FDA Issues Warning Letter to Food Processor – Need Better Documentation of Root Cause Analysis and Corrective Actions
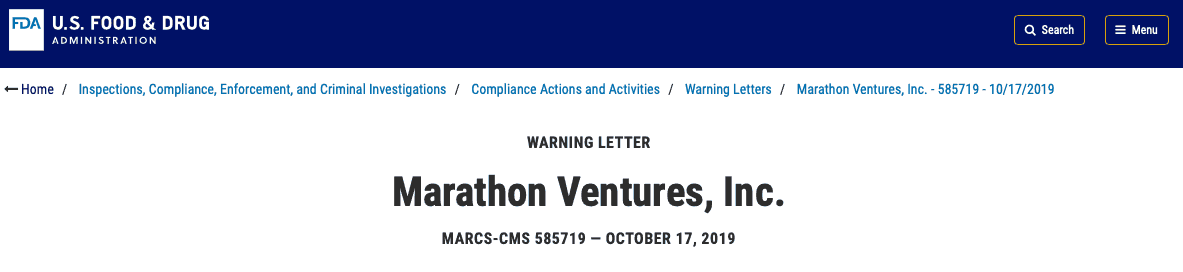
FDA Warning Letter
Food Safety News reported that the FDA had issued a warning letter on October 17, 2019, to John Larsen and Michael Sortino, co-owners of Marathon Ventures, Inc., after finding evidence of Listeria monocytogenes in their food processing facility in Bellvue, Nebraska.
The letter is quoted as saying:
“Your written corrective action procedure for your “Environmental Microbial Sampling SOP,” issued 3/19/2019, states that ‘(b)(4).’ However, between April 2019 and May 2019, you identified five positive environmental samples of L. monocytogenes, and you do not have records to show that you conducted an investigation of the potential source or cause of contamination.”
“Your responses indicate that state that although you did not document the root cause of the positive L. monocytogenes samples, you had performed a root cause analysis for each sample that tested positive for L. monocytogenes. However, your written response and “Environmental Microbial Sampling SOP,” issued 7/12/2019, do not address how you will ensure employees will document the corrective actions and investigations when there are positive environmental test results in the future. We will evaluate the effectiveness of your program during a future inspection.”
What Would a Good Root Cause Analysis Include
A good root cause analysis would include documentation of what happened to cause the contamination, the Causal Factors that led to the contamination, the root causes of each Causal Factor, and the corrective actions developed and implemented to prevent future contamination. This would be documented for each time contamination is identified.
After a good root cause analysis, one would expect that future problems would be prevented by the corrective actions and Generic Causes would be addressed to prevent similar causes of contamination in other parts of the facility.
Results of Good Root Cause Analysis
The best proof of a good root cause analysis, besides thorough documentation, is the prevention of future similar incidents. Repeat contamination and findings of contamination during follow-up regulatory inspections is an indicator that either the root cause analysis was not thorough and effective and/or, the corrective actions did not effectively address the root causes, and/or the corrective actions were not effectively implemented.
The results of good root cause analysis have been shown in all types of manufacturing facilities including those regulated by the FDA. Implementing good manufacturing practices and taking action by performing a thorough root cause analysis and implementing effective corrective actions should prevent warning letters from the FDA.
Learn How To Perform an Effective Root Cause Analysis
System Improvements has been teaching effective root cause analysis for the past 30 years. If you need to improve the effectiveness of your root cause analysis to help you prevent future FDA warning letters, register for one of our upcoming public TapRooT® Root Cause Analysis Courses being held around the world. See our list of upcoming courses at:
https://store.taproot.com/courses