How Much Money Can TapRooT® Root Cause Analysis Save Your Company?
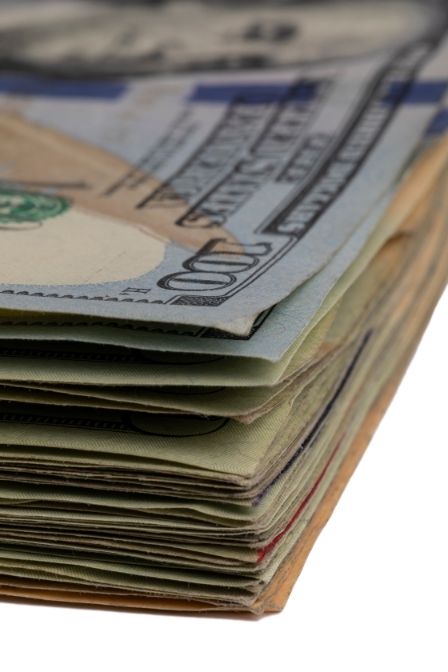
Example of Money Saved
One of the students in a 5-Day TapRooT® Advanced Root Cause Team Leader Course came up to me on the third day of the course and told me that the course had already paid for itself many times over.
I asked him what he meant. He said while we were teaching that morning, he used the information he learned in the course to spot a problem in some engineering work they were doing. He immediately called his office, and they fixed the problem. The savings they achieved totaled over $1 million dollars.
That’s a great return on investment. A $2500 course and a $1,000,000 payback.
That’s about a 40000% instant ROI.
What is Your ROI?
That made me think …
Do TapRooT® Users think about how much they are saving their company?
Do they track the savings?
Do they know how much problems cost their company and have a cost-saving goal?
If you are a TapRooT® User, how much money have you saved your company? How many lives have you saved?
Here is a TapRooT® Success Story about another site that saved a bundle:
Let me know if you have a Success Story involving saving money for your company by leaving a note below…
I have a huge concern with this “testimonial.” One of the most common failures with engineering projects in general, and with most continuous improvement initiatives, is failure to effectively and consistently capture and report results. These are the results that validate the project investment and are the greatest measure of project success. In your example a hypothesis was generated, a call to the “office” was made, and a 4,000% ROÍ was ascribed on that same day. I do not see how this savings could possibly have been validated in this timeframe.
At the very least the engineer should have been advised to validate the savings subsequent to project commissioning and you should not have advertised this “testimonial” before that happened.
Thanks, Mark,
You are right; this wasn’t the most rigorous calculation. His was a comment at a course. It was meant to be an example, not a case study.
However, changes in design engineering can prevent many errors that cost terrific amounts of money during operations and maintenance. But in this case, the error prevented was in the engineering, and the savings were in engineering costs. But for the example, that really doesn’t make much difference
Another example that won’t pass your standards check was an engineer in a course that recognized that he had put a pump start button in a confined space and that people were starting the pump without using a confined space procedure. He had the button moved to a more convenient location outside the confined space. What were the savings there? A life? Had to say.
I would guess that most sites don’t know the cost of human errors. Maybe this article will get people to think about the cost of errors and start calculating at least a guess on the savings possible.
Best Regards,
Mark