Firefighting Chemical Spill – Finding the Real Cause
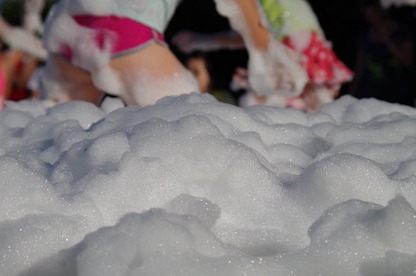
In May, the Navy released a report discussing causes of a chemical spill — Aqueous Film Forming Foam (AFFF) — at Red Hill Storage Facility near Pearl Harbor, Hawaii.
The chemical spill released over 13,000 gallons of AFFF.
The Navy report on the error(s) that led to the chemical spill stated, “The deputy commander of the U.S. Army Corps of Engineers blamed the Nov. 29, 2022, on two factors. First, a maintenance contractor hired by the Navy improperly installed an air vacuum valve during a temporary modification to the AFFF fire suppression system at the Red Hill facility in April 2022. Second, employees from that same company failed to disable the AFFF pumps from automatically starting prior to running tests on the fire suppression system.”*
I quickly noticed the words in the report, “final verdict”: “The bottom line is that this mishap was caused by human error, and it was preventable.”
Unfortunately, when maintenance errors occur, this is often the immediate response.
These types of rapid assessments show that a human-performance based analysis was not performed. The corrective actions will be blame-oriented. In fact, another statement in the article reads, “The Navy needs to act now to hold people accountable for this spill and ensure that its continued work to remediate and close Red Hill meets the standards of quality and safety that the people of Hawaii deserve.”
This is the typical response when we are more interested in looking for a scapegoat rather than truly understanding the reasons these errors were made.
I’m confident the contractors did not go onsite that day and decide to cause an environmental spill. They were doing their jobs, and errors were made, but unless we understand the reasons for the mistakes, the corrective actions will most likely not prevent similar occurrences in the future.
*Source content/credit: Spectrum News, “Navy announces findings from investigation into AFFF spill,” by Michelle Broder van Dyke, May 6, 2023.
Equifactor® Equipment Troubleshooting and TapRooT® Root Cause Analysis Training
Do you need to efficiently and effectively find the root causes of equipment failures to improve your facility’s equipment reliability? Imagine the downtime prevented, and money saved NOT having repeat equipment failures. If this sounds interesting (and worthwhile), then this completely revised TapRooT´® Equifactor® course is for you.
The Equifactor® Techniques are based on the work of noted equipment reliability expert Heinz Bloch. The tools can be used by maintenance personnel, equipment reliability specialists, maintenance managers, or investigators who don’t have an extensive understanding of equipment engineering.
Circumstances can crop up anywhere at any time if proper and safe sequence and procedures are not planned and followed. We encourage you to learn and use the TapRooT® System to find and fix problems.
TapRooT® has a team of investigators and instructors with years of extensive training ready to offer assistance worldwide. We also offer ongoing support to our clients through free newsletters and root cause tip videos, the root cause analysis blog, and our annual Global TapRooT® Summit.
Register for one of our TapRooT® courses. We offer a basic 2-day course and an advanced 5-day course. Contact us or call 865.539.2139 about having a course at your site or for further root cause analysis opportunities. We’re here to find solutions for you.