If it ain’t broke, don’t fix it: Maintain it!

“An ounce of prevention is worth a pound of cure.” Not true! When I was running a maintenance and troubleshooting department for US Navy Submarines, the ratio was more like “an ounce of prevention is worth 26.7 pounds of cure.” My cost ratio was 1:427 for one machine. That’s just machine repair costs.
Vital failures that delay operational plants can range in the $100k’s per day. The Kitsap Sun captured what delayed maintenance versus operational schedule looks like in this article from when I was stationed at Bangor NSB. Stop sacrificing equipment reliability to operational schedules.
Disciplined maintenance is how you actually retain not just operational but more importantly, contingent funds.
How much is each hour of your operational schedule worth? Can you even do enough maintenance to match that rate? Did you buy your last unplanned outage at a good cost-benefit?
Equipment failures in any way attributable to poor maintenance put your survival at risk. This is the lowest-hanging fruit. Any threat to maintenance, especially an UNDUE sense of urgency to return to operations, is a threat to your survival. Are you really considering sacrificing sustainability and safety to operations?
Financial scale perspective:
- How many routine PM cards would you have to do to equal the value of a day of ops? How about the length of your last unplanned outage?
- How many PMs equal the value of an injury or death? Ten?
If you don’t have a consistent, repeatable, trend-tracking system for equipment failures, any knowledge you gain even from incident level accidents goes away too quickly to be of much use. Mark Paradies, Founder and President of System Improvements, just recently wrote an article that sums up my sentiment exactly! Mark and Ken both have become priceless mentors to me as I start my Equifactor® journey to learn and develop what actual right looks like.
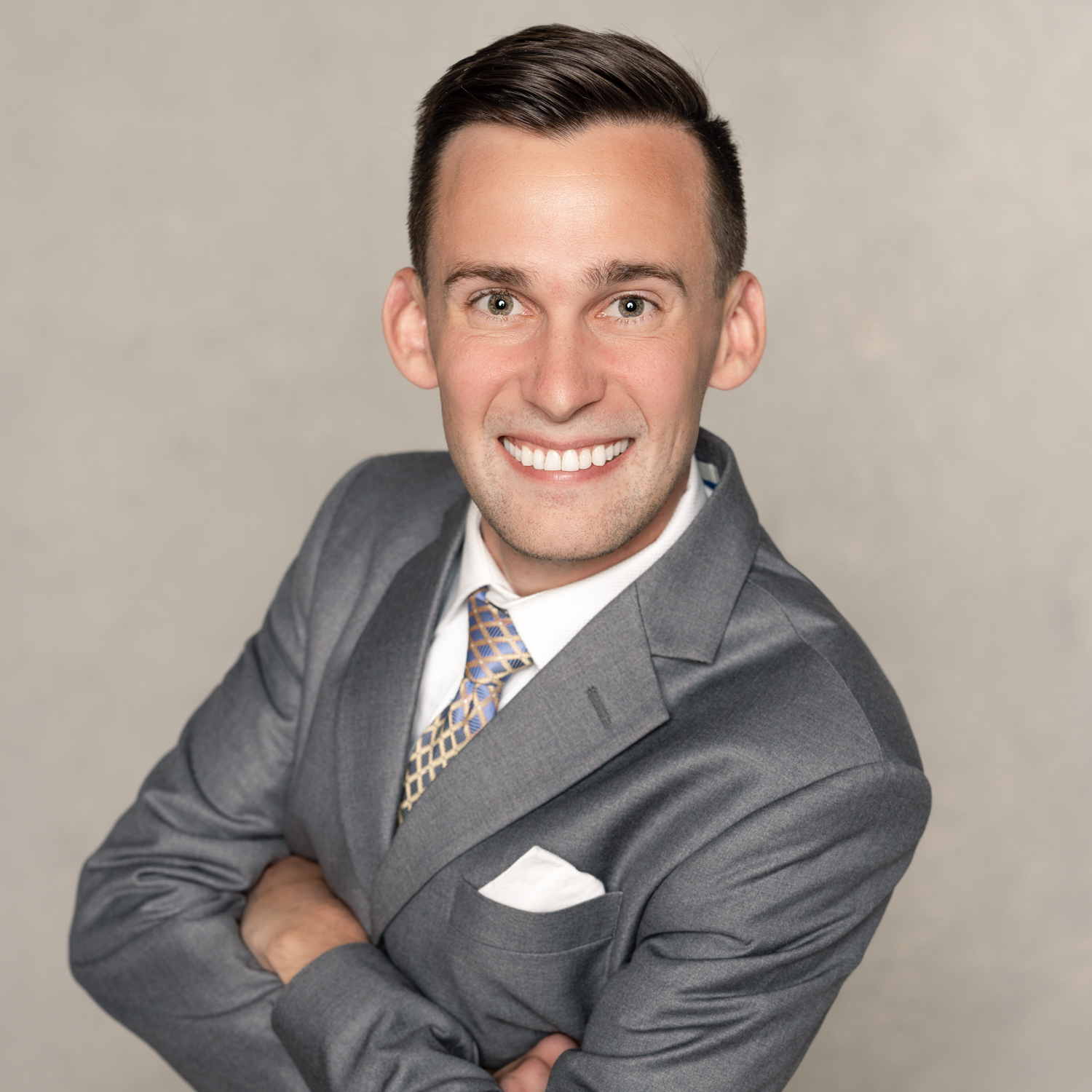
Justin Clark draws on 10 years of operational experience as a nuclear trained US Navy Submarine Officer. He is a Co-Project Manager for the Equifactor® Equipment Troubleshooting module of the TapRooT® software, leveraging extensive leadership and management in equipment operations, reliability, and maintenance. He holds a B.S. in Mechanical Engineering from Kansas State University and resides with his family in Knoxville, Tennessee.