FDA Warning Letters, CAPA, and Root Cause Analysis
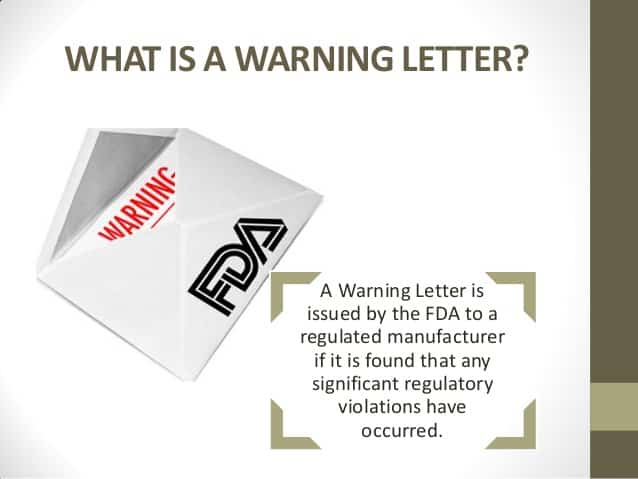
About 50% of FDA warning letters include CAPA failures. This isn’t a new trend. CAPA failures show up year after year in FDA warning letters.
When you think about it, there must be something wrong with the CAPA systems being used by a large number of pharmaceutical companies.
Here are three ideas to think about when evaluating the potential reasons for your companies’ CAPA failures…
1. Bad Root Cause Analysis.
“Lack of knowledge … that is the problem.
You should not ask questions without knowledge.
If you do not know how to ask the right questions,
you discover nothing.”
W. Edwards Deming
Some common root cause analysis tools applied in CAPA process at pharmaceutical companies just don’t work very well. These common techniques include 5-Whys, Fishbone Diagrams, and Brainstorming. Want to learn more about why these techniques fail so frequently? Read these articles:
Root Cause Analysis Tip: Why Did The Robot Stop?
What’s Fundamentally Wrong with 5-Whys?
Quality Progress: A Critical Look at Root Cause (Page 32)
Dunning-Kruger Effect – Another Reason You Need TapRooT® Root Cause Analysis
Lean, Six Sigma, and Lean-Six Sigma –
What Do They Need to Advance into the 21st Century?
That’s a good start understanding what’s wrong with what many companies are doing for root cause analysis. But what can they do to improve? We will discuss that AFTER we look at two more problems that companies have.
2. Developed Bad Corrective/Preventative Actions.
“We Can’t solve problems by using the same kind of thinking
we used when we created them.”
Albert Einstein
Even if your company identifies true root causes, we have often seen people fail to develop effective corrective actions. Why? Because they don’t have the knowledge needed to develop effective corrective actions for human error related root causes. Therefore, they fall back on the “Standard 3” corrective actions:
- Training
- Discipline
- Procedures
Although these types of corrective actions may be needed occasionally, they are overused. Often they are used when they won’t be effective.
How do you solve this problem? Keep reading. We will discuss that after we describe the final problem.
3. Didn’t Follow-Up/Implement Corrective/Preventative Action
One of the saddest CAPA program failures is to watch a company find root causes and develop corrective actions BUT they are never implemented.
You must track corrective/preventive actions to make sure they are implemented.
Management has to be interested in the implementation and provide the necessary resources.
A follow up audit to make sure that the corrective/preventive actions are effective and the results should be documented.
– – –
So, how do you solve these types of problems?
FIRST, you adopt advanced root cause analysis – TapRooT® – to analyze the root causes of quality issues.
SECOND, you use the Corrective Action Helper® Guide and other corrective action tools in the TapRooT® System to develop effective corrective actions based on human factors and equipment reliability best practices.
THIRD, you use the corrective action tracking portion of the TapRooT® Software (or any corrective action tracking software you have) to track corrective action implementation,verification, and validation.
Want more information about how the TapRooT® System can help you improve quality and your CAPA System? CONTACT US and see these links:
https://www.taproot.com/solutions/pharmaceuticals/
https://www.taproot.com/what-makes-a-great-root-cause-system/
And get information about our training and software here: