How Do You Measure the Goodness of a Root Cause Analysis?
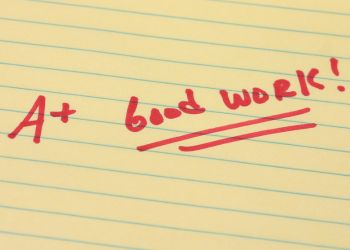
Are Your Analysts Producing Good Root Cause Analyses?
I had someone ask me:
“How do you know if a root cause analysis is good?“
Of course, my first thought was that a good root cause analysis prevents repeat incidents.
But some incidents are infrequent, so you might not know about repeat incidents for years.
Also, you would like to think that a good root cause analysis would prevent similar incidents. But how similar is a difficult question to answer.
But I had a second answer to knowing if a root cause analysis is good. Read on for my second answer.
Grading Root Cause Analyses
In the late 1990s, I was asked how management could tell if a root cause analysis was adequate. I came up with a systematic process for grading a root cause analysis. It could produce a score of 0-100 and a letter grade. I wrote about it HERE.

A portion of a grading sheet is shown above. It explains the various grades of the RCA goodness.
The first column is the factors used to grade the root cause analysis.
- Complete, accurate timeline of what happened has been documented.
- All causal factors are identified.
- Root causes with supporting evidence are accurately identified for each causal factor.
- Generic causes are identified for each causal factor (if applicable).
- Effective corrective actions are proposed for each specific root cause for each causal factor.
- At least one proposed corrective action is appropriately high enough on the hierarchy of safeguards list.
- Effective corrective actions for generic causes. (If generic causes are identified. Rate at 100 if generic cause analysis is either deemed unnecessary or if no generic causes were found.)
- Corrective actions are specific.
- Corrective actions are measurable.
- Corrective actions are assigned to individuals with the authority and budget to implement them.
- Corrective actions are reasonable (cost-justified).
- Corrective actions have a prompt due date based on their risk mitigation potential.
- Corrective actions have been reviewed for unintended consequences, and no serious shortcomings have been identified.
- Management reviewed the root cause analysis and has accepted it. Management has approved the corrective actions.
- Management has a system to track and manage the implementation of corrective actions.
These criteria are explained in the second column. If you don’t understand the criteria explanations, you probably have not attended TapRooT® Root Cause Analysis Training. See this LINK for suggested courses.
If you meet these criteria, you should prevent future incidents by implementing the corrective actions developed during the root cause analysis.
The first version of the grading system was an Excel spreadsheet. However, we went even further by building the grading system into the TapRooT® Software Version VI (that grading system is shown below).

These systems were tested by independent members of the TapRooT® Advisory Board and found to be quite useful.
How Does Grading Help?
First, it gives management confidence in the quality of the root cause analysis.
Second, if the analysts know the criteria, they can produce better root cause analyses by having an objective.
Third, if you give the analysts feedback from a peer review committee of experts that use the criteria to grade investigations, they will know how their judgment compares to the experts. This feedback should produce even better root cause analyses.
Finally, the experts become even better during discussions of the analyses that they grade.
Most Important Use of the Grading System – Coaching
Using this system, it is easy to explain to investigators what they need to do to improve their investigations.
For example, if the first factor, “Complete, accurate timeline of what happened has been documented,” is rated as a 75 (a C), the coach can explain how the SnapCharT® needs to be improved to get a better grade (an A or a B).
This makes feedback very specific and actionable.
The best way to give this feedback is in “real-time” during the investigation as each phase of the investigation is being completed. In that way, errors are corrected, and improvements are made BEFORE going to the next step.
Start Grading Your Root Cause Analyses Now!
Those who have implemented grading as part of their root cause analysis system have seen measurable improvements in their investigations of safety and quality problems. You can, too.
If you are a TapRooT® Software User, you already have the system built in.
If you want to discuss using the grading tool, contact your TapRooT® Implementation Advisor by calling 865-539-2139.

(The above figures and rating systems are copyrighted © by System Improvements, Inc. They are used here by permission. Duplication is prohibited.)