Do You Know the Causes of Improperly Installed Equipment?
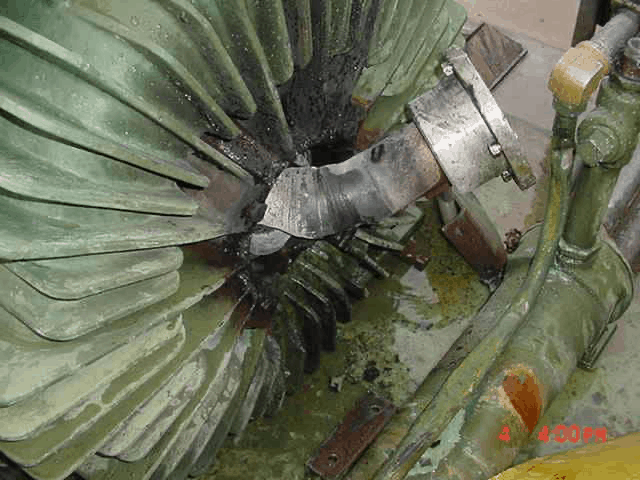
How Big a Problem is “Improperly Installed Equipment?”
Before we discover how to find the causes of improperly installed equipment, let’s look at how big a problem improper installation is.
In a study by Nolan & Heap, they stated that only 11% of equipment failures were due to age. The remainder? Well, if you remember back a few months, we published an article that referenced several articles that said operator error was the #1 cause of equipment failure.
However, in an article by James Kovacevic, he says that in his experience, 65% of the failures are due to improper installation. And of those failures, 36% can be traced back to misalignment or soft-foot conditions.
In the article, James explains misalignment and soft-foot and 7 steps to proper machinery alignment.
Discovering Misalignment During Equipment Troubleshooting
When using the Equifactor Troubleshooting Tables, you may be directed to check if the equipment was properly aligned. Here is an example from one of our exercises in the 2-Day Equifactor® Equipment Troubleshooting and TapRooT® Root Cause Analysis Training…

How would you or the mechanic or the analyst know if the pump was aligned correctly? If the installation was performed using James Kovacevic’s 7 Steps to a Proper Machinery Alignment, you would not only know the process used, you would have documentation and post-installation acceptance testing and verification to ensure that the alignment was at least initially correct. You could then check the alignment (perhaps with laser alignment) to see if the alignment had somehow changed.
Thus, having a systematic process for equipment installation and for equipment troubleshooting and root cause analysis is an extremely important part of achieving world-class equipment reliability.
Discovering the Causes of Improperly Installed Equipment
So, in the example above, we used the Equifactor® Equipment Troubleshooting Tables to guide the mechanic or the incident analyst to the causes of the improper installation (or any other potential problem) by using a process of elimination or selection in a well thought out table.
The cause can then be analyzed to find its root causes using the TapRooT® Root Cause Analysis System.
Where can you learn more about this troubleshooting and root cause analysis process? Start with this article:
https://www.taproot.com/first-step-to-improving-asset-reliability/
Next, see the book:
And the book is included in the course materials for the course:
2-Day Equifactor® Equipment Troubleshooting and
TapRooT® Root Cause Analysis Training

Hope to see you in an upcoming course!