Improving Investigations to Provide Management with the Information They Need to Support Corrective Actions
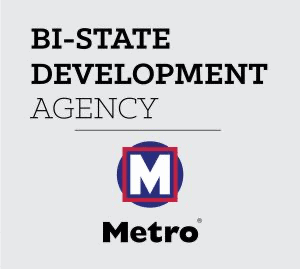
Using TapRooT® Root Cause Analysis to Improve Investigations and Provide Management with the Info Needed to Support the Corrective Actions
Success Story Submitted by Pamela McCombe, Manager, Bus and Rail Safety at the Bi-State Development Agency
This success story was written in the past and is being updated to our most recent blog article format and reposted here. The example shows how TapRooT® Root Cause Analysis can help improve incident investigations and help management understand and support the corrective actions needed to improve performance. This success story applies just as much today as it did when it was written.
Challenge
The Bi-State Development Agency is a progressive rail and bus transit system whose service area includes metropolitan St. Louis, Missouri, and expands over the Mississippi River into St. Clair County, Illinois.
In December of 1998, I became the Manager for Bus and Rail Safety. In discussions with the new Executive Director, one of my challenges became clear … I needed to improve the investigation and reporting of accidents so that management would have the information they needed to improve performance and support effective corrective actions.
Before my arrival, a member of the Safety Department would go to the scene of an accident and, within four hours, write a “Fact Sheet” (a boilerplate consisting of the events leading up to the accident and the response efforts). Management recognized that this method of investigation was not providing the information needed to develop effective corrective actions.
Action
Fortunately, I already had a plan.
I had previously used TapRooT® Root Cause Analysis to improve investigations and I knew how fast it could work to improve investigations and corrective actions. So, I introduced TapRooT® RCA as the Safety Department’s investigative tool and sent our investigators to TapRooT® Training.
Result
Within weeks of instituting TapRooT® Root Cause Analysis as the primary investigative tool, we had dramatically improved the investigation of accidents. The Safety Department drew SnapCharT®s as part of the investigation and used the charts to explain what happened to management. We also used the TapRooT® Root Cause Tree® to consistently identify the accidents’ root causes. These two techniques helped us understand the details of what happened and look much deeper into the system causes that needed to be corrected.
Of course, this was much more difficult than just blaming the driver. But the effort is very worthwhile. The Safety Department can now answer questions as to why human error or mechanical failure occurred. Upper management was pleased with the wealth of knowledge gleaned from the TapRooT® System. People that I hardly knew were stopping me to say that the reports were much more informative and that now they now understood Safety’s role in accident investigations.
Using TapRooT® RCA, our department provides an unbiased resource to dig into the factors that caused the accident, find the system causes, and recommend effective corrective actions. Since implementing TapRooT®, the Executive Director praises our accident reports saying that they “now add value in terms of reducing accidents and improving the way Bi-State does things.”
Our next challenge is to ensure that the corrective actions are implemented quickly and documented when completed. But with upper management’s support for problem investigation and rapid implementation of corrective actions, I’m sure our efforts will be successful and that we will have even more impressive successes to report in the future.