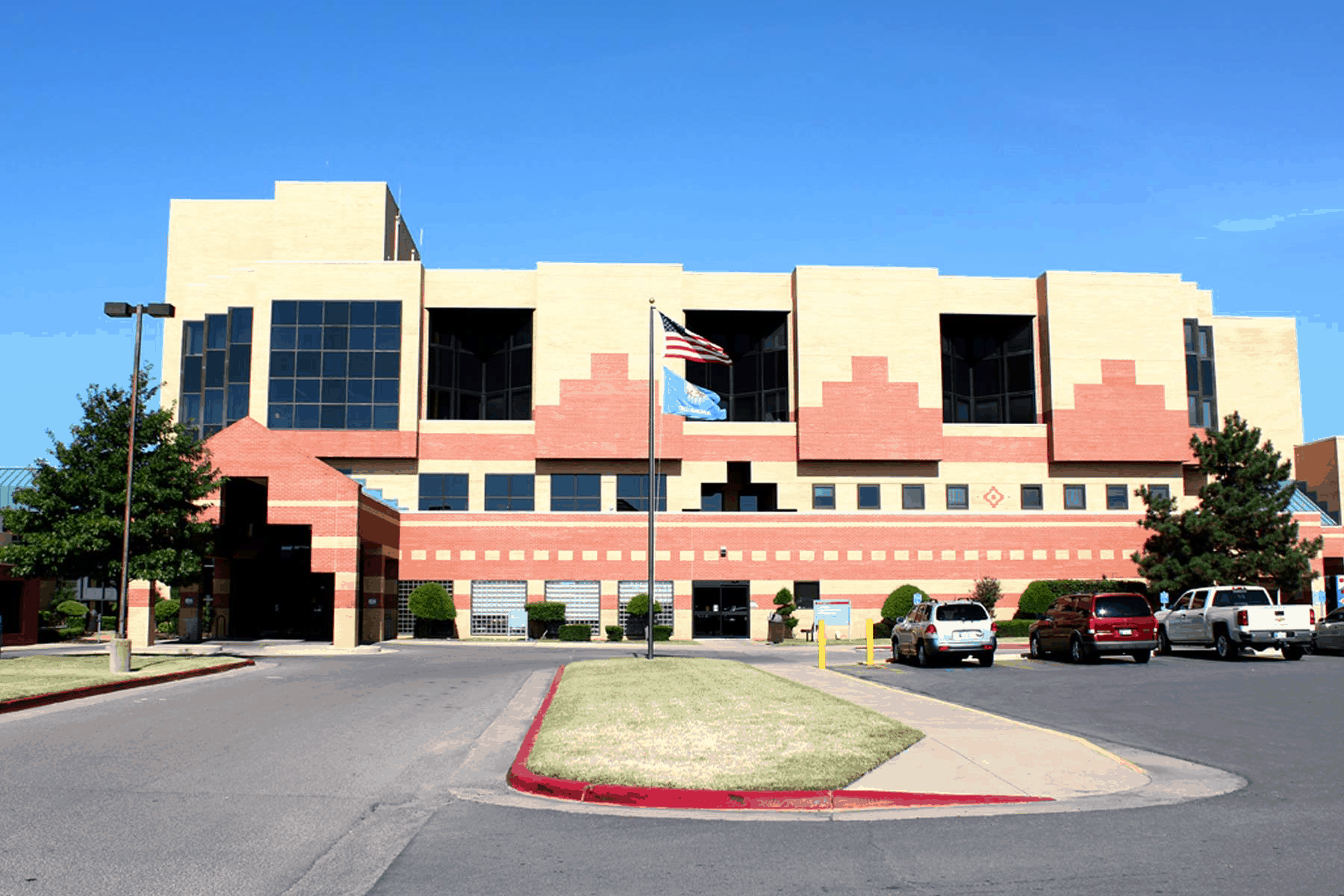
Improving Patient Safety By Using FMEA and TapRooT® RCA to Proactively Analyze a Medication Administration Process
Submitted by Julia Campbell,
Nursing Unit Administrator,
Jackson County Memorial Hospital
This success story was written in the past and is being updated to our most recent blog article format and is being reposted here. The example shows how TapRooT® Root Cause Analysis (RCA) can be used in a healthcare setting to proactively improve patient safety. The lessons learned from this success story apply today more than ever and should be shared across healthcare facilities that need to improve patient safety.
Challenge
Our challenge was to further improve the medication administration process at our facility by proactively analyzing the process using FMEA and TapRooT®.
Our goal was to find ways to help prevent errors and increase patient safety by identifying error-prone points in the system and anticipating what might cause these failures so they could be eliminated or minimized whenever possible. The medication administration process had already been reviewed for ways to decrease medication errors and increase patient safety. Therefore, we were starting with a system that many people thought might not present easy improvement targets.
A practical constraint to our efforts was that because of the fiscal constraints that all healthcare facilities face in these days of tight budgets, we knew it would be difficult to make large capital investments. Therefore, complex or costly systems for automation of the medication administration process were not a possibility. However, we thought that by the use of systematic evaluation tools – FMEA and TapRooT® – we might find ideas for improvement that others had missed.
Action
We formed a core team of nurse managers and pharmacists to analyze the process. As the analysis progressed, others were asked to help where they had a better working knowledge of the process in a particular area. Each of these team members had been trained to use of TapRooT® (TapRooT® has been used at our institution for the last 5 years).
We started by diagramming the process using a SnapCharT® Diagram using the TapRooT® Software. This helped the team visualize the whole process and break it down into manageable pieces for further analysis.
As we performed the FMEA for various parts of the process, familiarity with the TapRooT® System’s Root Cause Tree® helped team members ask better questions and identify potential failures that they may not have thought of without the TapRooT® Training. The TapRooT® Training also increased the team’s awareness of how problems at a particular unit might be generic (applicable to the whole organization).
Once the team had identified problems and their root causes, it was time to develop corrective actions. This is where the training that we had received at the TapRooT® Course about developing “SMARTER” corrective actions came in. As we looked for ways to improve, we considered the caregivers and what it takes to provide that care. We made sure that Safeguards that we put in place to improve patient care didn’t actually introduce new types of errors by making the process too complicated or difficult to follow. Therefore, each corrective action was reviewed (the final “R” of SMARTER) to make sure that there were not any unintended negative consequences from the proposed improvement.
Results
How did we improve our medication administration process to improve patient care? Here are some of the ideas that we implemented:
- Medication carts ordered for the bigger units that will enable medications to be prepared closer to the patient decreasing distractions.
- Medication references easily accessible at the point of administration and pharmacy phone numbers posted bold and bright encouraging communication and questions.
- Rearranging of floor stock medications in smaller units where storage is a problem.
- Changing labels where labeling was not clear in some areas.
- Chemotherapy administration sequence references made readily available.
- Standardize transcription on the major units to decrease transcription error potential.
None of these changes look like a radical departure from our old practices. None of the changes were extremely expensive. But people involved in the analysis believe that the changes address issues that could have caused errors and had previously been overlooked in our improvement efforts. Therefore the analysis was both useful and worthwhile.
Our institution has a strong commitment to the continuous improvement of patient safety and the quality of care. Use of systematic tools – like TapRooT® and FMEA – helps us recognize the potential opportunities for improvement proactively.
As a healthcare professional, I feel that this proactive approach (instead of waiting for accidents and analyzing the failures after the fact) allows us to manage our processes and provide better care. We aren’t victims of the system with no control to change or improve things. We can systematically analyze, manage, and improve our processes. And TapRooT® is a key part of that proactive analysis and improvement process.