Food & Beverage Industry: What Are You Investigating?
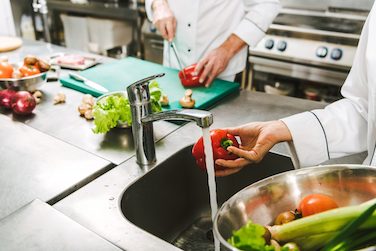
For world-class companies, figuring out “What are you investigating?” is an important step in their improvement journeys.
Some pursuits of “what are you investigating?”are obvious: Serious injuries, reportable environmental releases, and large fires are obvious targets. For the Food and Beverage industry, your company doesn’t have a lot of these! So where do you concentrate your improvement efforts?
There are lots of ways to determine this. A list to catch all the factors of “what are you investigating?” might look something like this:
- Anything reportable to regulators
- For example, required to be reported to the Reportable Food Registry;
- Recalls;
- Anything that stops production for more than a predetermined amount of hours;
- And of course, reportable OSHA issues.
But, there are also more subtle problems that you might want to investigate:
- Repeat customer complaints;
- Public issue damaging to your reputation (even if it seems like a minor issue internally);
- Supplier problems causing product quality issues;
- Quality rejection of a production batch;
- Repeat equipment failures.
To be clear, the tasks of “what are you investigating?” is both overarching and detailed.
All of these types of issues should be investigated. We want to make sure we are fixing not just the high-visibility items, but those precursor issues that could lead to more major problems in the future.
Additionally, we want to ensure that, when we address these types of problems, we aren’t focusing on individual people. We want to correct the system problems that are preventing our team from performing at their best.
These types of issues are exactly what TapRooT® Root Cause Analysis was designed to help you understand and fix — with a focus on the human performance issues that will make long-lasting improvements to your company.
Let us know if you would like to see exactly how TapRooT® can help. I will be happy to set up a short demo of the TapRooT® System, showing you how easy it is to use and how effective the process is at identifying human performance-based root causes.
TapRooT® wins food safety software award
We are excited to share that System Improvements, Inc., creator of the TapRooT® System, is recognized as a top food safety solution provider by Food & Beverage Technology Review.

TapRooT® helps food and beverage companies get to the root causes of food safety issues as well as improving industrial safety in the production facilities.
Read more here about TapRooT® and food safety.
Register for a TapRooT® Root Cause Analysis Training Course
TapRooT® Root Cause Analysis Training courses are taught all over the world. If you are interested in learning how to stop repeat incidents, find a 2-day or 5-day course. We are available to train you and your staff on-site at your workplace; contact us to discuss your needs. You may also call us at 865.539.2139.
Sign up and bring your team to the 2022 Global TapRooT® Summit
Register now to join us in beautiful Knoxville, Tennessee, near the incredibly picturesque Great Smoky Mountains National Park. The 2022 Global TapRooT® Summit is May 2-6, with Pre-Summit courses happening May 2-3 and Summit sessions are May 4-6.