Equipment Failure? Use Equifactor® Troubleshooting During Your Root Cause Analysis
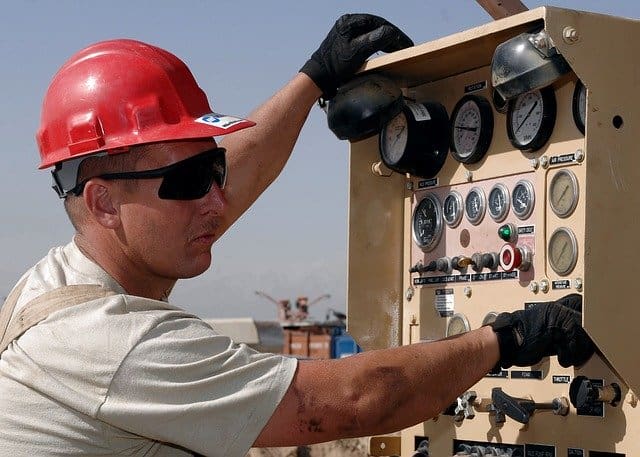
Safety and Quality experts already know that a TapRooT® Root Cause Analysis is the best option to get human-performance-based root causes. It is the only system that uses scientifically derived root causes to eliminate bias and avoid blame. What they don’t know is that the Equifactor® Equipment Troubleshooting Module should be used whenever there is an equipment failure.
When would it be appropriate to use Equifactor®?
First, it is important to understand what it is. This module consists of a series of predefined equipment troubleshooting tables. For example, there are tables for different types of pumps, AC and DC motors, refrigeration units, etc. These tables will give you a list of symptoms to choose from, and then provide an extensive list of possible causes for that symptom. It’s a great way to give your maintenance and reliability experts a terrific list of possible causes to begin their troubleshooting efforts.
So when would you use these Equifactor® tables in your TapRooT® investigation? The tables are obviously a great resource for an equipment failure incident. However, don’t limit yourself to these obvious investigations. For example:
- You can also use Equifactor® during an injury investigation if one of your Causal Factors happens to be an equipment failure.
- Similarly, during an investigation of a Quality deviation, you may find a failure of a piece of equipment on the manufacturing line. Again, it could be employed to better understand the causes of the equipment failure (probably a Causal Factor), which will then lead to a better root cause analysis.
Use Equifactor® anytime an equipment failure is involved in your investigation. It’s a great way to make sure you are fully covering all the possible errors and failures during your TapRooT® analysis.
Learn more
Attend one of our 2-Day TapRooT® / Equifactor® courses. These courses are designed to teach your equipment experts how to use both TapRooT® the Equifactor® module during their investigations. You can register for one of these courses here:
https://store.taproot.com/search?q=Equifactor
Additionally, if you would like to see a demonstration of how it works, check out this video: