Equipment Used to be Reliable
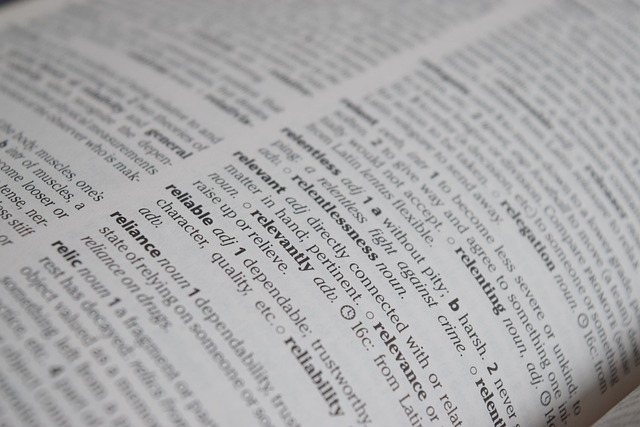
The 1980’s Mercedes 300 series routinely logged 1,000,000 (yes, that’s a million) miles on the original engine — I suppose you could call that reliable.
Remember talking about equipment being reliable — “They don’t make ’em like they used to, right?” Equipment doesn’t work anymore, and we’re doing voodoo gymnastic rocket surgery to keep even modern machines running. So how do companies keep their machines running? Reliability departments, IOT, vibration monitoring, oil analysis, and predictive systems are used at best-in-class companies. The practices are what separate world-renowned companies from their competitors. Unfortunately, the biggest reliability problems companies face are at the opposite end.
Modern vs. Classic
Are modern machines under more stress? I say no. We used to be MEAN to our equipment. So why do we have to baby, nurture, and give our modern equipment some TLC to even receive an ounce of reliability? To answer the question above, “No, modern machines are not under more stress.”
So, what happened?
Let’s take a look at an example…
A Ferrari and a Geo Metro can both suffer from reliability issues. A Ferrari is designed without cost analysis in mind and is subject to tremendously high stress and high-performance conditions. This is vastly different from the Geo Metro. The Geo Metro was designed to meet minimum design standards and move a human being between locations at minimum cost. Even though both cars were designed vastly different, they both suffer from reliability issues. But if you take a look at the 1984 Mercedes which lies somewhere in between the Ferrari and Geo Metro you get a reliable machine that just keeps running without fail, is easy to repair, and classically elegant.
Let’s talk more specifically about process equipment in modern vs. classic vehicles. Pumps from the 1920s still run because they were designed for rugged performance (without cost analysis). Pumps from the 2020s fail after a few months because they were designed for cost optimization. You get exactly what you pay for, a pump that meets minimum criteria. This is the real reason we need equipment reliability programs today.
Do automation and electronic control reduce reliability?
Electronics don’t make an engine more complicated. The engine still runs with parts such as valves, compression, fuel supply, and an oil filter that’s too hard to reach. Electronics control the engine operating region to keep fragile designs from breaking. So, electronics aren’t the problem. Take my Mini Cooper for example. It has electronic everything and gets better gas mileage in sport mode rather than green. Designs with automation and control systems require a narrow operational band. Outside of those nice manicured conditions, controls are usually the first to stop working, not the machine itself.

“These kids and their new-fangled…” is valid. Unless you have dead-nuts perfect conditions all day every day, your fragile modern equipment will fail. Mechanical seals, boundary fluids, laser alignments, oil mist, lube analysis, metallurgy (as it exists today) didn’t exist 100 years ago because they didn’t NEED to.
Before engineers let accountants, lawyers, admin, marketing, and sales dictate design, world-class reliability just flowed. They understood that reliable performance didn’t come from a reliability-centered maintenance program, vibration monitoring, oil analysis, and predictive analytics. Reliability starts and ends with equipment that was designed to be reliable.
Design according to cost optimization is solving the wrong problem.
Reliable equipment can only be produced from a deep source of understanding, strength, and unity of purpose.
You can’t build anything worthwhile on a cheap foundation.
The Builders
All are architects of Fate,
Working in these walls of Time;
Some with massive deeds and great,
Some with ornaments of rhyme.
Nothing useless is, or low;
Each thing in its place is best;
And what seems but idle show
Strengthens and supports the rest.
For the structure that we raise,
Time is with materials filled;
Our to-days and yesterdays
Are the blocks with which we build.
Truly shape and fashion these;
Leave no yawning gaps between;
Think not, because no man sees,
Such things will remain unseen.
In the elder days of Art,
Builders wrought with greatest care
Each minute and unseen part;
For the Gods see everywhere.
Let us do our work as well,
Both the unseen and the seen;
Make the house, where Gods may dwell,
Beautiful, entire, and clean.
Else our lives are incomplete,
Standing in these walls of Time,
Broken stairways, where the feet
Stumble as they seek to climb.
Build to-day, then, strong and sure,
With a firm and ample base;
And ascending and secure
Shall to-morrow find its place.
Thus alone can we attain
To those turrets, where the eye
Sees the world as one vast plain,
And one boundless reach of sky.
Henry Wadsworth Longfellow (1807-1882)
After all this discussion, we haven’t even touched on Equifactor® and how we, here at TapRooT®, have designed a systematic process to help you solve your equipment reliability issues. No one wants their equipment to fail. Unfortunately, it does. So, do you slap a Band-Aid on it, or do you try and find the real cause of the issue to prevent the equipment from failing again?
Like our good friend Johnny Cash says, “You build on failure. You make it a stepping stone.”
Equifactor® Equipment Troubleshooting and TapRooT® Root Cause Analysis Training
Do you need to efficiently and effectively find the root causes of equipment failures to improve your facility’s equipment reliability? Imagine the downtime prevented, and money saved not having repeat equipment failures. If this sounds interesting (and worthwhile), then this completely revised TapRooT´® Equifactor® course is for you.
The Equifactor® Techniques are based on the work of noted equipment reliability expert Heinz Bloch. The tools can be used by maintenance personnel, equipment reliability specialists, maintenance managers, or investigators who don’t have an extensive understanding of equipment engineering.
Contact us
To further discuss training your employees on-site or at a public course. You may also call us at 865.539.2139 to speak to an instructor, schedule an executive briefing, or book on-site training for your team. We’re here to find solutions for you.